Sunscreen is an essential skincare product used to protect skin from the harmful effects of the sun’s ultraviolet (UV) radiation. Its production involves a careful balance of ingredients, precise formulation, and rigorous testing to ensure it is safe, 有效的, and pleasant to use. Here’s a closer look at how sunscreen is made, from choosing the right ingredients to the final stages of production.
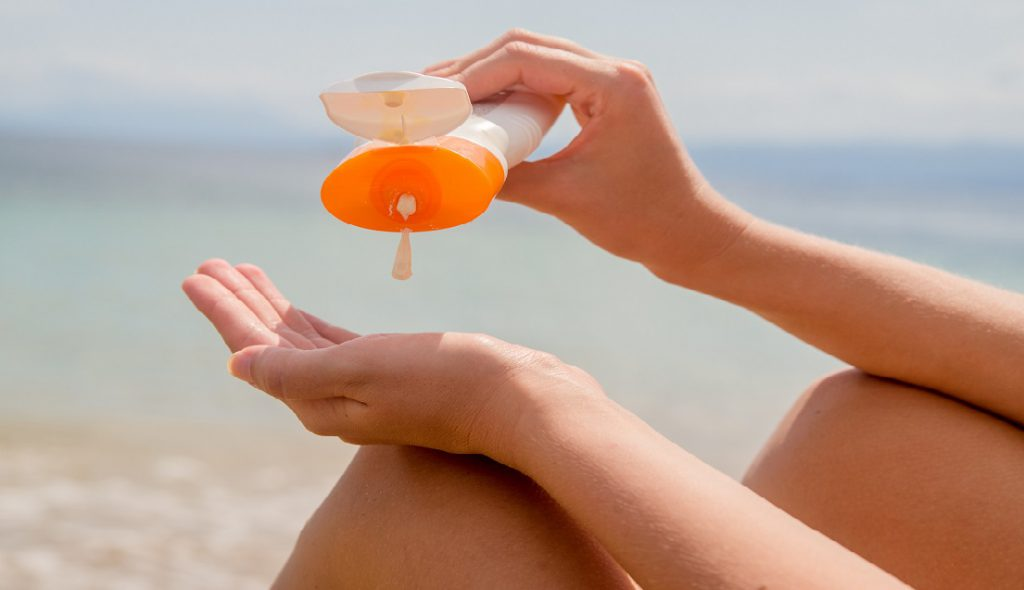
Key Ingredients in Sunscreen
The ingredients in sunscreen are chosen to provide effective sun protection, ensure stability, and improve the product’s feel and spreadability on the skin. There are two main types of active ingredients in sunscreens:
- Physical (Mineral) UV Filters: These ingredients, such as zinc oxide and titanium dioxide, work by reflecting and scattering UV radiation. They sit on top of the skin and offer broad-spectrum protection against both UVA and UVB rays. Mineral sunscreens are often preferred for sensitive skin.
- 化学 (Organic) UV Filters: Chemical filters, like avobenzone, oxybenzone, octinoxate, and octocrylene, absorb UV radiation and convert it into harmless heat, preventing skin damage. Chemical sunscreens are usually lightweight and transparent, making them popular for everyday use.
Other essential ingredients include:
- Emollients and Moisturizers: Ingredients like glycerin, aloe vera, and various oils are added to improve skin hydration and make the sunscreen feel comfortable.
- Stabilizers and Preservatives: These ensure that the product remains stable and effective over time without breaking down or separating. Preservatives also prevent microbial growth.
- 乳化剂: Since many sunscreens are oil-and-water mixtures, emulsifiers help blend these components into a stable, uniform formula.
- Antioxidants: Ingredients like vitamin E and green tea extract are often added to provide additional skin protection against free radical damage caused by sun exposure.
Sunscreen Production Process: Step-by-Step
Producing sunscreen involves several key steps, including formulation, mixing, quality testing, and packaging. Here’s a breakdown of the process in detail:
1. Formulating the Sunscreen
The first step in sunscreen production is formulating a stable, effective product. Formulation scientists select the right combination of active ingredients to achieve the desired SPF (Sun Protection Factor) and broad-spectrum protection. The formulation must also comply with regulatory standards for UV protection and safety in the target market, as some ingredients may be restricted or regulated.
Formulators also work to achieve the desired feel, consistency, and spreadability of the sunscreen, often experimenting with different ratios of ingredients to achieve the right texture and stability.
2. Measuring and Mixing Ingredients
Once the formula is finalized, production begins with carefully measuring each ingredient to ensure accurate proportions. Ingredients are weighed and prepared according to the recipe, which specifies the precise quantities and order of mixing.
The mixing process typically involves the use of industrial mixers. For oil-and-water emulsions (common in sunscreens), both water-based and oil-based ingredients are heated separately to a specific temperature. The two phases are then combined and vigorously mixed using an emulsifier. Mixing machines, like high-shear mixers or homogenizers, are often used to create a stable, smooth emulsion, where the oil and water phases stay evenly blended.
3. Incorporating Active Ingredients
The active ingredients, such as zinc oxide, titanium dioxide, or chemical UV filters, are added during the mixing stage. When using physical (mineral) filters, the particles must be uniformly dispersed to ensure even protection and prevent clumping.
在某些情况下, the active ingredients are pre-micronized (ground into fine particles) to improve their spreadability and feel on the skin. For chemical sunscreens, precise blending is essential to ensure each batch has consistent SPF and protection levels.
4. 乳化
Once the active ingredients and base are combined, the mixture undergoes emulsification. Emulsification is a process that thoroughly blends the oil and water components, creating a smooth, consistent texture. This is crucial because a well-emulsified sunscreen will spread more evenly on the skin, providing uniform sun protection.
Industrial homogenizers are often used in this step to ensure that the sunscreen remains stable, even under high temperatures or extended storage. This process can take several hours, depending on the complexity of the formula and the equipment used.
5. Cooling and Stabilization
After emulsification, the mixture is gradually cooled to room temperature. Cooling must be done slowly to prevent any separation or destabilization of the product. During this stage, stabilizers, antioxidants, and preservatives may be added to maintain the sunscreen’s effectiveness and prolong its shelf life.
Some sunscreens also include fragrance or special skin-conditioning agents, which are usually added during the cooling phase to preserve their potency and effectiveness.
6. Quality Control and Testing
Once the sunscreen is fully mixed and stabilized, it undergoes a series of rigorous quality control tests to ensure it meets industry standards for SPF and safety. The most important tests include:
- SPF Testing: To confirm that the sunscreen provides the advertised level of protection, SPF tests are conducted in both lab settings and sometimes on human subjects. Regulatory bodies often have specific requirements for SPF testing, which must be followed for compliance.
- Stability Testing: This involves subjecting the sunscreen to different temperatures and environmental conditions to ensure it remains stable and effective over time. Stability testing helps determine the product’s shelf life.
- Microbial Testing: Sunscreens are tested for microbial contamination to ensure they’re safe for use and free of harmful bacteria or fungi. Preservatives are checked for effectiveness to maintain long-term product safety.
- Patch Testing and Skin Irritation Tests: These tests check for potential skin irritation or allergies, especially for sensitive formulas. Dermatological testing is especially important for sunscreens marketed for sensitive skin.
7. Filling and Packaging
After passing all quality control tests, the sunscreen is ready for packaging. Sunscreen can be packaged in tubes, 瓶子, spray containers, or jars, depending on the product design and marketing preferences. Automated filling machines ensure accurate, hygienic filling of each container, preventing contamination and maintaining product consistency.
Sunscreens are typically filled in controlled environments to ensure hygiene and quality. Once filled, the containers are sealed, labeled, and batch-coded to track production details for quality control and regulatory compliance.
Manufacturing Equipment in Detail
The quality of sunscreen depends significantly on the manufacturing equipment used:
High-Shear Mixers
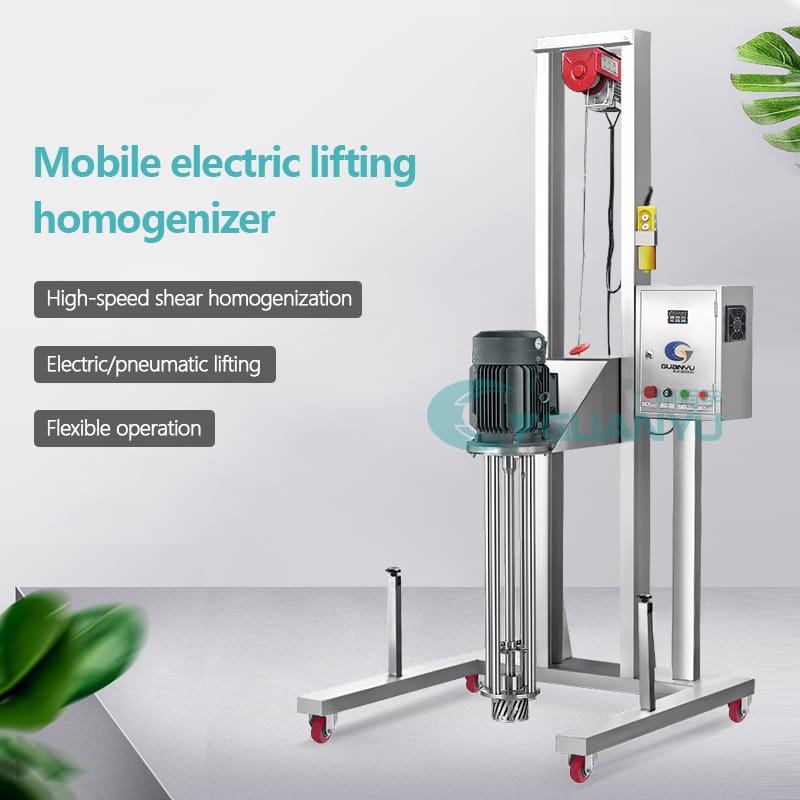
High-shear mixers are pivotal in the sunscreen manufacturing process. They are designed to effectively blend, emulsify, and disperse the various ingredients used in sunscreen formulations.
These mixers work by applying intense shear forces, crucial for breaking down particle agglomerates, ensuring even distribution of UV filters, and achieving a smooth texture.
Their ability to mix ingredients thoroughly ensures that the active ingredients are evenly distributed throughout the product, which is essential for consistent sun protection.
Vacuum Emulsifiers
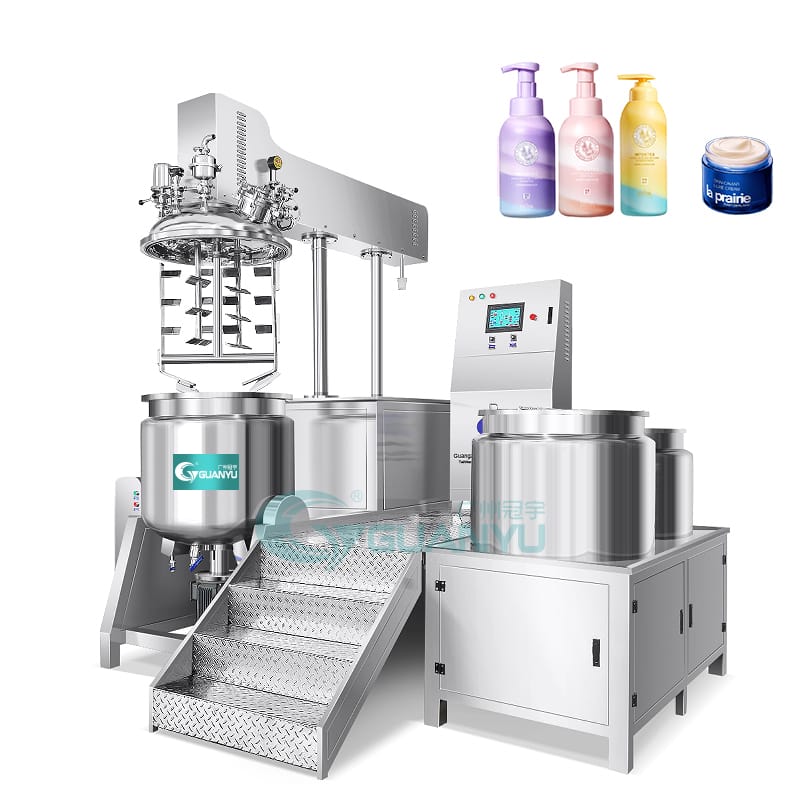
Vacuum emulsifiers play a crucial role in creating stable and uniform emulsions, which are the foundation of most sunscreen lotions and creams.
These machines work under vacuum conditions to prevent air incorporation, which is vital for achieving a stable emulsion and ensuring product longevity.
The vacuum environment also helps in reducing oxidative degradation of sensitive ingredients, such as certain organic UV filters and antioxidants, thus maintaining the efficacy and safety of the sunscreen product.
Filling Machines
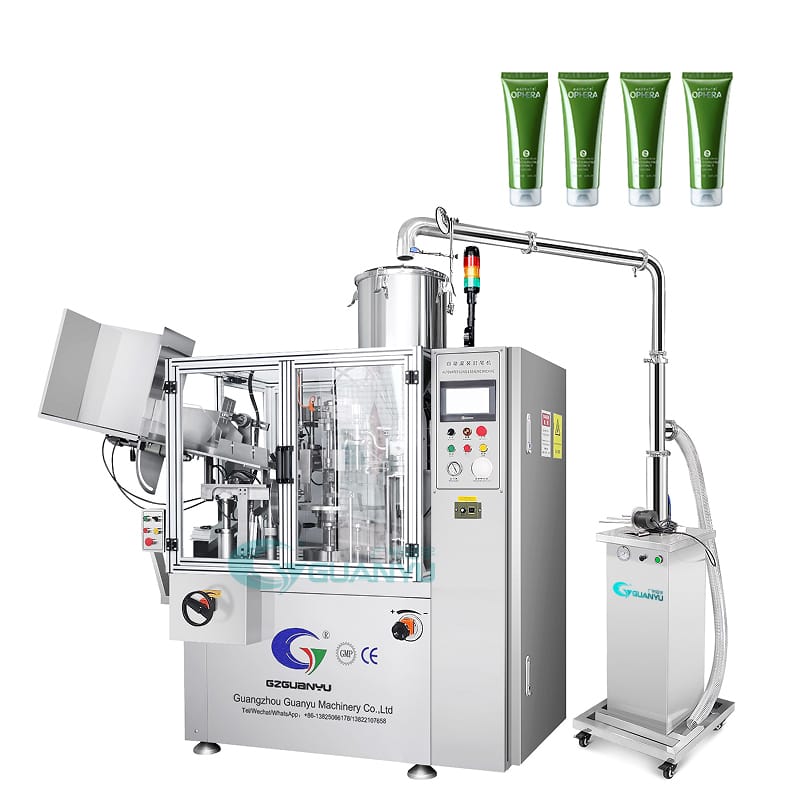
Filling machines in sunscreen production are designed for precision and efficiency. They ensure that each container of sunscreen, whether it’s a bottle, 管子, or spray, is filled with the exact amount of product.
This accuracy is critical not only for consumer satisfaction but also for regulatory compliance, as the labeled quantity must match the actual content. Modern filling machines are equipped with advanced technologies that can handle different viscosities and types of sunscreen formulations, ensuring consistent product quality.
Sealing and Labeling Equipment
Sealing and labeling equipment are the final steps in the sunscreen manufacturing process, and they are as important as the initial stages.
Sealing machines ensure that the packaging is securely closed to maintain the product’s integrity and prevent contamination. Proper sealing is crucial for preserving the product’s efficacy and shelf life.
Following sealing, labeling equipment is used to apply labels that provide essential information, including SPF rating, 原料, 使用说明, and regulatory compliance details. This information is vital for consumers t
Types of Sunscreen Formulations
There are various types of sunscreen formulations designed for different skin types, 应用, and user preferences:
- Creams and Lotions: These are the most common types of sunscreens, offering a thick, creamy consistency that spreads easily on the skin. They are ideal for people with dry or normal skin.
- Gels: Gel-based sunscreens are lighter and often alcohol-based, making them more suitable for oily or acne-prone skin.
- Sprays: Spray sunscreens are convenient and quick to apply, especially for hard-to-reach areas. 然而, they require careful application to ensure even coverage.
- Sticks: Sunscreen sticks are compact and convenient for on-the-go application, often used on small areas like the face and lips.
- Tinted Sunscreens: Tinted sunscreens provide sun protection along with a hint of color, acting as a light foundation or concealer for the skin.
Regulatory Compliance and Safety Standards
Sunscreen production is highly regulated by authorities such as the U.S. Food and Drug Administration (FDA) in the United States, the European Medicines Agency (EMA) in Europe, and similar agencies worldwide. Sunscreens are often classified as over-the-counter (OTC) drugs, which means they must meet strict regulatory requirements for labeling, SPF accuracy, and safety.
Manufacturers must adhere to Good Manufacturing Practices (良好生产规范) and ensure that each product batch meets safety and efficacy standards. This includes listing all active ingredients, providing proper labeling, and following guidelines for SPF claims.
结论
The production of sunscreen is a complex process that requires careful formulation, advanced equipment, and stringent quality control to ensure that the product effectively protects the skin from UV radiation while being safe and pleasant to use. Each stage—from ingredient selection to packaging—is critical in creating a product that meets consumer expectations for both efficacy and aesthetics.
With increased awareness about sun protection and skin health, the demand for high-quality sunscreens continues to grow. Manufacturers must stay up-to-date with regulatory changes, technological advancements, and consumer preferences to remain competitive in this important industry.
For an effective ChatGPT alternative to support content creation or SEO writing needs, you can try HIX.AI.
Muchas gracias. ?Como puedo iniciar sesion?