Introduction to Powder Mixing Machines
Powder mixing machines play a crucial role in a variety of industries, 包括药品, 食品加工, 和化学制造. These machines are designed to create a homogeneous blend of powdered materials, ensuring consistent quality in end products. The demand for effective mixing solutions has led to significant advancements in technology, resulting in machines that offer enhanced performance and efficiency. The significance of these machines cannot be overstated, as precise mixing is essential for product integrity, 稳定, and application.
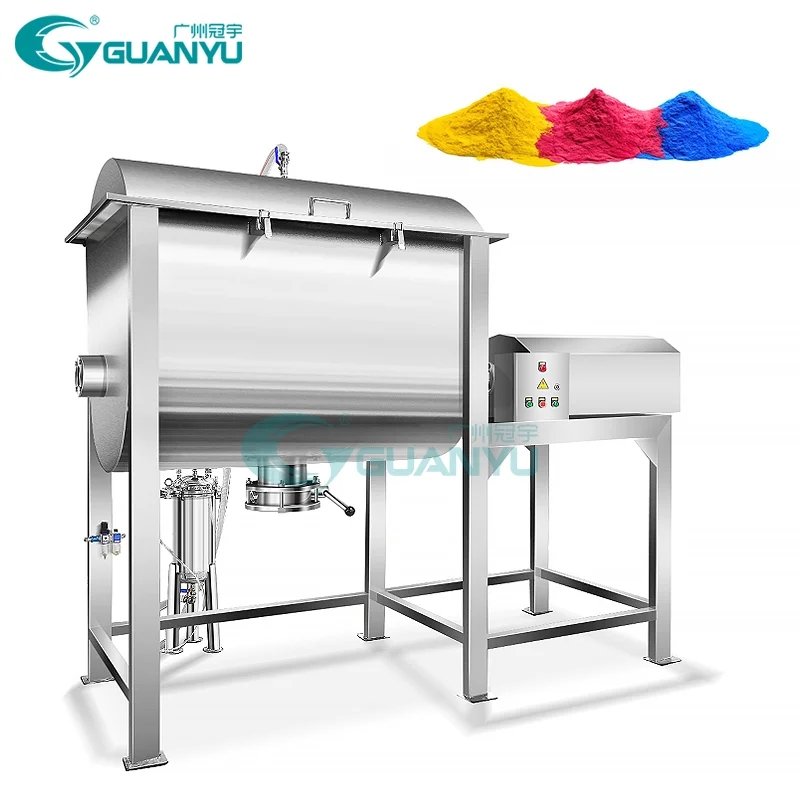
In general, the basic functionality of powder mixing machines involves the incorporation of various dry materials into a uniform mixture. Depending on the specific application and material characteristics, different mixing technologies can be employed, such as ribbon mixers, V-blenders, 还有更多. 然而, the U-shape tank bottom powder mixing machines have emerged as a notable innovation within this domain. The design of these mixers features a distinct U-shaped tank that not only facilitates efficient material mixing but also optimizes material discharge. This is particularly advantageous in reducing product waste and enhancing operational efficiency.
One of the defining features of U-shape tank bottom mixers is their ease of cleaning, setting them apart from traditional mixing equipment. The design allows for smooth surfaces and minimal crevices, simplifying the cleaning process between batches. This characteristic is essential for industries where cross-contamination could pose significant risks, such as in pharmaceutical manufacturing. Consequently, the U-shape tank design not only improves the overall mixing quality but also reinforces compliance with stringent hygiene standards. As the demand for high-quality mixing solutions continues to grow across various sectors, the U-shape tank bottom powder mixing machine stands out as a vital component in the evolution of material processing technology.
The U-Shape Tank Bottom Design: Benefits Explained
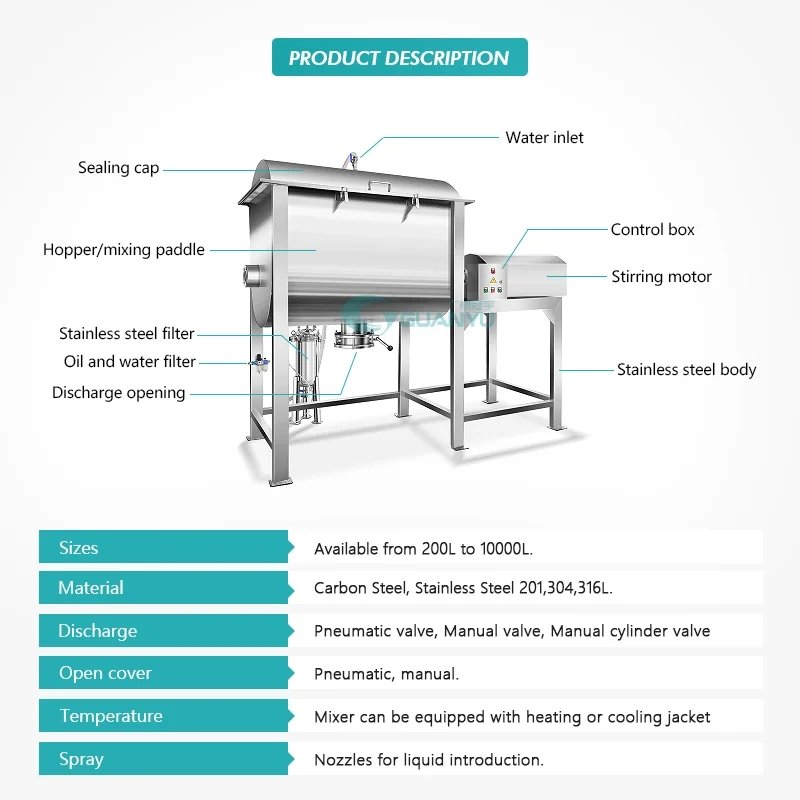
The U-shape tank bottom design in powder mixing machines provides numerous advantages that significantly improve the material mixing process. One of the primary benefits of this design is its ability to facilitate optimal material movement within the tank. The U-shape encourages a flow pattern that allows powders to move more freely compared to traditional flat-bottom tanks. This enhanced mobility ensures that materials are adequately mixed, resulting in a more homogeneous blend. Such efficiency is crucial for industries that require consistent product quality and uniformity.
此外, the U-shape tank bottom design plays a vital role in minimizing product wastage during the discharge process. The contours of the tank effectively guide the materials towards the outlet, ensuring that even the smallest quantities are efficiently removed from the tank. This capability is particularly beneficial in operations where material cost is a critical factor, as it maximizes every drop of the expensive ingredients. By significantly reducing the amount of residual product left behind, manufacturers can improve overall yield and profitability.
Another critical aspect of the U-shape tank design is its synergy with the dual screw structure commonly found in these machines. This combination enhances the mixing efficiency, allowing the dual screws to create a more intensive blending action. As the screws work in tandem, they draw materials towards the center of the tank, promoting thorough mixing and preventing the formation of dead zones. The result is a uniform distribution of all components, vital for applications that require precise ratios of mixed materials.
全面的, the U-shape tank bottom design stands out as an innovative solution that optimizes both material handling and mixing efficiency. By leveraging its strengths, manufacturers can ensure superior product quality with reduced waste and increased operational effectiveness.
Dual Screw Structure: Enhancing Mixing Efficiency
The dual screw structure is a significant innovation in the design of U-shape tank bottom powder mixing machines, contributing substantially to the overall mixing efficiency. This configuration typically consists of two independently rotating screws that work in tandem to create a highly effective mixing environment. The dual screws facilitate the simultaneous movement of materials in multiple directions, which optimizes the distribution of powders and minimizes the likelihood of segregation.
One of the major advantages of the dual screw design is its ability to generate a dynamic mixing action. As the screws rotate, they not only transport materials along the length of the tank but also impart shear forces that enhance the inter-particle interaction. This results in a more uniform blend of materials, crucial for industries relying on precise formulations, 例如药物, 食品加工, 和化学制造. 而且, the enhanced mixing action enables the effective blending of a wide variety of powder types, including cohesive, granular, and ultra-fine materials.
In addition to improving the quality of the mixture, the dual screw structure significantly reduces the overall mixing time. Traditional mixing machines may require prolonged operational cycles to achieve a homogenous blend. 然而, the innovative dual screw mechanism allows for quicker mixing processes, thereby enhancing operational efficiency. Users can benefit from shorter production cycles while maintaining or even improving the quality of their final products.
The versatility of the dual screw system also extends to various applications beyond simple powder mixing. Its design can accommodate different material characteristics, moisture content, and bulk density variations, making it suitable for diverse industrial environments. 最终, the dual screw structure represents a quantum leap in mixing technology that ensures efficient, fast, and uniform material blending.
Cleaning and Maintenance Advantages of U-Shape Tank Bottom Machines
The design and construction of U-shape tank bottom powder mixing machines present significant advantages when it comes to cleaning and maintenance. One of the primary benefits of this innovative design is the ease of access provided for cleaning operations. Unlike traditional mixing machines, the U-shape configuration allows operators to reach all areas of the tank without the need for complex disassembly. This easy access is crucial for ensuring that all residues, including powders and liquids, are thoroughly removed after each use—thereby promoting hygiene and safety standards in manufacturing processes.
此外, the smooth interior surface of the U-shape tank minimizes the risk of material sticking to the sides, which is a common challenge with other mixing machines. This feature not only improves the efficiency of cleaning routines but also extends the longevity of the equipment by reducing the wear associated with stubborn residue buildup. Regular maintenance is essential for optimal performance, and the U-shape tank’s design facilitates straightforward inspections and servicing tasks.
To ensure that U-shape tank bottom powder mixing machines perform at their best, several best practices can be employed. 第一的, establishing a routine cleaning schedule allows operators to maintain hygiene effectively and can help in identifying wear and tear on components early. Second, using appropriate cleaning agents that do not corrode or damage the machine’s surfaces is critical in prolonging its lifespan. Lastly, regular lubrication of moving parts and periodic checks on seals and gaskets can prevent operational failures and costly downtimes. Following these practices ensures that the U-shape tank bottom machines remain in optimal condition, delivering reliable and effective mixing while upholding stringent hygiene requirements.