Introduction to Shampoo Production
The production of shampoo is an essential process within the personal care industry, providing consumers with various products designed to cleanse and nourish the hair and scalp. As a multi-billion dollar market, the significance of shampoo extends beyond mere cleansing; it incorporates aspects of hair health, beauty standards, and consumer preferences. The evolution of shampoo from simple soap infusions to sophisticated formulations demonstrates the intricate interplay of chemistry and technology in personal care.
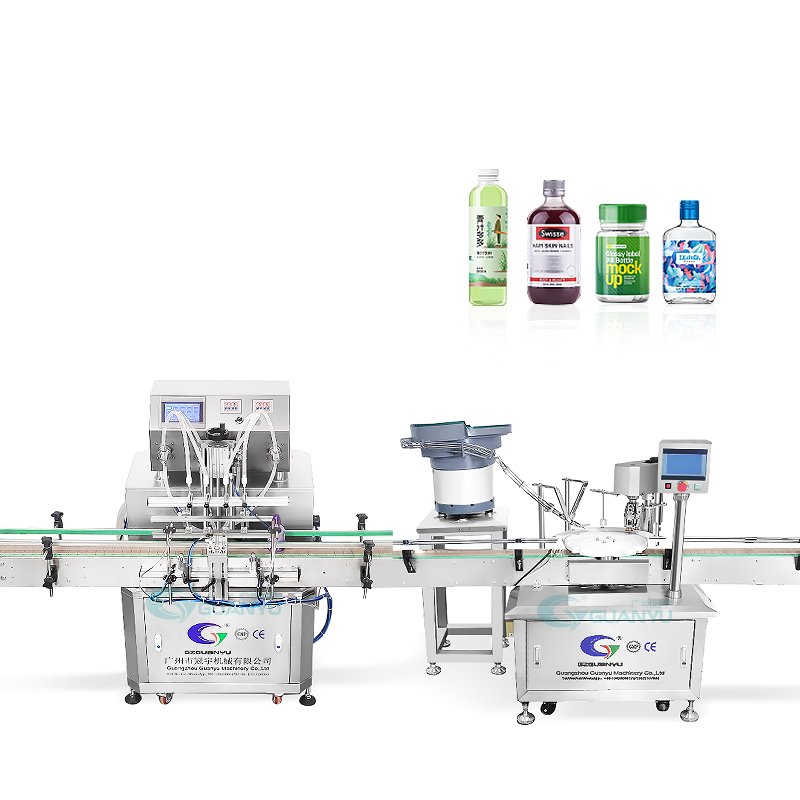
Shampoo manufacturing encompasses a series of meticulous steps carried out to ensure the final product adheres to safety and efficacy standards. The production process typically begins with the careful selection of raw ingredients, which may include surfactants, thickeners, conditioning agents, and fragrances. These components are chosen not only based on their cleansing capabilities but also for their ability to deliver various benefits such as moisture retention, shine enhancement, and scalp health improvement.
The process of creating shampoo involves mixing these raw materials using specialized equipment designed to accommodate the unique characteristics of liquid formulations. Equipment such as agitators, mixers, and emulsifiers come into play to ensure a homogenous blend, which is vital for consistent product quality. Following the mixing phase, further processes such as heating, cooling, and quality control tests are carried out. This careful sequence ensures that the final product meets the industry standards and fulfills consumer expectations for performance and safety.
In summary, understanding the intricacies of shampoo production reveals not only the technological advancements that have impacted the industry but also highlights the importance of quality control throughout the manufacturing process. As we delve deeper into the specific equipment and stages involved, it becomes evident how each element contributes to the creation of effective and appealing shampoo products that cater to a diverse range of consumer needs.
Essential Ingredients in Shampoo
Shampoo production involves a careful selection of ingredients, each serving a specific purpose to ensure effective cleansing, conditioning, and enhancement of hair quality. Among the key components are surfactants, thickeners, preservatives, and fragrances. Understanding their functions is vital for producing a high-quality shampoo that meets consumer expectations.
Surfactants, derived from both natural and synthetic sources, are the primary cleaning agents in shampoo formulations. They effectively reduce surface tension, allowing water to interact with oils and dirt on the scalp and hair, facilitating their removal. Common surfactants include sodium lauryl sulfate (SLS) and sodium lauryl ether sulfate (SLES). While they are effective cleansers, there has been an increasing demand for gentler alternatives, such as sulfate-free surfactants, to cater to sensitive skin and minimize irritation.
In addition to surfactants, thickeners are essential for achieving the desired texture and viscosity in shampoo formulations. Ingredients such as xanthan gum and hydroxyethylcellulose are often used to create a pleasing consistency, ensuring that the product is easy to dispense and apply. These thickeners also contribute to the overall stability of the formulation, preventing separation during storage.
Preservatives play a crucial role in extending the shelf life of shampoos by preventing microbial growth. Without effective preservatives, shampoos can become unsafe and ineffective over time. Parabens, phenoxyethanol, and ethylhexylglycerin are commonly used preservatives, although there is a growing trend toward utilizing natural preservatives to cater to consumer preferences for clean beauty products.
Finally, fragrances are added to enhance the sensory experience of using shampoo. They contribute to the overall appeal of the product; however, it’s essential to ensure the fragrances used meet safety standards and do not trigger allergic reactions. The balance of these ingredients is critical for formulating shampoos that are not only effective but also safe for consumers.
Overview of Shampoo Manufacturing Equipment
Shampoo manufacturing is a complex process that necessitates a variety of specialized equipment to ensure the production of high-quality products. The core machinery utilized in this industry consists of mixers, homogenizers, mills, filling machines, and packaging systems, each serving a distinct function in the overall manufacturing process.
Mixers are fundamental pieces of equipment in shampoo production, as they facilitate the blending of various raw ingredients, including surfactants, conditioners, and fragrances. These machines are designed to ensure uniform dispersion of ingredients, which is critical for maintaining consistency and effectiveness in the final product. The efficiency of the mixer directly influences the quality of the shampoo, making it a crucial stage in the manufacturing line.
Homogenizers play a vital role in ensuring that the shampoo achieves the desired viscosity and texture. By subjecting the blend to high pressure, homogenizers break down particles into smaller sizes, leading to a more stable emulsion. This process not only enhances the product’s appearance but also its performance, directly impacting consumer satisfaction.
Another essential element in shampoo production is the milling machine, which is used to refine and reduce the particle size of solid ingredients. This step is particularly important for achieving a smooth and appealing product. Like mixers and homogenizers, the milling process contributes to the overall quality and consistency of the shampoo.
Once the shampoo is adequately formulated, filling machines commence the packaging process, ensuring that the product is accurately measured and sealed in containers. These machines operate with precision to prevent spills and waste, maintaining efficiency in the final stages of production. Packaging systems also play a role in branding and market presentation, as they are designed to attract consumers while protecting the integrity of the product.
In conclusion, understanding the various types of equipment used in shampoo production is essential for grasping the intricacies of the manufacturing process. Each machine plays a significant role in ensuring that the product meets quality standards and consumer expectations.
Shampoo Mixer: The Heart of the Production Process
The shampoo mixer plays a crucial role in the production of shampoo, serving as the heart of the entire process. Its primary function is to blend the various components effectively, creating a uniform emulsion that is essential for the performance and stability of the final product. Mixing different ingredients such as surfactants, emulsifiers, thickeners, and fragrances requires precision and control, which industry-grade blenders provide. These mixers are designed to accommodate the specific needs of shampoo formulation, ensuring that all components are evenly distributed throughout the mixture.
One of the key features of shampoo mixers is their ability to handle a wide range of viscosities. This characteristic is particularly important as shampoo formulations vary significantly in thickness. High-shear mixers and homogenizers are commonly used in the industry, as they create a strong mechanical force that helps to disperse solids and dissolve powders rapidly. Additionally, these mixers can manage temperature variations, which is vital when heat-sensitive ingredients are involved in the formulation.
Design-wise, shampoo mixers often include various elements such as agitators, baffles, and distinct mixing chambers that enhance the blending process. Agitators are designed to create turbulence within the mixture, promoting uniform distribution while minimizing air incorporation. Baffles, on the other hand, help to optimize flow patterns, thereby allowing more efficient mixing. Furthermore, the compatibility of the mixer with cleaning and maintenance protocols is essential, as hygiene plays a significant role in the manufacturing of personal care products.
Choosing the right type of shampoo mixer is vital for achieving the desired consistency and quality of the final product. Factors such as batch size, formulation complexity, and production scale influence which mixer is most suitable. Industry professionals must carefully evaluate these aspects to ensure optimal mixing processes, ultimately leading to a high-quality shampoo that meets consumer expectations.
Heating and Cooling Equipment in Shampoo Production
In the realm of shampoo production, temperature control plays a pivotal role in ensuring product quality and consistency. The heating and cooling equipment utilized during the manufacturing process directly influences the mixing and emulsification stages, both of which are critical to achieving a stable emulsion and the desired final product. The ability to manipulate temperature effectively is essential for dissolving ingredients, activating certain compounds, and promoting uniform consistency.
The primary equipment used for heating includes jacketed vessels, steam-heated kettles, and thermal fluid heating systems. Jacketed vessels are particularly effective as they provide a controlled environment in which heat can be applied uniformly. This method ensures that the temperature is consistent throughout the mixture, which is vital for dissolving solid ingredients and ensuring that additives are thoroughly integrated into the formulation. Steam-heated kettles can rapidly increase the temperature of the product, allowing for a quick transition through the heating phase, while thermal fluid systems provide a reliable means for heating without direct contact between the heating source and the product itself.
Cooling is equally essential in the shampoo production process to prevent overheating that might damage sensitive ingredients. Equipment such as chillers and heat exchangers are essential for quickly lowering the temperature of the product post-emulsification, ensuring that it stabilizes effectively. Chillers utilize refrigerants or water to absorb heat from the mixture, while heat exchangers allow for efficient heat transfer, maintaining the desired temperature with precision. The integration of both heating and cooling systems ensures that each batch of shampoo meets the necessary standards for quality and safety.
In conclusion, the deliberate management of heating and cooling equipment is pivotal in shampoo production, as it directly affects the properties of the final product. Effective temperature control is not merely an operational necessity; it is a fundamental aspect of crafting high-quality shampoos that satisfy consumer expectations.
Emulsifiers and Their Applications
Emulsifiers play an essential role in shampoo production, serving as stabilizing agents that help maintain a uniform mixture of water and oil in formulations. Within the context of shampoos, the primary function of an emulsifier is to prevent the separation of hydrophilic (water-attracting) and lipophilic (oil-attracting) ingredients. This is crucial for ensuring the efficacy and aesthetic appeal of the final product, as a stable emulsion enhances texture and application properties.
In the realm of shampoo production, emulsifiers can be classified into two main categories: anionic and non-ionic emulsifiers. Anionic emulsifiers, which carry a negative charge, are often used in formulas designed for cleansing and degreasing. Sodium laureth sulfate (SLES) is a widely recognized example of an anionic emulsifier that not only helps to emulsify oils but also contributes to the shampoo’s foaming characteristics. On the other hand, non-ionic emulsifiers, which are neutral in charge, are favored for their ability to provide stability without impacting the pH of the shampoo. Ingredients such as glyceryl stearate and cetyl alcohol fall into this category and are commonly utilized for their mildness and moisturizing qualities.
The selection of emulsifiers can significantly influence the performance attributes of the shampoo. For instance, the use of polysorbates enhances the ability of the formulation to mix with water, thereby supporting a smoother application experience. In contrast, more specialized emulsifiers, like cationic agents, can be incorporated into conditioning shampoos to provide added benefits, such as improved hair manageability and softness. Therefore, understanding the diverse types of emulsifiers and their respective functions is critical to developing effective shampoo formulations that meet consumer needs.
Packaging Machines and Their Importance
The packaging of shampoo is an integral part of the production process, impacting not only the presentation and shelf life of the product but also consumer appeal. Various types of packaging machinery are utilized in the production of shampoo, each playing a crucial role in ensuring efficiency and product integrity. The most common machines involved in the packaging process include filling machines, capping machines, labeling machines, and cartoning machines. Each of these machines serves a distinct function to prepare the product for distribution.
Filling machines are essential for accurately dispensing the shampoo into bottles, ensuring that each container is filled to the correct volume. This precision helps maintain product consistency, which is vital in retaining customer trust and satisfaction. Additionally, capping machines securely seal the bottles to prevent leaking and contamination, thus extending the shampoo’s shelf life. The use of both filling and capping machines enhances the efficiency of the production line by automating processes that would otherwise require significant manual labor.
Labeling machines, on the other hand, are responsible for applying labels to the bottles, offering vital information such as ingredients, usage instructions, and branding. An appealing label design not only informs consumers but also enhances the product’s aesthetic appeal on retail shelves, influencing purchasing decisions. Finally, cartoning machines package the filled and labeled bottles into boxes, making transportation and storage easier while ensuring they arrive at retailers in pristine condition.
Overall, efficient packaging is crucial for large-scale shampoo production. High-quality packaging not only protects the product but also actively engages consumers, thereby driving sales. As such, manufacturers must carefully select packaging machinery that meets their production needs and aligns with market trends, ultimately contributing to the viability and success of the shampoo in a competitive market.
Quality Control Measures in Shampoo Production
In the realm of shampoo production, quality control is a critical component that assures consumers of product safety and effectiveness. Quality assurance begins with the selection of ingredients, where raw materials are evaluated for purity and consistency. Suppliers must meet stringent standards, providing comprehensive documentation that guarantees the quality of their products. A thorough assessment of ingredients is essential, as these foundational elements directly impact the final product’s performance.
Once the ingredients are acquired, the production process incorporates several machinery and testing methodologies to maintain quality. The first step involves measuring the viscosity of the shampoo, which is vital for determining the product’s texture and usability. This is typically accomplished using viscometers that provide precise readings during various stages of production. Maintaining the correct viscosity ensures that the shampoo is neither too runny nor excessively thick, enhancing user experience.
pH levels are another crucial parameter monitored during shampoo production. The ideal pH range for shampoos typically falls between 4.5 to 5.5, aligning closely with the natural acidity of the scalp and hair. Automated pH meters are employed in laboratories to ensure that the formulation remains within this range. If pH results fall outside the acceptable limits, adjustments are necessary before proceeding to the next phase of production.
Finally, overall product efficacy is evaluated through stability and compatibility testing. Samples undergo long-term storage tests to observe how they respond over time to changes in temperature and light exposure. Additionally, consumer testing can provide valuable feedback on performance attributes, such as lathering ability, cleansing effectiveness, and scent appeal. Together with these rigorous testing protocols, shampoo producers can confidently assure consumers that their products meet industry standards and deliver the promised benefits.
Conclusion and Future Trends in Shampoo Manufacturing
In summary, shampoo production is a multifaceted process that involves a diverse array of machines and dedicated methodologies designed to ensure product quality and safety. As has been discussed, the manufacturing process includes ingredient formulation, mixing, bottling, and quality control measures that are vital to the final product’s integrity. The equipment used, ranging from mixers to filling machines, plays a critical role in maintaining consistency and efficacy in shampoo production.
Looking forward, the future of the shampoo manufacturing industry is poised for considerable transformation, primarily influenced by the increasing demand for sustainability and eco-friendly practices. Eco-conscious consumers are increasingly driving brands to innovate their product lines by integrating biodegradable materials and reducing water usage during production. This trend is evident in the rising popularity of solid shampoos and refillable packaging options that minimize waste and carbon footprints.
Moreover, advancements in technology continue to pave the way for innovative manufacturing techniques. Automation and artificial intelligence are emerging as pivotal players in streamlining production processes, enhancing efficiency, and improving product personalization. These technologies allow brands to respond quickly to consumer trends, creating tailored formulations that cater to specific hair concerns while adhering to environmental standards.
Furthermore, the development of green chemistry offers promising opportunities for the formulation of shampoos that are both effective and environmentally benign. This approach minimizes the use of hazardous substances and promotes the utilization of renewable resources, aligning with the global sustainability movement. As these trends evolve, it is essential for manufacturers to remain adaptable, embracing new technologies and methodologies that not only enhance product performance but also align with consumer preferences for ethical and sustainable beauty solutions.
awesome