Steam Heating
Steam heating offers a range of benefits for mixing machines, making it a widely used method in various industrial applications. One of the primary advantages of steam heating is its ability to provide rapid and consistent temperature control. This is particularly useful in processes that require precise thermal management, such as chemical reactions or pharmaceutical production. Steam can quickly reach high temperatures and maintain them consistently, ensuring uniform heating throughout the mixing process.
Another significant benefit of steam heating is its efficiency. Steam transfers heat through condensation, which is a highly effective method of heat exchange. This results in faster heating times compared to other methods, such as electric heating. Adicionalmente, steam heating systems can be easily integrated into existing steam infrastructure, making it a cost-effective choice for facilities that already use steam for other processes.
No entanto, steam heating is not without its drawbacks. One major disadvantage is the need for a boiler system, which can be expensive to install and maintain. Boilers require regular inspections and maintenance to ensure safe and efficient operation. Além disso, steam systems can pose safety hazards, including the risk of steam leaks and burns, which necessitates stringent safety protocols and training for personnel.
Steam heating is particularly suitable for situations that demand high-temperature processes. Industries such as food and beverage, produtos farmacêuticos, and chemicals often require precise thermal control and rapid heating, making steam an ideal choice. Por exemplo, in the food processing industry, steam is used to achieve the necessary temperatures for pasteurization and sterilization, ensuring product safety and quality.
Case studies illustrate the effectiveness of steam heating in various applications. Por exemplo, a pharmaceutical company might use steam heating in the production of active pharmaceutical ingredients (APIs), where maintaining a specific temperature is crucial for chemical stability and efficacy. Similarly, a chemical manufacturing plant could rely on steam heating for processes that require consistent high temperatures, such as distillation or polymerization.
Para concluir, while steam heating offers rapid heating times and consistent temperature control, it also requires a boiler system and poses potential safety hazards. It is best suited for industries that require high-temperature processes or already have steam infrastructure in place.
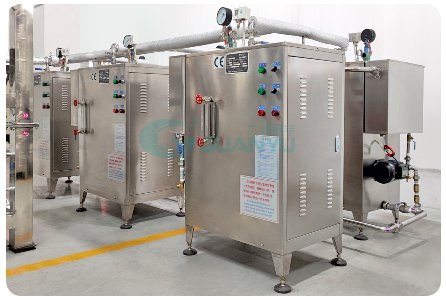
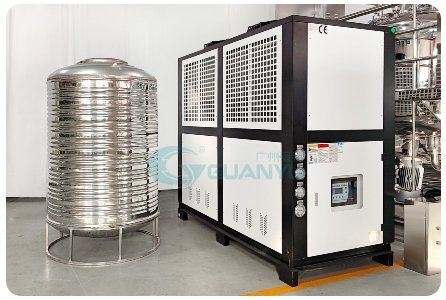
Electric Heating for your mixing machine
Electric heating presents several advantages when used in mixing machines. One of the foremost benefits is the precise temperature control it offers. Unlike steam heating, which can be subject to fluctuations, electric heating systems enable consistent and accurate temperature settings, which is particularly crucial in processes requiring exact thermal conditions.
Adicionalmente, electric heating is known for its ease of installation. The convenience of integrating electric heating elements into existing systems without extensive modifications makes it an attractive option. This is especially beneficial in facilities where space constraints or infrastructure limitations make other heating methods less feasible.
Another significant advantage is the lower maintenance requirements associated with electric heating. These systems generally have fewer moving parts compared to steam heating setups, translating to reduced wear and tear and longer intervals between maintenance activities. This can result in lower long-term operational costs and minimized downtime, enhancing overall productivity.
No entanto, electric heating does have its drawbacks. One of the primary disadvantages is the higher operational costs. Electricity can be more expensive than other energy sources, which may impact the overall cost-efficiency of the mixing process, especially in large-scale operations. Adicionalmente, electric heating systems often have slower heating times compared to steam heating, which may be a consideration for processes requiring rapid temperature changes.
Electric heating is particularly suitable in scenarios where precise temperature control is paramount. Por exemplo, in pharmaceutical or food processing industries, where maintaining specific temperatures is critical for product quality and safety, electric heating can be the optimal choice. Além disso, environments lacking steam infrastructure, such as remote locations or smaller facilities, may find electric heating a more practical solution.
Practical examples include its use in laboratory-grade mixing machines where precision is non-negotiable, and in small-scale production units where installing a steam infrastructure would be impractical or cost-prohibitive. By understanding the specific requirements and constraints of your operation, you can determine if electric heating is the right choice for your mixing machine needs.
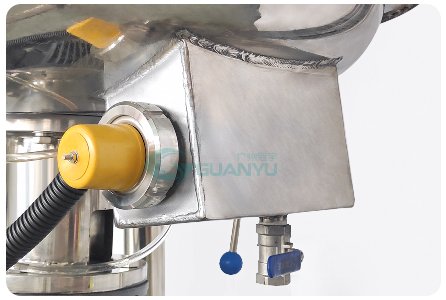
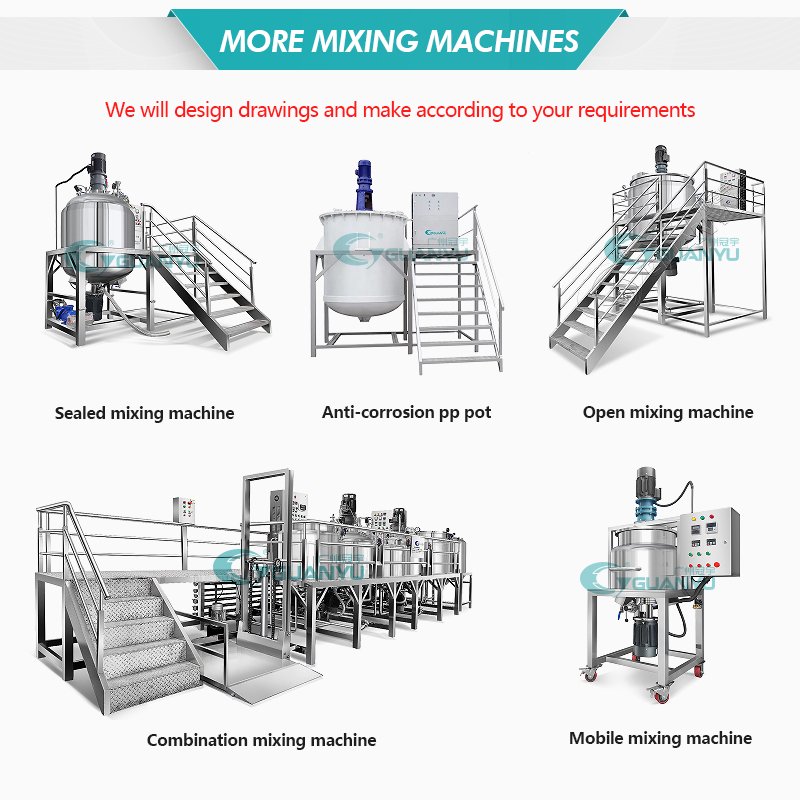
Summary
In evaluating whether to choose electric heating or steam heating for your mixing machine, several critical factors must be considered to make an informed decision that aligns with your specific needs and operational circumstances. Both heating methods present unique advantages and potential drawbacks that can significantly impact efficiency, custo, and overall performance within your production environment.
Electric heating is generally praised for its precision and ease of use. It offers consistent and easily controllable temperature settings, making it ideal for processes requiring exact temperature maintenance. Adicionalmente, electric heating systems tend to be more compact and easier to install, which can be advantageous in facilities with limited space. No entanto, it’s essential to consider the potentially higher operational costs due to electricity prices, which can vary significantly by region.
Por outro lado, steam heating is often preferred for its efficiency in transferring heat over large areas. It is particularly effective in environments where rapid and uniform heating is necessary. Steam systems can capitalize on existing infrastructure, potentially reducing initial setup costs. No entanto, they require a more complex setup, including boilers and extensive piping, which can increase maintenance needs and initial investment costs. Além disso, safety considerations are paramount with steam systems due to the high pressures and temperatures involved.
Aspect | Electric Heating | Steam Heating |
---|---|---|
Temperature Control | Highly precise | Moderate precision |
Installation | Simple, space-efficient | Complex, space-intensive |
Operational Cost | Depends on electricity rates | Potentially lower, depends on fuel source |
Maintenance | Lower complexity | Higher complexity |
Safety | Generally safer | Requires stringent safety measures |
Ultimately, the decision between electric and steam heating for your mixing machine hinges on a careful consideration of these factors. Understanding the specific requirements of your processes, the existing infrastructure, and budgetary constraints will guide you towards the most suitable and efficient heating solution for your operations.
Warmly welcome to contact us, our company official website:https://gzguanyu.en.alibaba.com/productgrouplist-210357808/Vacuum_Emulsifying_Machine.html