Understanding the Basics of Shower Gel Production
Shower gel production begins with a comprehensive understanding of the essential raw materials, each playing a crucial role in the final product’s quality and functionality. Key ingredients include surfactants, espessantes, fragrâncias, and colorants. Surfactants are the primary cleaning agents responsible for removing dirt and oil from the skin. They create the foam that users associate with cleanliness and freshness. Common surfactants used in shower gel production are sodium lauryl sulfate (SLS) and sodium laureth sulfate (SLES), known for their effective cleansing properties.
Thickeners, such as hydroxyethylcellulose and xanthan gum, are added to achieve the desired viscosity, ensuring the shower gel is neither too runny nor too thick. These ingredients enhance the textural experience and ensure the product spreads evenly on the skin. Fragrances are incorporated to provide a pleasant scent, enhancing the user’s sensory experience. These can range from natural essential oils to synthetic aromatic compounds, depending on the target market and formulation goals. Colorants, whether natural or synthetic, give the shower gel its appealing visual appearance, which can significantly influence consumer preference.
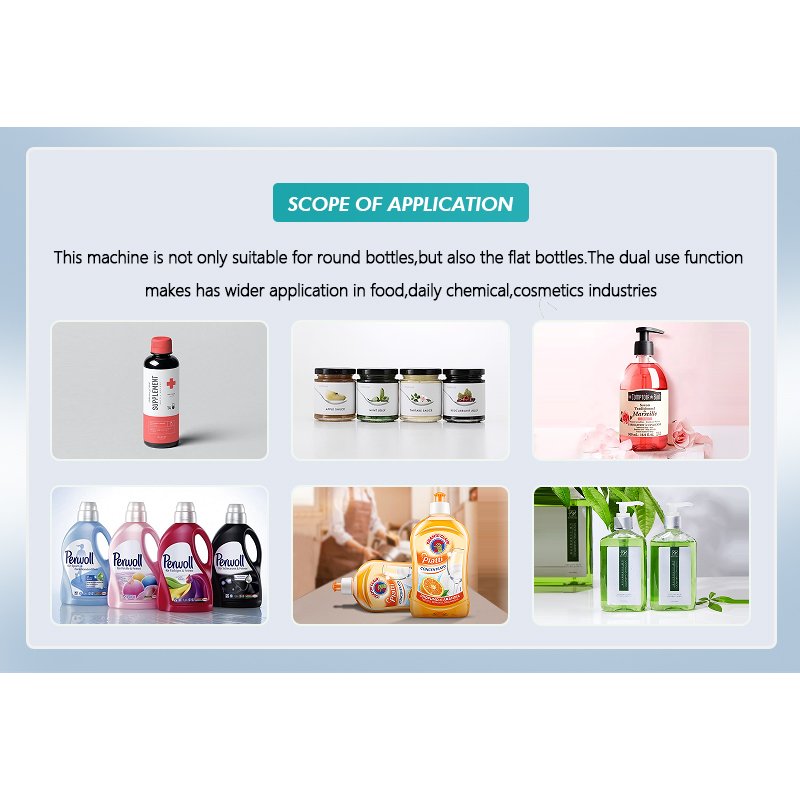
Achieving a homogenous mixture is paramount in shower gel production. Uniformity ensures that each use delivers consistent performance and sensory experience. This homogeneity is achieved through careful mixing and blending processes, where all ingredients are combined thoroughly to avoid separation or inconsistencies. Mixing tanks and blenders are indispensable in the initial stages of production. Mixing tanks, often equipped with agitators, facilitate the thorough blending of large batches of ingredients. Blenders, por outro lado, are used for smaller batches or for achieving finer consistency.
Understanding these basics is crucial for anyone looking to produce high-quality shower gel. Each ingredient and piece of equipment plays a vital role in creating a product that meets consumer expectations for performance, textura, and aesthetic appeal. By mastering these fundamentals, producers can ensure a reliable and successful shower gel formulation.
Choosing Between an Emulsifier and a Mixing Pot
When it comes to producing shower gel, selecting the right mixer is crucial for ensuring the final product’s quality and consistency. Two primary options are available: emulsifiers and mixing pots. Each has its unique set of functionalities, advantages, and disadvantages, making them suitable for different production needs.
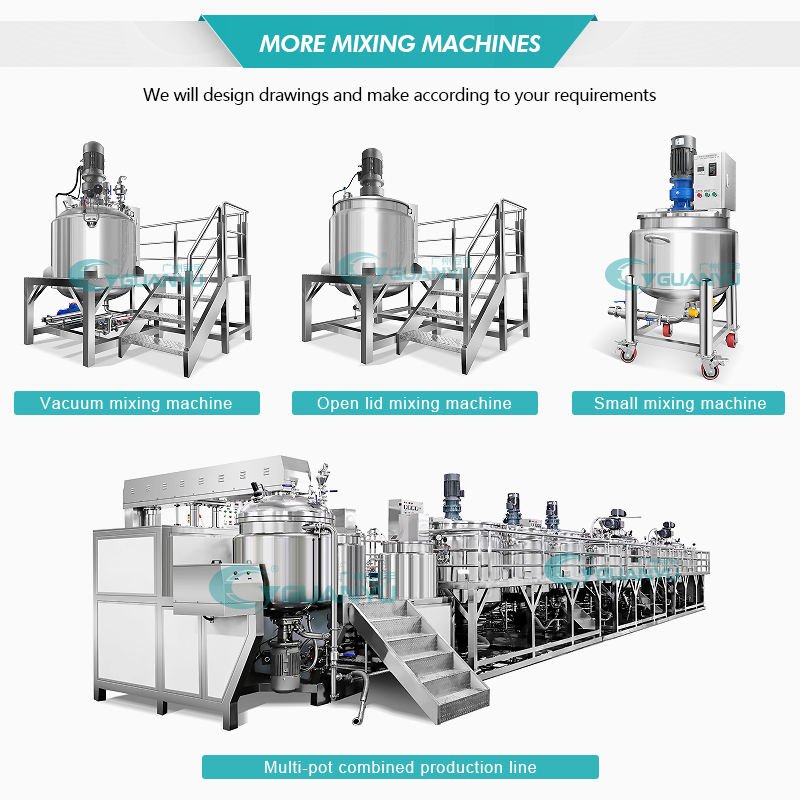
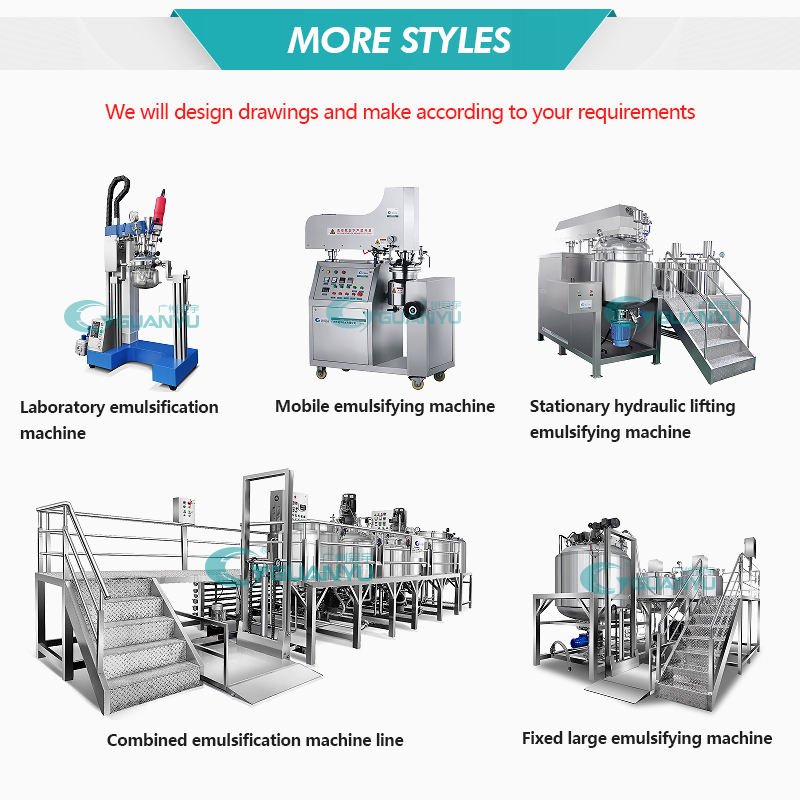
Emulsifiers are specialized mixers designed to blend immiscible liquids, such as oil and water, which are common components in shower gel formulations. By applying high shear forces, emulsifiers create a stable emulsion, ensuring that the oil and water phases are uniformly mixed. This results in a smooth and homogenous shower gel, enhancing its texture and performance. Emulsifiers are particularly beneficial for formulations that require a fine and consistent dispersion of ingredients, providing superior product stability and shelf-life.
Por outro lado, mixing pots, also known as batch mixers, offer a more straightforward approach to blending ingredients. These mixers typically involve a large vessel where ingredients are combined and agitated until they reach the desired consistency. While mixing pots might not achieve the same level of uniformity as emulsifiers, they are often sufficient for simpler formulations and smaller-scale productions. Their ease of use and lower cost make them an attractive option for businesses with limited resources or less complex shower gel recipes.
Efficiency is a critical factor when choosing between an emulsifier and a mixing pot. Emulsifiers generally provide faster mixing times and better energy efficiency due to their advanced technology. No entanto, they also come with higher initial costs and require more technical expertise to operate. Em contraste, mixing pots are more cost-effective and easier to manage but may require longer mixing times and result in less consistent emulsions.
Scalability is another consideration. Emulsifiers are well-suited for large-scale production, offering consistent results across multiple batches. Mixing pots, while scalable to a certain extent, may face limitations in maintaining product uniformity as production volumes increase. Portanto, when planning for expansion, an emulsifier might be the more practical long-term investment.
In terms of technical requirements, it is essential to consider the specific needs of your shower gel formulation. Look for emulsifiers with adjustable shear rates and temperature controls to fine-tune the mixing process. For mixing pots, ensure that the vessel size, mixing speed, and agitation method align with your production goals.
Additional Features: Heating and Vacuum Functions
When choosing a mixer for shower gel production, it is crucial to consider whether additional features such as heating and vacuum functions are necessary. These features can significantly impact the quality and efficiency of your production process, depending on your specific formulation and production scale.
Heating functions are essential in the production of shower gel for several reasons. Firstly, heating aids in the dissolution of various ingredients, ensuring that all components blend seamlessly. Por exemplo, certain surfactants and thickeners require a specific temperature to dissolve completely, preventing grainy textures and ensuring a smooth, uniform consistency. Adicionalmente, heating can accelerate the mixing process, reducing overall production time and improving batch consistency.
The vacuum function, por outro lado, plays a critical role in enhancing the texture and stability of the shower gel. By removing air bubbles that may have formed during mixing, a vacuum function ensures a smooth, homogeneous product. Air bubbles can not only affect the aesthetic quality of the shower gel but can also compromise its stability and shelf life. A vacuum function can thus help in producing a more stable and visually appealing product.
Determining the necessity of these features depends on your specific needs. For small-scale production or simple formulations, a basic mixer without heating and vacuum functions may suffice. No entanto, for larger-scale production or more complex formulations that include sensitive ingredients, investing in a mixer with these advanced functionalities can be beneficial. The improved dissolution, enhanced texture, and increased stability provided by heating and vacuum functions can lead to a higher-quality end product with a longer shelf life.
Resumindo, while heating and vacuum functions may represent an additional investment, their benefits in terms of product quality and production efficiency often justify the cost. Evaluating your production requirements and formulation complexity will guide you in making the right choice for your mixer needs.