Fabric softeners have become an essential household product, transforming laundry from a mundane chore into a more pleasant experience. These products not only soften fabrics but also reduce static cling, make ironing easier, and impart a fresh scent to clothes. The production process of fabric softeners is intricate and requires precise equipment to ensure the final product’s quality and consistency. One of the most critical pieces of equipment in this process is the blending vessel. This article will explore the production process of fabric softeners, how to select the appropriate blending vessel, and the advantages and applications of blending vessels in the manufacturing of household and personal care products.
Introduction to Fabric Softener Production
The production of fabric softeners involves several stages, starting from the formulation of raw materials to the final packaging of the product. The primary ingredients typically include cationic surfactants, which are responsible for the softening effect, along with other components such as fragrances, corantes, conservantes, and thickeners.
Key Steps in Fabric Softener Production
- Formulation and Mixing: The first step is formulating the blend of ingredients. This is done in a blending vessel where raw materials are measured and added according to a specific recipe.
- Heating and Agitation: To ensure that all ingredients are thoroughly mixed and any solid components are dissolved, the mixture is often heated and continuously stirred. This step is crucial for achieving a homogeneous mixture.
- Homogenization: Depending on the formulation, the mixture might need to be homogenized to achieve a stable emulsion. This step is particularly important for ensuring that the active ingredients are evenly distributed throughout the product.
- Cooling and Dilution: After homogenization, the mixture is cooled to a desired temperature and diluted to the final concentration. This step can also involve adjusting the pH and adding any heat-sensitive ingredients.
- Filtration and Packaging: The final product is filtered to remove any impurities or undissolved particles and then packaged in bottles or other containers.
Selecting the Appropriate Blending Vessel
The blending vessel, also known as a mixing tank or mixer, plays a pivotal role in the production process. Choosing the right blending vessel is crucial for ensuring the efficiency and quality of the fabric softener.
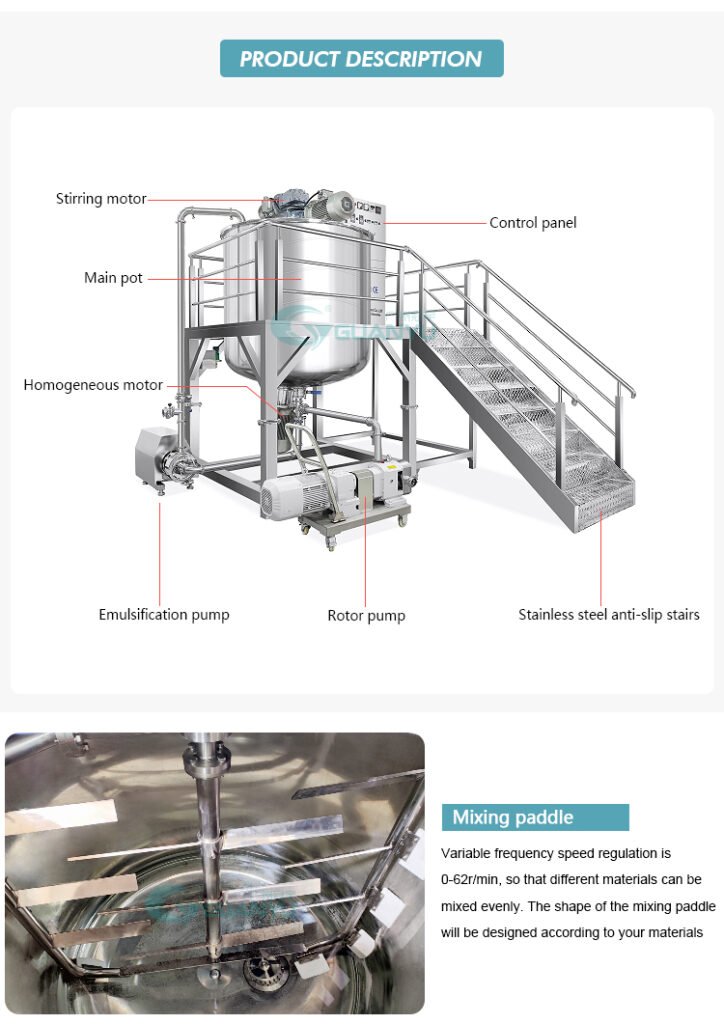

Factors to Consider When Choosing a Blending Vessel
- Capacidade: The capacity of the blending vessel should match the production scale. Small-scale production might require vessels of a few hundred liters, while large-scale operations might need vessels with capacities of several thousand liters.
- Material Construction: Blending vessels are typically made from stainless steel due to its corrosion resistance, durability, and ease of cleaning. Stainless steel is particularly important in maintaining the purity of the product and preventing contamination.
- Heating and Cooling Capabilities: Some formulations require precise temperature control. Vessels equipped with heating jackets or coils can ensure that the mixture reaches the necessary temperature for optimal blending. Similarly, cooling jackets can help quickly bring the mixture to the desired temperature after heating.
- Agitation and Mixing Mechanism: The design of the agitator is crucial for effective mixing. Options include paddle mixers, turbine mixers, and anchor agitators, each suited for different types of products. The mixing mechanism should provide sufficient shear to blend the ingredients thoroughly without causing excessive aeration.
- Vacuum Capability: Vessels with vacuum capabilities are beneficial for removing air and preventing oxidation during the mixing process. This is particularly important for products sensitive to air or requiring a smooth, air-free consistency.
- Sanitization and Cleanability: The vessel should be easy to clean and sanitize to prevent contamination between batches. Features such as CIP (Clean-in-Place) systems can automate and streamline the cleaning process.
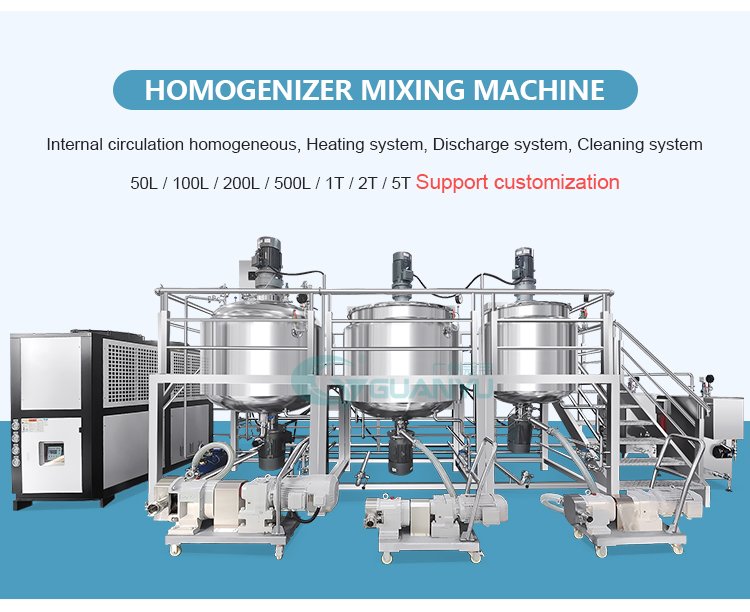
Advantages of Using Blending Vessels
Blending vessels offer numerous advantages in the production of fabric softeners and other personal care products.
Homogeneous Mixing
Blending vessels are designed to provide thorough and consistent mixing of ingredients, ensuring a homogeneous product. This uniformity is critical for the performance of the fabric softener, as any uneven distribution of active ingredients can lead to inconsistent results.
Efficient Heating and Cooling
The integrated heating and cooling systems in blending vessels allow for precise temperature control. This capability is essential for the solubility of certain ingredients and the stability of the final product. Efficient temperature management can also reduce production time and energy consumption.
Vacuum Processing
The option to use vacuum processing in blending vessels offers several benefits. It helps remove entrapped air, reducing the risk of oxidation and improving the shelf life of the product. Vacuum processing also aids in achieving a smooth, lump-free consistency, which is important for the aesthetic and functional qualities of the fabric softener.
Scalability
Blending vessels come in a range of sizes, making it easy to scale up production as demand increases. This scalability is advantageous for manufacturers looking to expand their operations without significant changes to their production infrastructure.
Automation and Control
Modern blending vessels are often equipped with advanced control systems that allow for precise monitoring and adjustment of various parameters such as temperature, mixing speed, and vacuum level. Automation improves process consistency, reduces the likelihood of human error, and enhances overall production efficiency.
Applications of Blending Vessels in Household and Personal Care Product Manufacturing
Blending vessels are not limited to the production of fabric softeners. They are widely used in the manufacturing of various household and personal care products due to their versatility and effectiveness.
Detergents and Cleaners
In addition to fabric softeners, blending vessels are integral to the production of liquid detergents and household cleaners. These products require thorough mixing of surfactants, solventes, and other additives to achieve the desired cleaning performance and stability.
Cosmetics and Toiletries
The cosmetic industry relies heavily on blending vessels for the production of creams, loções, shampoos, and conditioners. These products often involve complex formulations that require precise mixing and temperature control to ensure the stability and efficacy of the active ingredients.
Farmacêuticos
Na indústria farmacêutica, blending vessels are used to mix various ingredients for the production of liquid medicines, xaropes, and topical treatments. The ability to maintain strict hygiene standards and prevent contamination is particularly important in this field.
Food and Beverages
Blending vessels are also employed in the food and beverage industry for mixing ingredients in the production of sauces, dressings, e bebidas. The versatility and efficiency of these vessels make them suitable for a wide range of applications.

Conclusão
The blending vessel is an indispensable component in the production process of fabric softeners and a variety of other household and personal care products. Its role in ensuring the homogeneous mixing of ingredients, efficient temperature control, and the ability to operate under vacuum conditions makes it a critical asset in modern manufacturing. By carefully selecting the appropriate blending vessel based on capacity, material construction, heating and cooling capabilities, agitation mechanism, vacuum functionality, and cleanability, manufacturers can significantly enhance their production efficiency and product quality.
Para concluir, the integration of advanced blending vessels in the production process not only optimizes the manufacturing workflow but also ensures that the final product meets the highest standards of quality and performance. As the demand for high-quality household and personal care products continues to grow, the importance of reliable and efficient blending vessels will remain paramount in the industry.