Different Configurations of Mixing Pots and Their Effects
In the production of liquid soap, the configuration of the mixing pot plays a pivotal role in determining the quality and characteristics of the final product. Various configurations of mixing pots can significantly influence the efficiency of the mixing process, impacting factors such as viscosity, texture, and stability of the liquid soap.
Mixing pots come in a variety of capacities, ranging from small-scale units for artisanal soap makers to large industrial vats for mass production. The capacity of the pot affects the homogeneity of the mixture; smaller pots often allow for more precise control over ingredients, leading to a more consistent product. Conversely, larger pots are equipped to handle higher volumes but may require advanced mixing mechanisms to ensure uniformity.
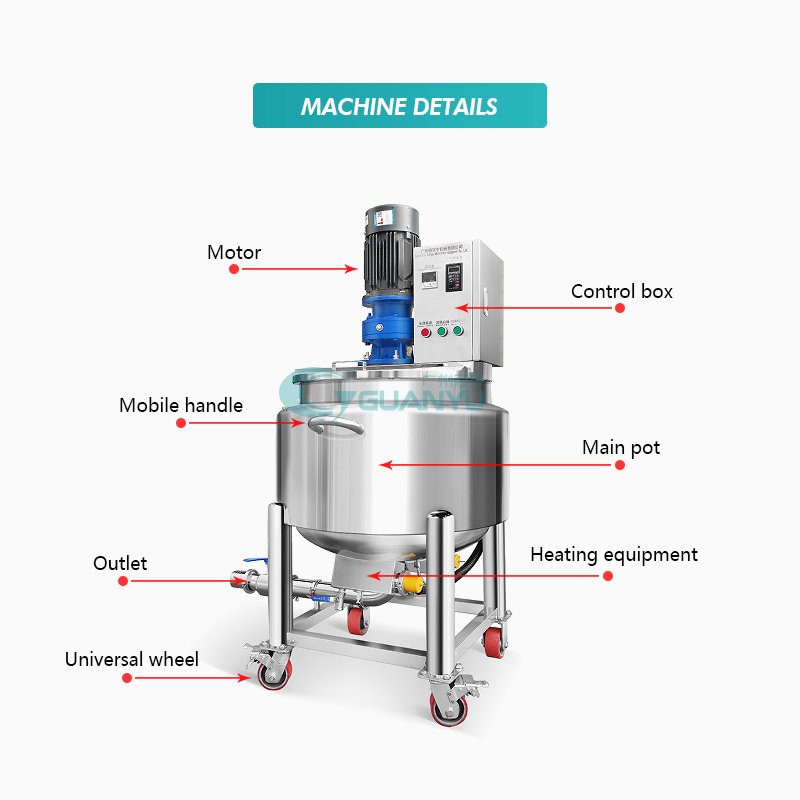
Material composition of mixing pots is another critical factor. Stainless steel is a popular choice due to its durability, resistance to corrosion, and ease of cleaning. Glass and plastic pots are also used, particularly in smaller-scale operations. The choice of material can influence the thermal conductivity and chemical reactivity during the soap-making process, thereby affecting the stability and quality of the final product.
Selecting the appropriate mixing pot configuration is essential based on the desired characteristics of the liquid soap. For instance, a high-viscosity soap may require a pot with robust mixing capabilities and a heating element to ensure smooth blending. Similarly, ensuring the right pot shape and material can help achieve the optimal texture and stability, preventing issues such as separation or inconsistent viscosity.
Ultimately, understanding the various configurations of mixing pots and their specific effects is crucial for any soap maker aiming to produce high-quality liquid soap. By carefully selecting the right mixing pot, manufacturers can enhance product quality, consistency, and overall production efficiency.
Stirring Pot: Cold Mixing Process and Hot Mixing Process
The production of liquid soap hinges significantly on the method employed in the mixing process. Two primary methods dominate the field: cold mixing and hot mixing. Each approach has its distinct advantages, tailored to suit different types of liquid soap products.
The cold mixing process involves combining ingredients at room temperature. This method is particularly advantageous for its energy-saving benefits, as it eliminates the need for heating elements, thus reducing operational costs. Furthermore, cold mixing is ideal for preserving the integrity of heat-sensitive ingredients. Essential oils, fragrances, and certain active components that may degrade at elevated temperatures remain intact, maintaining their efficacy and aroma. Liquid soap products such as delicate facial cleansers, natural and organic soaps, and those containing essential oils are best suited for cold mixing. This method ensures that the final product retains its intended therapeutic and aromatic properties.
Conversely, the hot mixing process requires heating the ingredients to specific temperatures to achieve optimal solubility and homogeneity. This method facilitates better integration of certain ingredients that are otherwise challenging to dissolve or emulsify at room temperature. Heating the soap mixture ensures that all components meld seamlessly, resulting in a consistent and stable final product. The hot mixing process is particularly beneficial for creating liquid soaps with ingredients that require thorough incorporation, such as thickening agents, certain surfactants, and preservatives. Products like antibacterial soaps, heavy-duty cleaners, and moisturizing body washes often necessitate this method to ensure their performance and longevity.
Ultimately, the choice between cold and hot mixing processes depends on the nature of the ingredients and the desired characteristics of the final soap product. Both methods play a crucial role in the liquid soap production industry, each offering unique benefits that cater to specific formulation needs.
Homogenized vs. Non-Homogenized Mixing Pots
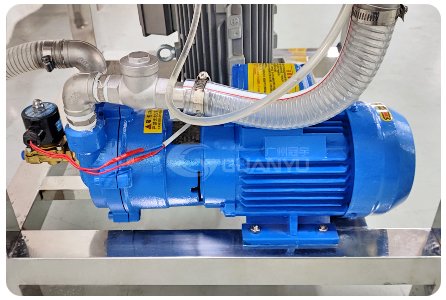
Homogenization is a critical process in liquid soap production, aimed at achieving a uniform distribution of ingredients. This method involves breaking down particles to a consistent size and evenly dispersing them throughout the mixture. Homogenization ensures that all components are thoroughly blended, leading to a stable, high-quality product. The primary function of a homogenized mixing pot is to facilitate this process, using mechanical means such as high-speed mixers or homogenizers.
The technical aspects of a homogenized mixing pot include high shear forces and intense agitation. These elements are essential for breaking down particles and emulsifying oils and water-based components, which are often present in liquid soap formulations. The benefits of using a homogenized mixing pot are manifold. Firstly, it ensures the consistency of the product, eliminating the risk of separation over time. Secondly, it enhances the efficacy of the soap by ensuring that active ingredients are evenly distributed. Lastly, it improves the aesthetic qualities, such as clarity and texture, making the final product more appealing to consumers.
When deciding whether to use a homogenized or non-homogenized mixing pot, the specific requirements of the liquid soap product must be considered. Products with complex formulations, including multiple oils, emulsifiers, and active agents, typically benefit from homogenization. Such products require a uniform texture and stability, which can only be achieved through the homogenization process. On the other hand, simpler formulations with fewer ingredients might not necessitate the use of a homogenized mixing pot. These products can be effectively mixed using standard agitation methods, provided that the ingredients are compatible and do not require intensive blending to achieve stability.
In summary, the choice between homogenized and non-homogenized mixing pots depends on the complexity of the liquid soap formulation and the desired characteristics of the final product. Homogenization plays a vital role in ensuring product consistency, stability, and quality, particularly for formulations involving multiple, diverse components.
Stirring Pot Control Systems
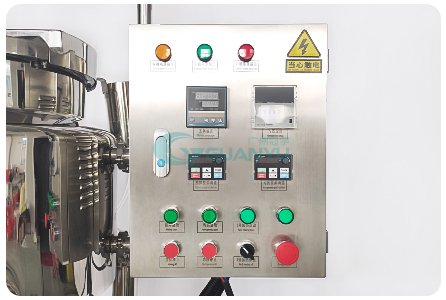
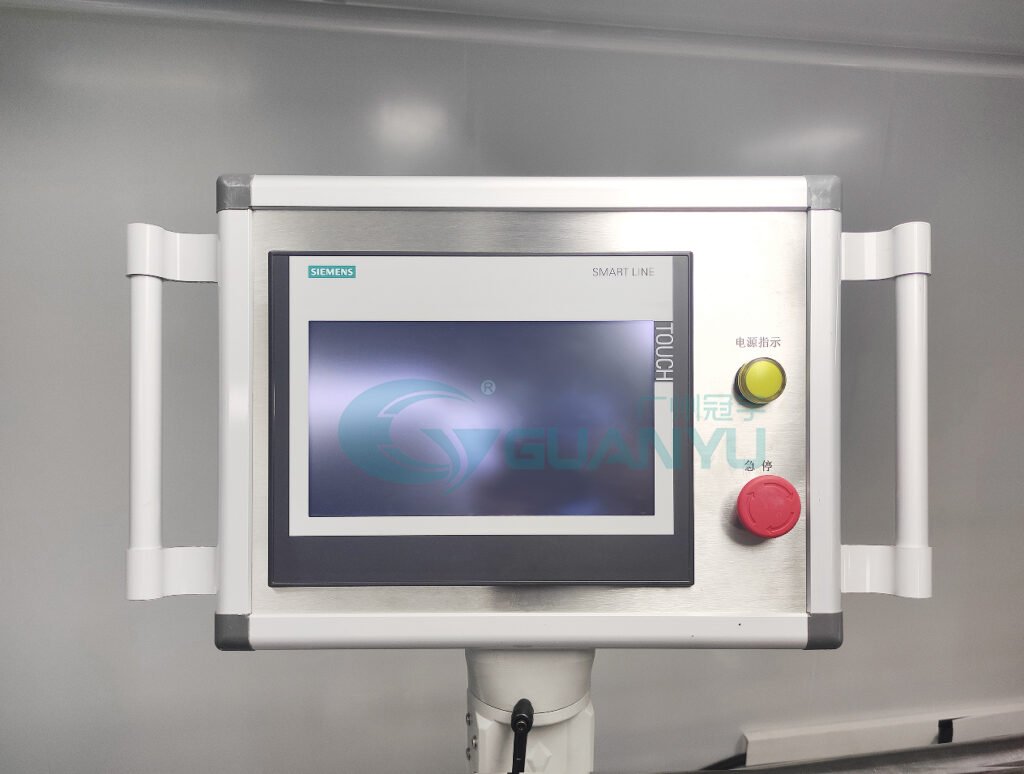
In the realm of liquid soap production, the efficiency and precision of stirring pot control systems play a pivotal role in ensuring the quality and consistency of the final product. These systems can be broadly categorized into traditional button control systems and advanced programmable logic controller (PLC) systems, each with its unique advantages and drawbacks.
The button control system is a conventional manual control mechanism widely employed in small-scale liquid soap production. This system relies on physical buttons to manage the stirring process, offering a straightforward and user-friendly interface. Operators can easily start, stop, and adjust the stirring speed to suit their specific needs. One of the key benefits of the button control system is its simplicity, making it an ideal choice for smaller operations with limited technical expertise. Additionally, these systems are generally cost-effective and require minimal maintenance, further enhancing their appeal to small businesses and artisanal producers.
On the other hand, the intelligent PLC system represents a significant advancement in stirring pot control technology. Designed for large-scale production environments, PLC systems offer unparalleled automation, precision control, and programmability. These systems utilize sophisticated software to monitor and adjust various parameters of the stirring process, ensuring optimal conditions are maintained consistently. The high degree of automation reduces the need for manual intervention, thereby minimizing human error and increasing overall efficiency. Furthermore, the programmability of PLC systems allows for the implementation of complex stirring protocols, enabling producers to achieve precise results tailored to specific formulations and batch sizes.
While the button control system is favored for its ease of use and cost-effectiveness, it may fall short in terms of scalability and precision in larger operations. Conversely, the PLC system excels in enhancing efficiency and consistency, though it comes with higher initial costs and requires a certain level of technical expertise for setup and maintenance. Ultimately, the choice between these control systems depends on the scale of production, available resources, and specific requirements of the liquid soap manufacturing process.
Summary
Understanding the pivotal role of mixing pots in liquid soap production is essential for achieving consistent quality and efficiency. Selecting the appropriate mixing pot configurations is crucial, as it directly impacts the final product’s texture, viscosity, and overall stability. Different mixing processes, such as high-shear mixing and low-shear mixing, cater to various stages of production, enabling manufacturers to customize their approach based on specific formulation requirements.
The significance of homogenization cannot be overstated; it ensures that all ingredients are uniformly distributed, preventing separation and achieving a seamless blend. Advanced control systems further enhance the production process by allowing precise adjustments to temperature, speed, and mixing time, thereby optimizing performance and minimizing waste.
By integrating these elements—proper mixing pot configurations, understanding mixing processes, emphasizing homogenization, and leveraging advanced control systems—manufacturers can not only improve the quality of their liquid soap but also enhance production efficiency, leading to better scalability and cost-effectiveness. This comprehensive approach is fundamental to mastering the complexities of liquid soap production and maintaining a competitive edge in the market.
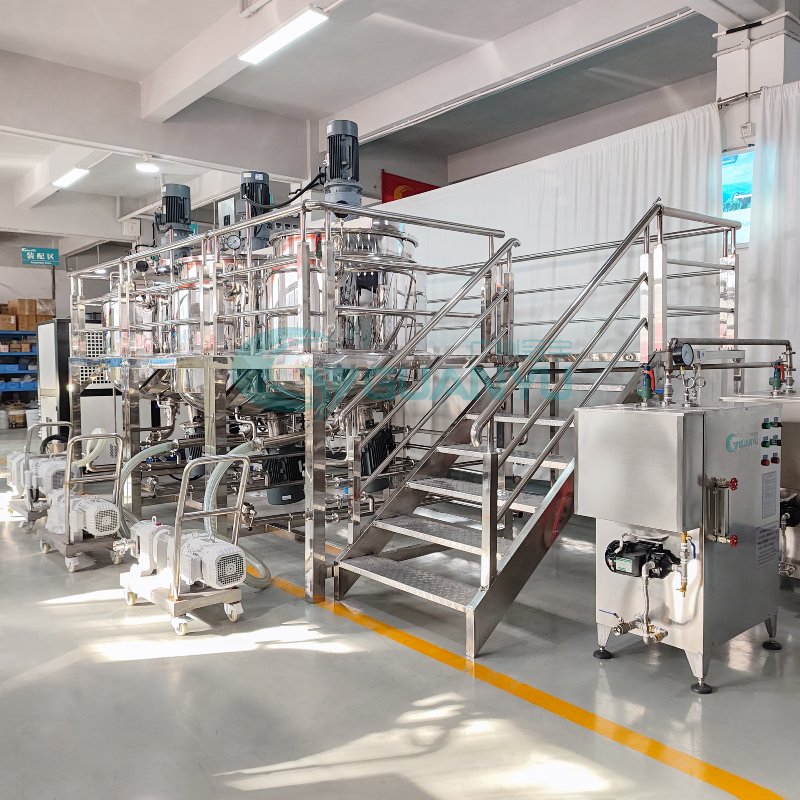