Exploring the Liquid Soap Manufacturing Process: Machine Solutions and Efficiency
The manufacturing of liquid soap has garnered significant attention in today’s market due to its versatile applications and the rising preference among consumers. Unlike traditional bar soap, liquid soap offers several benefits, making it a popular choice for households, industries, and commercial settings alike. The ease of use, combined with the convenience of dispensing, has contributed to the growing demand for liquid soap products. En fait, the liquid soap market has expanded significantly to cater to diverse consumer needs ranging from personal hygiene to industrial cleaning solutions.
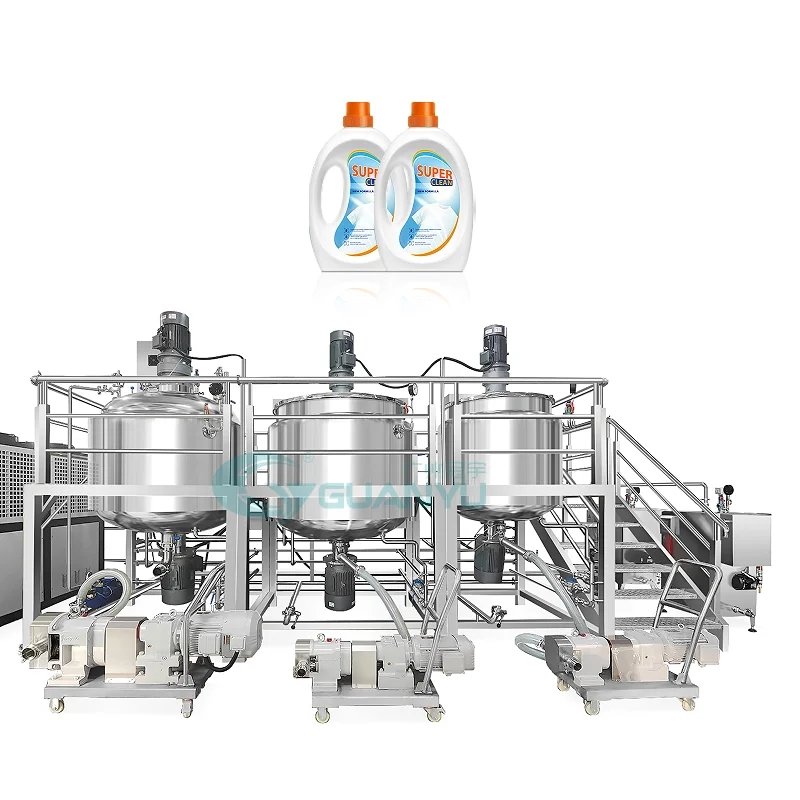
En plus, liquid soap is often perceived as more hygienic compared to bar soap, as it minimizes direct contact with surfaces that may harbor bacteria. This aspect has driven its popularity, particularly in environments where sanitation is paramount, such as hospitals, restaurants, and schools. Furthermore, the formulation of liquid soap allows for a wide range of customization. Manufacturers can incorporate various scents, colors, and skin-nourishing ingredients, appealing to a broader audience by addressing specific consumer preferences and skin types.
The evolution of the liquid soap industry is marked by the integration of advanced technology in the manufacturing process. Automated machinery and efficient production techniques have significantly enhanced output while maintaining quality. As consumers increasingly prioritize both efficacy and environmental sustainability, manufacturers are adapting by offering eco-friendly formulations and packaging. The expansion of distribution channels, including online platforms, has also played a crucial role in fostering the growth of liquid soap products.
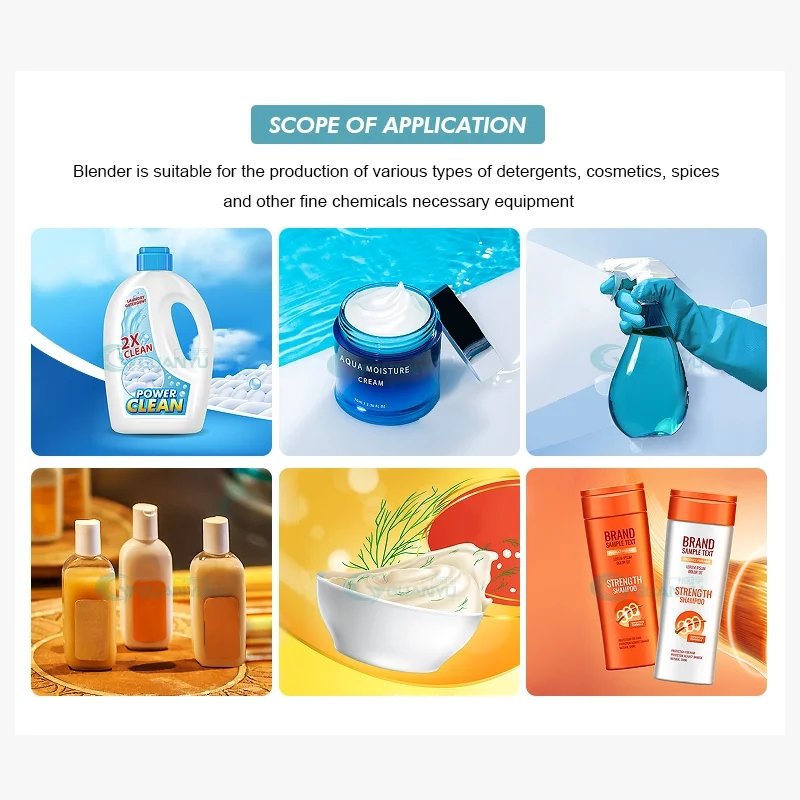
As society progresses towards greater hygiene awareness and environmental consciousness, the liquid soap manufacturing process will continue to evolve. This evolution not only meets consumer demands but also aligns with global trends towards health and sustainability. The future of liquid soap production holds promise as innovation and efficiency remain at the forefront of the industry.
Understanding Liquid Soap Making Machines
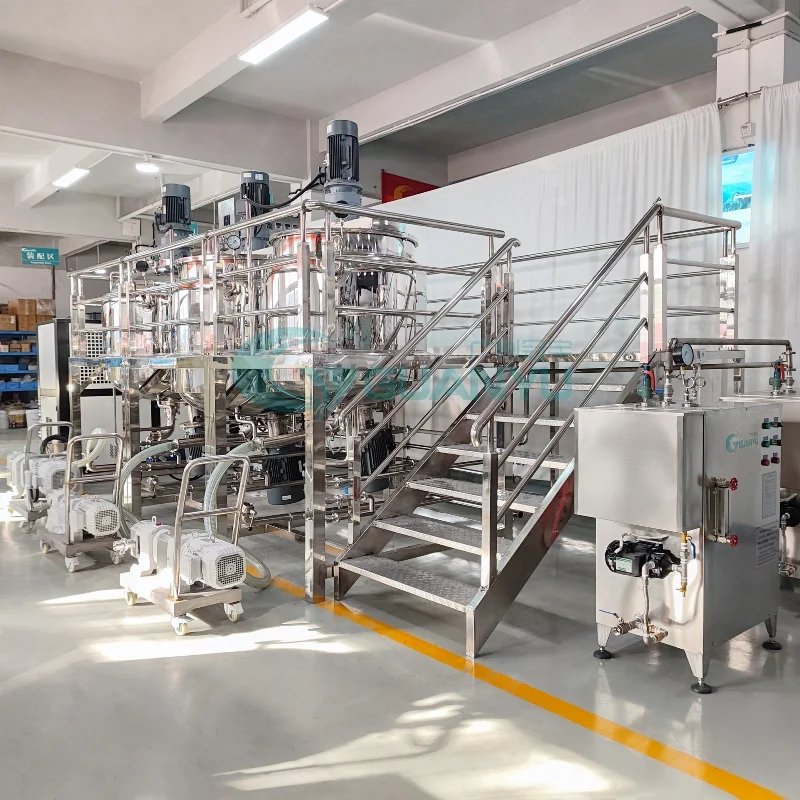
The manufacturing process of liquid soap is heavily reliant on advanced machinery designed to streamline production and maximize efficiency. Among the various types of equipment available, cream liquid soap and shampoo mixers stand out due to their specialized functions and capabilities. These machines are essential for achieving consistent quality and desired viscosity in the final product.
Cream liquid soap mixers typically incorporate high-shear mixing technology, which ensures that all ingredients, y compris les tensioactifs, épaississants, and fragrances, are thoroughly combined. This robust mechanism allows for uniform blending, preventing separation and ensuring a creamy texture that meets customer expectations. The operation of these mixers is straightforward, often featuring automated controls that regulate mixing speed and duration, thus allowing for precise adjustments throughout the production process.
When selecting liquid soap making machines, it is crucial to consider their features and production capacity. Factors such as material construction, ease of cleaning, and integration with automated systems can significantly impact operational efficiency. High-capacity machines, capable of producing up to 500 kg of liquid soap per hour, offer considerable advantages to manufacturers looking to scale production. Investing in such equipment not only increases output but also reduces labor costs by minimizing manual intervention.
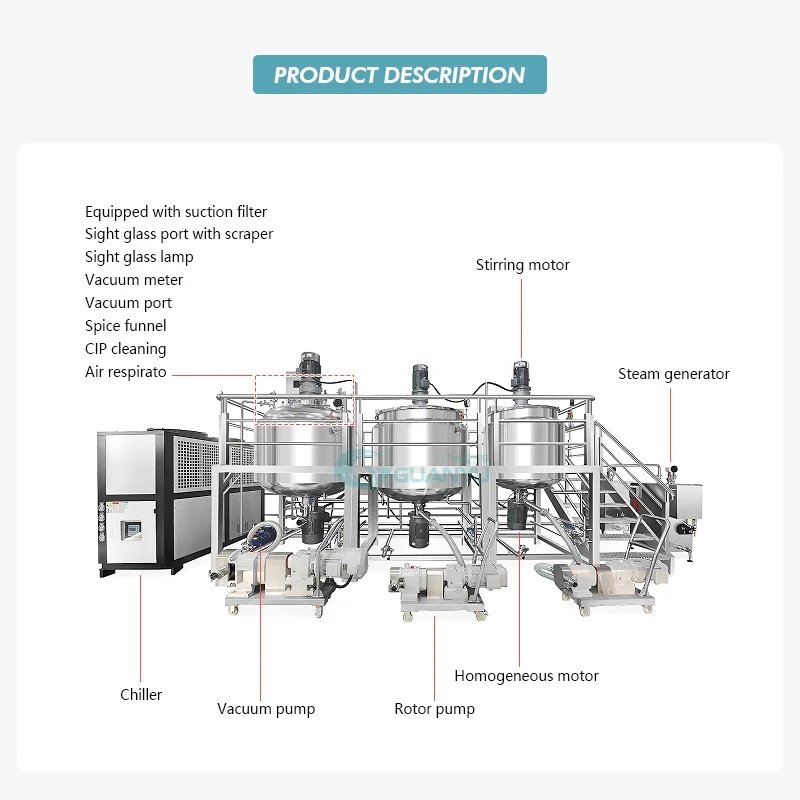
Moreover, advanced models often come equipped with additional functionalities such as temperature control and inbuilt pumps, which facilitate the smooth transfer of mixtures to packaging. These features enhance the overall manufacturing workflow, making it essential for producers to evaluate their specific needs before making a purchase decision. In the competitive landscape of liquid soap manufacturing, choosing the right machine can profoundly influence product quality and operational success.
Key Components of a Liquid Soap Manufacturing Plant
Establishing a liquid soap manufacturing plant requires careful consideration of several key components essential for optimal functionality and efficiency. The layout and design of the manufacturing facility play a critical role in determining the workflow and overall productivity. A well-planned layout minimizes bottlenecks, facilitates smooth movement of materials, and ensures a safe working environment for employees.
Equipment selection is another vital factor when setting up a liquid soap manufacturing plant. The choice of machinery directly influences the quality of the final product as well as the efficiency of the production process. Common equipment includes mixers, emulsifiers, heating systems, and filling machines, which must be chosen based on their capability to handle different formulations and production volumes. En plus, the integration of automation technology cannot be overlooked. Automation enhances prescriptive control, reducing human error and increasing throughput.
Supply chain management is crucial in the context of liquid soap manufacturing. Secure sourcing of raw materials—such as surfactants, parfums, and preservatives—ensures consistent quality and availability, thereby streamlining production processes. An effective inventory management system is necessary to keep track of stock levels and forecast material requirements efficiently.
Quality control is a fundamental component of any liquid soap manufacturing operation. Regular testing of both raw materials and finished products is essential to ensure compliance with established industry standards. Quality control not only guarantees the efficacy and safety of the produced liquid soap but also reinforces brand credibility. Implementing a comprehensive quality assurance program typically involves routine inspections and adherence to regulatory frameworks, paving the way for sustained operational success.
In summary, the foundation of a successful liquid soap manufacturing plant hinges on strategic layout, equipment choice, an efficient supply chain, and rigorous quality control measures. With the right machinery and practices, manufacturers can achieve remarkable efficiency and product quality in their processes.
Cost-Effectiveness and Sustainability in Liquid Soap Production
The liquid soap manufacturing process plays a crucial role in determining both the cost-effectiveness and sustainability of the product. One of the primary expenses in this industry stems from the acquisition of advanced manufacturing machines. Initial investment costs can be significant, as these machines vary in capacity and technology. Cependant, choosing the right technology can lead to substantial savings in operational costs over time. Automated and efficient machinery can minimize human intervention, reduce production time, and lower labor costs, making it feasible for manufacturers to scale their operations while preserving quality.
Operational expenses also include raw materials, utilities, and maintenance. In recent years, there has been a growing emphasis on sourcing eco-friendly ingredients. By utilizing natural and biodegradable components in liquid soap production, manufacturers not only enhance the product’s marketability but also contribute to environmental conservation. Sustainable practices, such as using renewable resources and minimizing waste, can significantly lower production costs in the long run. Many companies find that adopting these practices not only improves their brand reputation but also aligns with the values of an increasingly eco-conscious consumer base.
Energy optimization is another vital area for enhancing sustainability. Transitioning to energy-efficient machinery and adopting best practices for energy use can reduce utility bills and carbon footprints. Investments in green technologies, such as solar energy or closed-loop manufacturing systems, ultimately contribute to cost savings and sustainability. By focusing on innovative solutions and sustainable manufacturing practices, liquid soap producers can create a balance between profitability and environmental responsibility. This ultimately aids in building a competitive advantage in the market while addressing the growing demand for sustainable products in the personal care industry.