In the world of fragrance production, precision, efficiency, and quality are paramount. The process of filling perfume bottles is a critical stage in the production line, where the essence of the brand is captured and presented to the consumer. This is where perfume filling machines come into play. These advanced machines have revolutionized the perfume industry by offering a high degree of automation, accuracy, and consistency. En este artículo, we’ll delve into the intricacies of perfume filling machines, exploring their components, functionality, benefits, and the significant role they play in the fragrance industry.
Understanding Perfume Filling Machines
Perfume filling machines are specialized equipment designed to automate the process of dispensing precise amounts of liquid perfume into bottles. These machines come in various types, tailored to different production needs, from small-scale artisanal operations to large-scale industrial manufacturing. The primary objective of these machines is to ensure that each bottle is filled with the exact volume of perfume, minimizing wastage and maintaining product consistency.
Key Components of Perfume Filling Machines
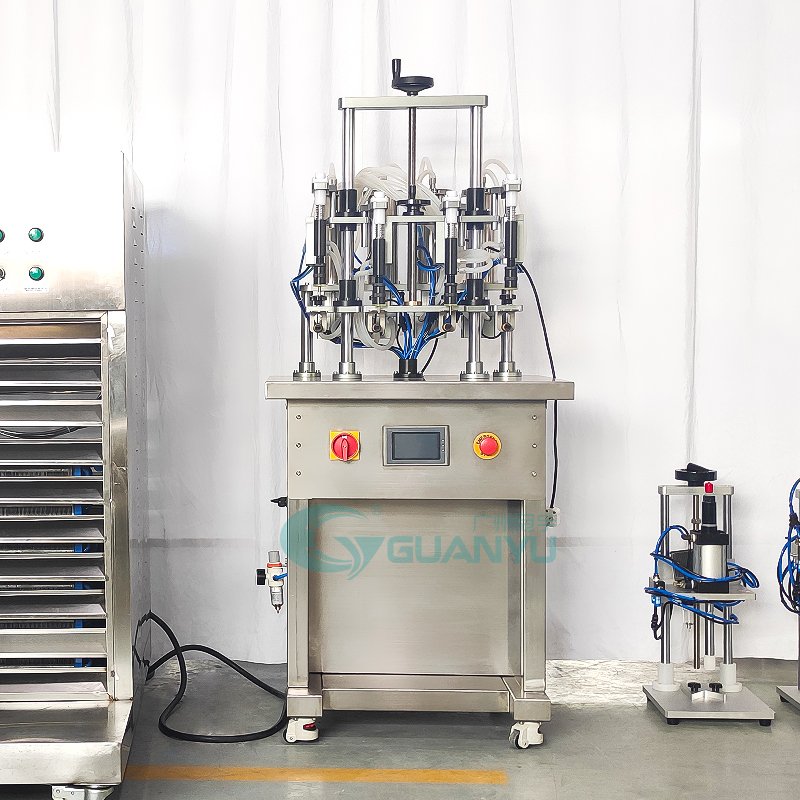
A perfume filling machine is a sophisticated piece of equipment, typically composed of the following key components:
- Filling System: The heart of the machine, this system is responsible for dispensing the perfume into the bottles. It often includes multiple filling heads to handle several bottles simultaneously, significantly boosting production speed.
- Conveyor System: This system moves empty bottles to the filling station and then transports filled bottles to the next stage of the production line. Conveyors can be adjusted to match the speed of production, ensuring a smooth and continuous operation.
- Bottle Positioning Unit: To ensure accuracy, bottles must be precisely positioned under the filling heads. This unit ensures each bottle is correctly aligned before filling begins, preventing spillage and ensuring consistency.
- PLC Control System: Programmable Logic Controllers (PLCs) are used to manage the entire filling process. Operators can input the required fill volume and other parameters through a user-friendly interface, often a touchscreen, making the system highly flexible and easy to use.
- Nozzles and Filling Heads: These are the components through which the perfume is dispensed into the bottles. Modern machines often feature anti-drip nozzles to prevent leakage and maintain cleanliness during the filling process.
- Safety Features: Given that perfumes can contain volatile and flammable substances, many filling machines are equipped with safety features such as explosion-proof designs and emergency stop functions to protect both the product and the operators.
Types of Perfume Filling Machines
Perfume filling machines can be categorized based on their operation mode and production capacity:
- Manual Perfume Filling Machines: These are ideal for small-scale operations where production volume is low. They require manual intervention to operate and are best suited for artisanal or boutique perfume brands.
- Semi-Automatic Perfume Filling Machines: These machines strike a balance between manual and automatic operations. While they still require some human intervention, they significantly reduce the workload and increase production efficiency compared to fully manual machines.
- Automatic Perfume Filling Machines: Designed for large-scale industrial production, these machines operate with minimal human intervention. They can handle large volumes of bottles per hour and are equipped with advanced features such as automatic bottle feeding, limitación, and labeling.
Benefits of Using Perfume Filling Machines
The adoption of perfume filling machines in fragrance production offers numerous advantages:
- Increased Efficiency: Automatic filling machines can fill thousands of bottles per hour, significantly increasing production capacity. This is particularly beneficial for large perfume manufacturers who need to meet high demand.
- Precision and Consistency: These machines are designed to deliver exact fill volumes, ensuring that every bottle contains the same amount of perfume. This consistency is crucial for maintaining product quality and consumer trust.
- Reduced Wastage: By accurately controlling the amount of perfume dispensed, these machines minimize spillage and overfilling, leading to reduced wastage of expensive perfume liquids.
- Producción rentable: While the initial investment in a perfume filling machine can be significant, the long-term savings in labor costs, reduced wastage, and increased production efficiency make them a cost-effective solution for perfume manufacturers.
- Enhanced Hygiene and Safety: Perfume filling machines are often designed with materials that comply with hygiene standards, such as stainless steel. Además, features like anti-drip nozzles and explosion-proof designs enhance safety during the production process.
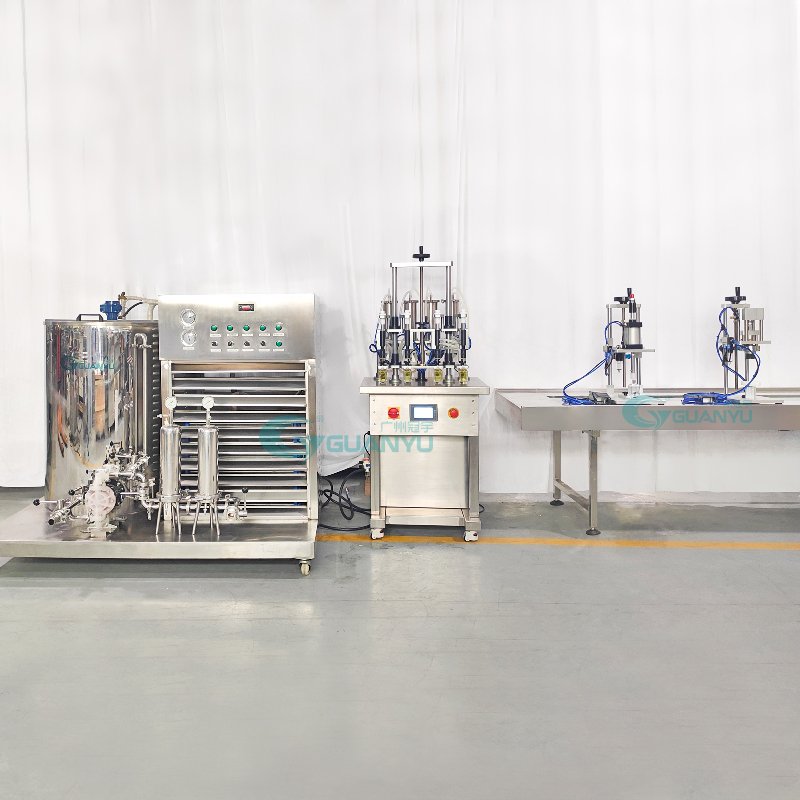
The Role of Perfume Filling Machines in the Industry
The fragrance industry is highly competitive, with brands constantly striving to differentiate themselves through unique scents, high-quality packaging, and consistent product offerings. Perfume filling machines play a crucial role in this process by enabling manufacturers to maintain high standards of quality and efficiency.
In addition to their practical benefits, these machines also support the industry’s move towards sustainability. By reducing waste and improving production efficiency, perfume filling machines contribute to more sustainable manufacturing practices. This is increasingly important as consumers become more environmentally conscious and demand more responsible production methods from their favorite brands.
Innovations and Future Trends
As technology continues to evolve, so too do perfume filling machines. Modern machines are increasingly integrated with advanced technologies such as IoT (Internet of Things) and AI (Artificial Intelligence), enabling real-time monitoring, predictive maintenance, and further automation of the production process. These innovations not only enhance the efficiency and reliability of the machines but also allow manufacturers to gather valuable data that can be used to optimize production and improve product quality.
Furthermore, the trend towards customization in the fragrance industry is leading to the development of more flexible and versatile filling machines. These machines can handle a wider range of bottle sizes and shapes, allowing brands to offer personalized products to their customers.
About us Compañía de maquinaria Guanyu
◭ 25 Años: Guangzhou Guanyu Machinery Co.ltd se ha dedicado a la investigación y fabricación de maquinaria para médicos, productos químicos para alimentos e industriales para 25 años.
◭ nuestra propia fábrica: Nuestra fábrica tiene 7000 metros cuadrados, más que 100 trabajadores, y 6 líneas de producción de máquinas, incluida la fabricación de máquinas, pulido, y prueba.
◭ maquinaria personalizada: Nuestros principales productos incluyen máquinas emulsionantes al vacío fijas., homogeneizadores móviles, Todo tipo de calderas agitadoras de reacción..
◭ Productos aplicables: Son adecuados para hacer crema, loción, productos líquidos, incluyendo crema facial, ungüentos, ketchup, mayonesa, atasco, jabón de manos, champú, etc..
◭ Certificaciones: CE, BPM, Certificados de tecnología UL y patentados.
Conclusión
Perfume filling machines are indispensable in the modern fragrance industry, offering a range of benefits from increased efficiency and precision to enhanced safety and sustainability. As technology advances, these machines will continue to evolve, supporting the industry’s growth and adaptation to changing consumer demands. For perfume manufacturers, investing in a high-quality filling machine is not just a matter of improving production efficiency—it’s a step towards ensuring the long-term success and sustainability of their brand.