Lipstick es uno de los productos de belleza más populares del mundo. Con una amplia gama de colores, acabados, y texturas, Este elemento básico cosmético tiene un complejo proceso de fabricación. En este artículo, Exploraremos cómo se hace lápiz labial, El papel de varios ingredientes, y la importancia de las máquinas en el proceso de producción.
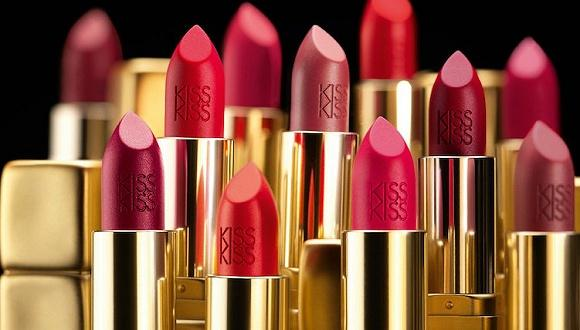
What Are the Main Ingredients in Lipstick?
To understand how lipstick is made, it’s essential to know what goes into it. The core ingredients of lipstick generally include:
- Waxes: Waxes like beeswax, carnauba wax, and candelilla wax provide the shape and structure of the lipstick. They help create a solid form that can be molded and applied smoothly.
- Oils: Castor oil, olive oil, mineral oil, and lanolin are common oils used in lipstick. They give the product a creamy texture and make it easy to glide on the lips.
- Pigments: Pigments add color to the lipstick. They can be natural, such as mica and iron oxide, or synthetic, to achieve a wider range of vibrant colors.
- Emollients: Emollients help moisturize the lips. Ingredients like shea butter, cocoa butter, and aloe vera are often added for this purpose.
- Preservatives and Antioxidants: These ingredients help maintain the quality and safety of the lipstick, extending its shelf life by preventing the oils from going rancid.
- Fragrances and Flavorings: These optional ingredients add a pleasant scent or taste to the lipstick, enhancing the overall user experience.
Step-By-Step Guide to Lipstick Production
1. Melting and Mixing
The first step in lipstick production is to melt and mix the ingredients. Waxes are usually heated in a lipstick making machine, like the one shown in the image. These machines are equipped with temperature control panels to ensure precise heating and mixing. Waxes, oils, and emollients are melted together at around 175°F (80°C). The mixing must be thorough to avoid lumps and ensure a smooth texture.
Modern lipstick-making machines are designed with double-layered mixing tanks that keep the temperature consistent, allowing for a high-quality blend of ingredients. Machines like these have automatic mixers that can continuously stir the mixture, ensuring even distribution of pigments and a smooth final product.
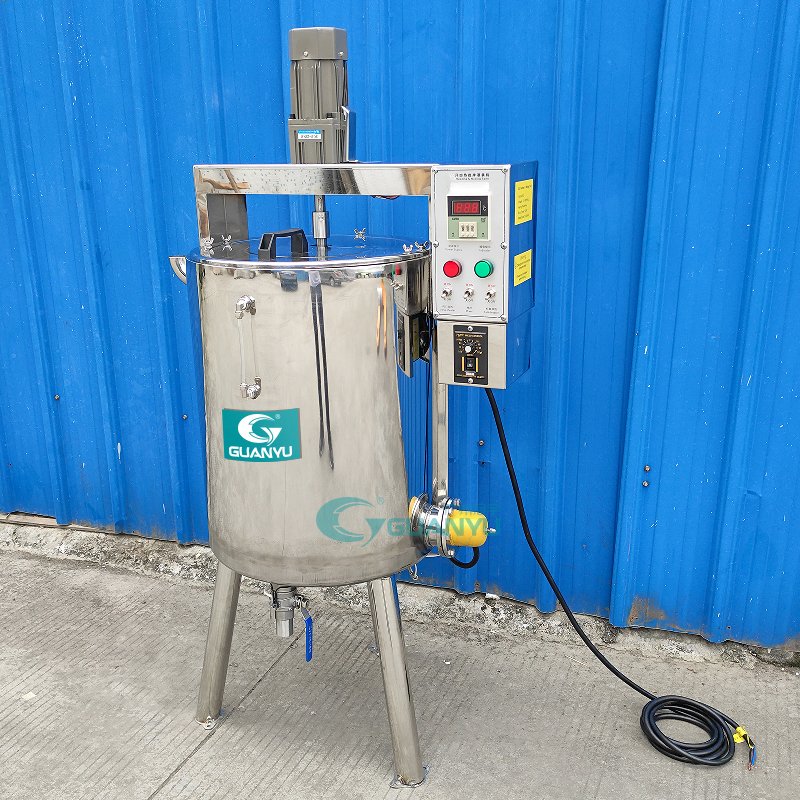
2. Adding Pigments and Other Ingredients
Once the waxes and oils are melted and blended, pigments are added. This is a critical step in the process, as it determines the lipstick’s final color and consistency. Pigments must be finely milled and evenly distributed to achieve a uniform color.
Lipstick manufacturing machines come with high-shear mixers that help break down pigment particles and blend them seamlessly with other ingredients. This ensures the color is smooth and doesn’t streak when applied. Other additives, such as emollients and preservatives, are also mixed in at this stage.
3. Refining the Mixture
Refining involves breaking down the pigment particles further to create a smooth consistency. This is done using specialized equipment known as three-roll mills o homogenistas. The refining process is essential for achieving the rich, even texture that high-quality lipsticks are known for.
Machines that have a triple-roller mechanism help create a smooth, homogenous product. The mixture passes through these rollers, which ensure that the pigment is finely dispersed, eliminating any grainy or uneven texture.
4. Molding and Shaping
Once the lipstick mixture has been thoroughly blended and refined, it is ready for molding. The warm mixture is poured into molds shaped like lipstick bullets. Molds are often made from metal and are cooled to help the lipstick set quickly.
Modern lipstick machines allow for automated molding and cooling, which speeds up the production process. After the lipstick hardens, it is removed from the mold and placed in the lipstick tubes.
Molding machines have precision filling mechanisms to ensure that each lipstick has the exact amount of product. This helps avoid product wastage and ensures uniformity in the final products.
5. Cooling and De-molding
After being poured into molds, the lipstick needs to cool down to maintain its shape. Machines equipped with cooling systems speed up this process. As the mixture cools, it solidifies into the desired shape.
In commercial lipstick production, a quick cooling system is essential to keep up with high demand. This equipment usually works by circulating cold air or water around the molds, allowing for consistent and rapid cooling.
6. Flaming and Finishing
Once the lipstick is cooled and solidified, it undergoes a process known as “flaming.” Flaming involves passing the lipstick through a small open flame or heating element to smooth out any imperfections and give it a glossy finish. This step is especially important for high-end lipsticks that require a flawless appearance.
Machines with built-in flaming tools make this process seamless. They provide a controlled flame that briefly melts the outer layer of the lipstick, giving it a smooth, professional finish.
7. Embalaje
The final step is packaging the lipsticks in their cases. Modern lipstick making machines often come with automated packaging features, where each lipstick bullet is loaded into a casing mechanically. The casings are then inspected for quality control before being sealed and labeled for distribution.
Automated packaging not only saves time but also reduces the risk of contamination. In a high-production setting, these machines play a critical role in keeping the manufacturing process efficient and sanitary.
Types of Lipstick Making Machines
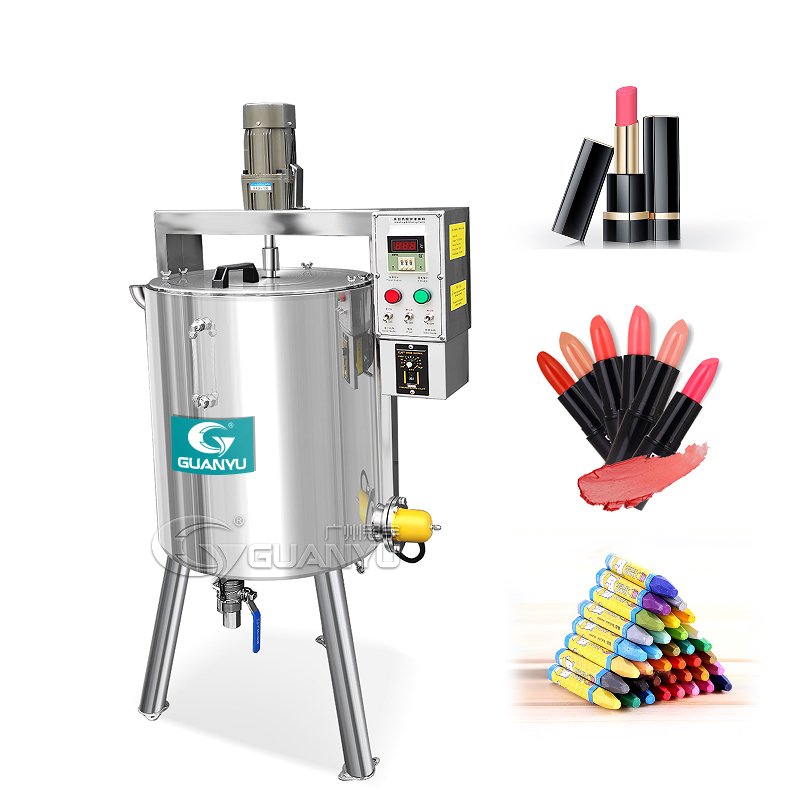
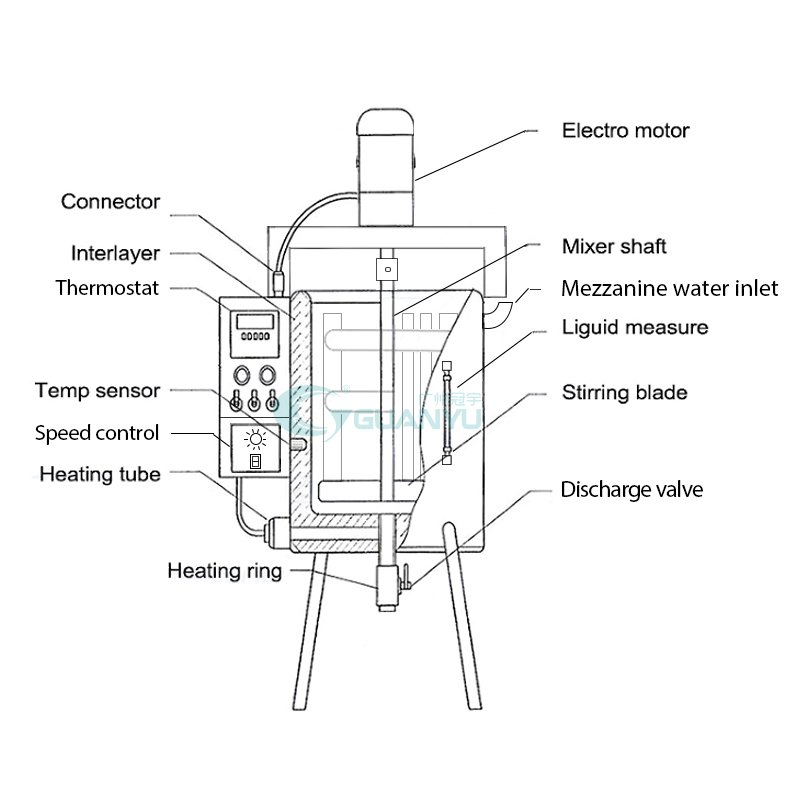
There are various types of lipstick making machines, each designed for a specific part of the production process. Here’s a look at some of the main types:
- Melting and Mixing Machines: These are essential for the initial blending of ingredients. They come with temperature controls and high-shear mixing capabilities.
- Homogenizers and Three-Roll Mills: These machines refine the lipstick mixture to achieve a smooth texture. They are used after pigments have been added to the base mixture.
- Lipstick Molding Machines: These machines are used to shape the lipstick. They come with pre-made molds and can automate the pouring, cooling, and de-molding process.
- Flaming and Finishing Machines: These are used for adding a smooth, glossy finish to the lipstick. They are often integrated with cooling systems for better efficiency.
- Automated Packaging Machines: These machines help pack lipsticks into cases and prepare them for shipment. They ensure hygiene and consistency in the packaging process.
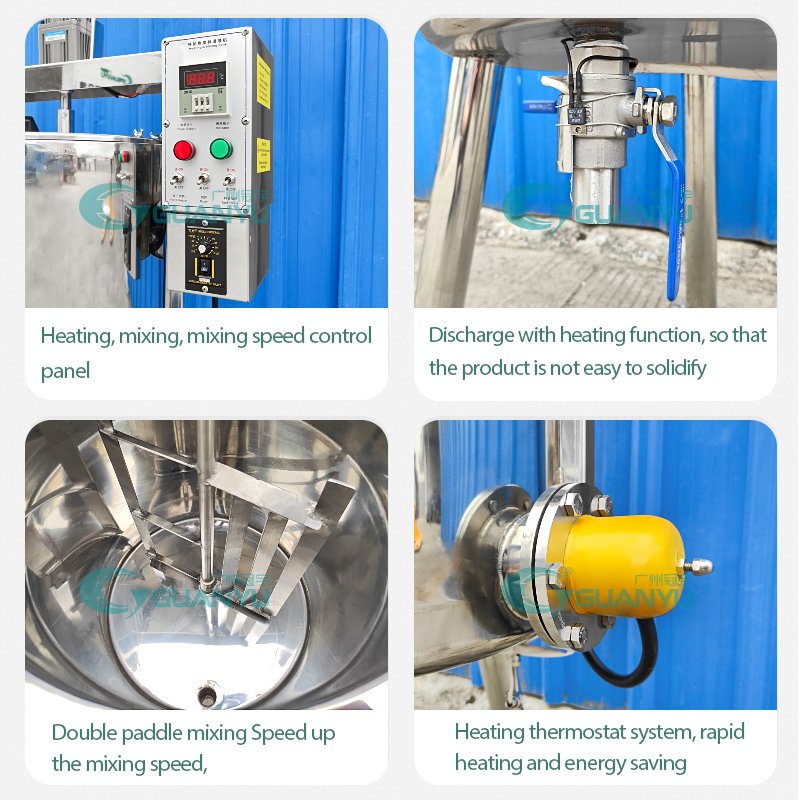
The Benefits of Using Lipstick Making Machines
Investing in specialized lipstick making machines has several benefits for manufacturers:
- Increased Efficiency: Machines automate complex processes, significantly reducing production time.
- Consistencia: Automated systems ensure each lipstick has the same texture, color, and finish.
- Hygiene: Machines reduce human handling, maintaining hygiene standards essential in cosmetics manufacturing.
- Cost-Effective: Although initial investments in machines can be high, they ultimately save money by reducing waste and labor costs.
- Escalabilidad: With machines, manufacturers can scale up production to meet market demand without sacrificing quality.
Conclusión
The art and science of lipstick manufacturing are intricate, involving various ingredients, precise techniques, and sophisticated machinery. The use of specialized lipstick making machines has revolutionized the production process, allowing manufacturers to create high-quality products with efficiency and consistency. From melting and mixing to molding, cooling, and flaming, each machine plays a vital role in delivering the perfect lipstick.
For businesses aiming to produce lipsticks on a large scale, investing in these machines is crucial. They not only enhance the production speed but also ensure that every lipstick meets the desired quality standards, satisfying the expectations of customers around the world.
For a more efficient and cost-effective lipstick manufacturing process, the integration of advanced machines is indispensable in today’s cosmetic industry.