Introduction
With the explosive growth of the new energy sector, particularly in the development and mass production of lithium-ion batteries, demand has surged for efficient, safe, and customizable production equipment. Among the most essential pieces of equipment in this industry is the chemical reactor—specifically designed to handle complex chemical reactions, precise mixing, and dispersion processes.
This article explores the vital role of chemical reactors in lithium battery production, focusing on stainless steel reactors equipped with stirrers and dispersers, and the increasing importance of customizable explosion-proof features.
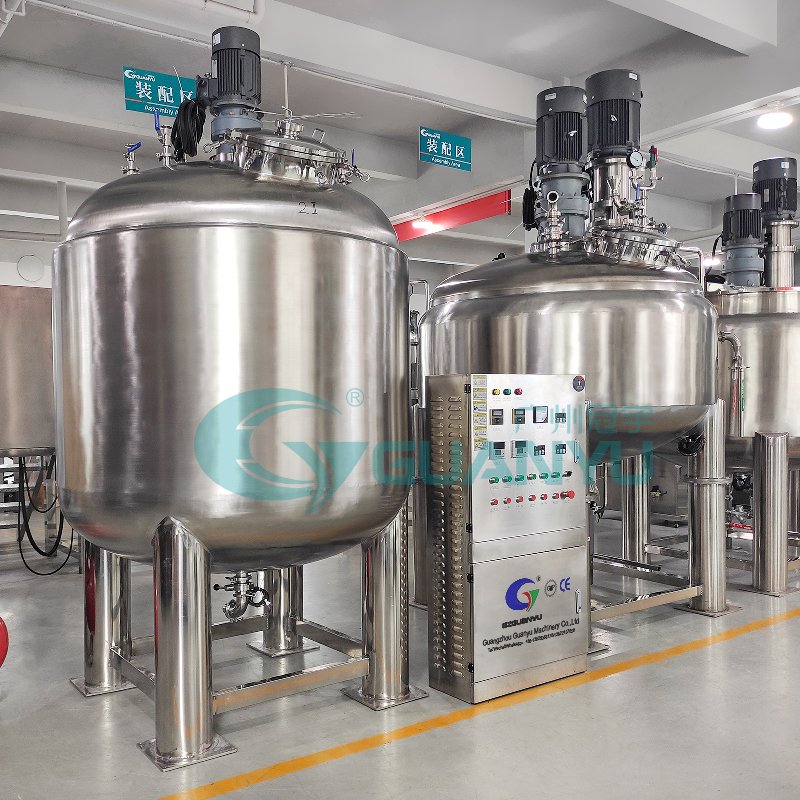
I. Understanding Lithium Battery Manufacturing Needs
1.1 The Rise of Lithium Batteries
Lithium batteries power everything from smartphones to electric vehicles (EVs), energy storage systems, and even aerospace applications. The lithium battery production process is both chemically intensive and highly sensitive to contamination and inconsistency, which makes advanced process equipment a necessity.
1.2 Core Production Processes That Require Reactors
Key steps in lithium battery material production involving reactors include:
- Cathode and anode slurry preparation
- Synthesis of lithium salts and additives
- Binder and electrolyte formulation
- Precursor co-precipitation for cathode materials
These processes require precise temperature control, efficient dispersion, and safe chemical handling, which is why high-quality chemical reactors are a fundamental part of the production line.
II. Stainless Steel Reactors: Why They’re Ideal for Lithium Battery Production
2.1 Corrosion Resistance
Lithium battery materials often involve highly reactive chemicals such as hydroxides, carbonates, and fluorinated compounds. Stainless steel reactors, especially those made from SS316L or SS304, offer excellent resistance to chemical corrosion and maintain structural integrity over time.
2.2 High Cleanliness Standards
The battery industry requires a clean and contamination-free environment. Stainless steel is non-porous and easy to sterilize, making it perfect for ensuring the purity of battery materials.
2.3 Mechanical Strength and Versatility
Stainless steel reactors can handle:
- High operating pressures and temperatures
- Heavy, high-viscosity slurries
- Multiple-phase mixing (solid-liquid, liquid-gas)
This makes them versatile for various sub-processes within the lithium battery industry.
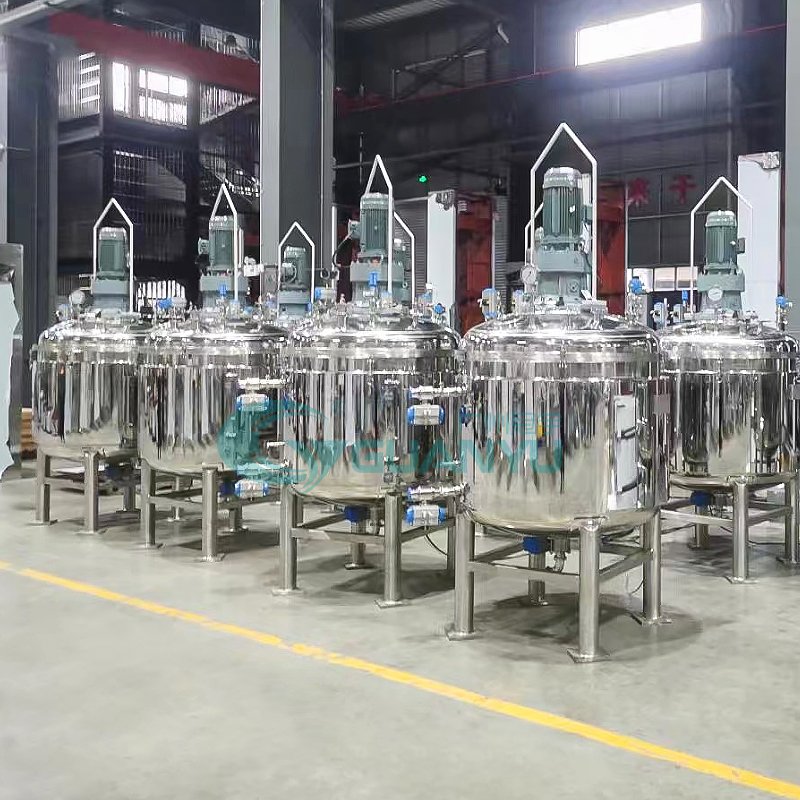
III. Key Features of Chemical Reactor for Lithium Battery
3.1 Integrated Stirring and Dispersion Systems
Modern chemical reactors for lithium batteries often come with dual-function agitation systems, incluido:
- Stirrers (paleta, ancla, or propeller types) to ensure macro-level mixing
- Dispersers (high-speed or sawtooth types) to break down solid particles and ensure even distribution
These integrated systems are crucial for:
- Preventing sedimentation of active materials
- Achieving consistent viscosity
- Enhancing electrochemical performance of the final product
3.2 Explosion-Proof Design for Safety
Given the flammable nature of many battery precursors and solvents, explosion protection is a vital requirement. Common explosion-proof features include:
- Flameproof motors and control panels
- Overpressure relief valves
- Inert gas blanketing systems
- Anti-static grounding
- Sealed design to prevent vapor leaks
Manufacturers can also customize reactors to meet ATEX or IECEx standards, depending on regional safety compliance requirements.
3.3 Temperature and Pressure Control
Reactions in battery production often require precise control over reaction environments. Stainless steel reactors come with:
- Jacketed vessels for temperature regulation using oil, steam, or chilled water
- Sensors and PLC systems for monitoring internal conditions
- Vacuum or pressurization options to support specific chemical processes
IV. Customization Options for Lithium Battery Applications
Each battery manufacturer may have slightly different formulation techniques and process conditions. Hence, customizable chemical reactors have become a trend in this industry.
4.1 Custom Volume Ranges
Reactors can be designed for:
- Lab-scale R&D (5–100L)
- Pilot scale (100–1000L)
- Mass production (1000–10000L or more)
This allows manufacturers to scale efficiently without changing equipment types.
4.2 Material Options
Beyond stainless steel, some setups may use:
- PTFE lining for extreme corrosion resistance
- Glass-lining for visual inspection and inert reactions
But stainless steel remains the most widely used due to its balance of strength, durability, and cost-efficiency.
4.3 Automation and Control Integration
Modern chemical reactors can be integrated into fully automated production lines with:
- Programmable logic controllers (SOCIEDAD ANÓNIMA)
- Human-machine interfaces (HMI)
- Real-time monitoring systems
- Data logging for quality traceability
This is particularly important in high-throughput environments where process repeatability is critical.
V. Applications of Stainless Steel Reactors in Lithium Battery Production
5.1 Cathode and Anode Material Preparation
Reactors are used to mix and process materials such as:
- Lithium iron phosphate (LFP)
- Nickel-cobalt-manganese (NCM/NCA)
- Graphite and silicon-based anodes
Precise stirring and dispersion help ensure active materials are coated evenly and maintain optimal particle sizes.
5.2 Electrolyte Synthesis
Although typically performed in smaller volumes due to the sensitive nature of electrolytes, reactors are used to:
- Blend solvents like ethylene carbonate (EC) y dimethyl carbonate (DMC)
- Dissolve lithium hexafluorophosphate (LiPF₆)
- Integrate additives like vinylene carbonate (VC)
Stainless steel reactors with explosion-proof configurations are particularly valuable in this stage due to the flammable components involved.
5.3 Binder and Slurry Preparation
Binders such as PVDF y CMC/SBR systems require thorough mixing with active materials and conductive agents. These slurries are then coated on current collectors. Reactors provide the necessary agitation and viscosity control to produce slurries that are stable, uniform, and easy to apply.
VI. Trends Driving Demand for Advanced Chemical Reactors
6.1 Energy Density and Material Innovation
With the push for higher energy density y faster charging, material innovation is advancing rapidly. Reactors must now handle:
- More complex, multi-component mixtures
- Nano-structured materials
- Environmentally sensitive ingredients
6.2 Environmental and Safety Compliance
As global regulations tighten, battery manufacturers are demanding:
- Solvent recovery systems
- Waste management integration
- Explosion-proof certifications
Modern reactors must align with both environmental y occupational safety standards.
6.3 Localization and Custom Engineering
Countries investing in local battery production (e.g., Porcelana, U.S., Alemania, India) are working with reactor manufacturers that offer localized support, fast turnaround on custom builds, and on-site installation services.
Conclusión
The lithium battery industry depends heavily on the calidad, seguridad, and flexibility of its production equipment. Stainless steel chemical reactors equipped with advanced mixing and dispersing systems, custom explosion-proof features, y scalable designs are becoming the standard across the sector.
By investing in reliable and efficient reactors, battery manufacturers can ensure high material consistency, greater energy output, and safer production lines—key factors in staying competitive in the booming global energy storage market.
If you’re seeking dependable mixing solutions for lithium battery applications, consider working with suppliers who specialize in customizable stainless steel chemical reactors designed for the next generation of battery technology.
Chemical Reactor for Lithium Battery Chemical Reactor for Lithium Battery Chemical Reactor for Lithium Battery Chemical Reactor for Lithium Battery