Top Trends in Vacuum Emulsifying Mixers
In the world of manufacturing and processing industries, vacuum emulsifying mixers have become an essential tool for achieving high-quality products. These mixers are widely used in industries such as cosmetics, Arzneimittel, and food, where the emulsification process plays a crucial role in product development. In recent years, several trends have emerged in the field of vacuum emulsifying mixers, bringing about industry-defining innovations.
1. Advanced Automation and Control Systems
The incorporation of advanced automation and control systems in vacuum emulsifying mixers has revolutionized the manufacturing process. These systems enable precise control over various parameters such as mixing speed, temperature, and pressure, resulting in consistent and reproducible product quality. Additionally, automation reduces human error and increases operational efficiency.
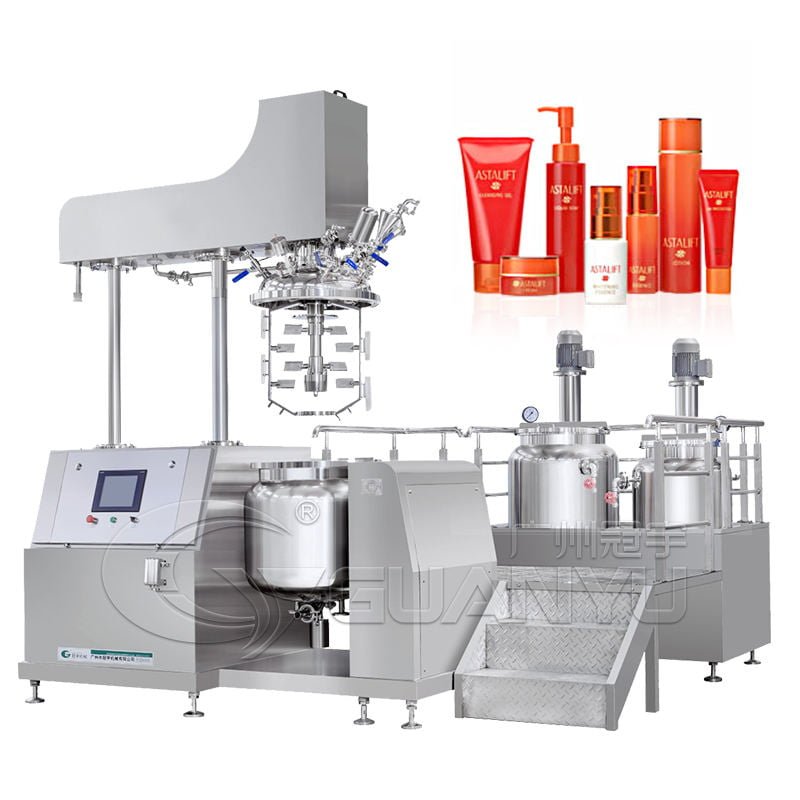
2. Enhanced Safety Features
Safety is of utmost importance in any manufacturing environment. Vacuum emulsifying mixers now come equipped with enhanced safety features such as emergency stop buttons, interlocking systems, and safety sensors. These features ensure operator safety and prevent accidents, making them an indispensable part of modern vacuum emulsifying mixers.
3. Integration of Process Monitoring and Data Logging
Real-time process monitoring and data logging have become crucial in the manufacturing industry. Vacuum emulsifying mixers now offer integration with monitoring systems that provide valuable insights into the mixing process. This data can be used for process optimization, quality control, and regulatory compliance.
4. Energy Efficiency
With the growing emphasis on sustainability, energy-efficient vacuum emulsifying mixers have gained popularity. These mixers are designed to minimize energy consumption without compromising on performance. Energy-efficient features such as variable speed drives, insulation, and optimized design contribute to significant energy savings.
5. Customization and Flexibility
Manufacturers are increasingly demanding vacuum emulsifying mixers that can be tailored to their specific needs. The industry is responding by offering customizable options in terms of vessel size, mixing capacity, and additional functionalities. This flexibility allows manufacturers to optimize their production processes and meet unique requirements.
In conclusion, the vacuum emulsifying mixer industry is witnessing significant advancements in automation, Sicherheit, monitoring, energy efficiency, and customization. These trends are shaping the future of manufacturing and enabling industries to achieve higher levels of product quality, efficiency, and sustainability.