Introduction to Filling and Capping Machines
Filling and capping machines play a crucial role in the packaging industry, offering solutions that significantly enhance efficiency and accuracy in the bottling process. These automated systems are designed to streamline the operations involved in filling containers with a variety of products, including liquids, creams, honey, and more. By integrating both filling and capping in one machine, manufacturers can optimize their production lines, thereby reducing the time and labor required for these essential tasks.
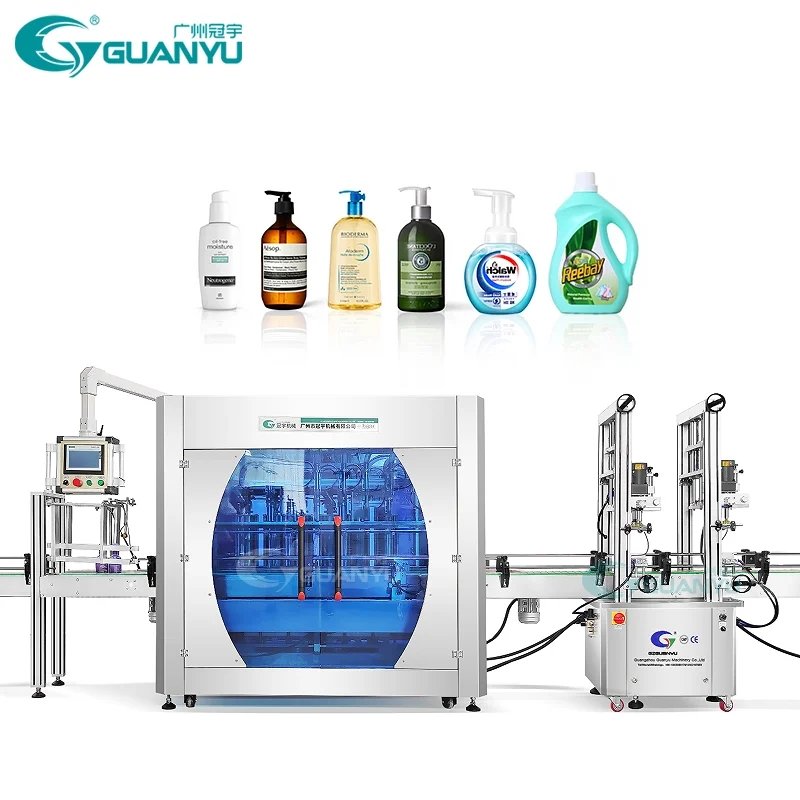
The operation of filling and capping machines is characterized by state-of-the-art technology and precision engineering. These machines utilize multiple nozzles, allowing for simultaneous filling of multiple containers, which is particularly advantageous for high-demand production scenarios. The nozzles are carefully calibrated to ensure consistent fill levels, minimizing waste and reducing overfilling, which can lead to product loss. Furthermore, filling machines are adaptable to a range of product viscosities, accommodating everything from thin liquids to thicker creams and gels.
Moreover, capping machines complement the filling process by securely sealing containers to prevent leakage and maintain product integrity. Various capping methodologies are employed, including screw-on caps, snap-on lids, and induction sealing processes. The choice of capping technology is often dependent on the specific requirements of the product and the demands of the market. Industries such as food and beverage, Kosmetika, Arzneimittel, and chemicals greatly benefit from the implementation of these machines, as they not only enhance productivity but also assure consistent quality in packaging.
Incorporating filling and capping machines into production lines signifies a commitment to improving operational efficiency and product quality. As businesses continue to seek ways to optimize their packaging processes, the adoption of fully automatic filling and capping systems will likely remain a significant trend within the industry.
Understanding Fully Automatic Filling Machines
Fully automatic filling machines represent a significant advancement in packaging technology, specifically designed for the high-volume production of liquid and viscous products such as creams, honeys, and sauces. These machines operate with minimal human intervention, utilizing a combination of sophisticated sensors and automation systems to ensure precision and efficiency in the filling process. The core functionality of fully automatic filling machines involves accurately measuring the product and dispensing it into containers at a rapid pace, enhancing productivity while maintaining consistency and quality.
One of the main advantages of fully automatic machines over their semi-automatic counterparts is their ability to operate continuously without the need for manual loading or monitoring. This feature not only reduces labor costs but also minimizes the potential for human error, leading to a more reliable and uniform filling process. Moreover, the integration of advanced technology such as programmable logic controllers (PLCs) allows for easy adjustments and programming of different product specifications, facilitating seamless transitions between various fill sizes and types.
The technology behind fully automatic filling machines is characterized by a variety of sensors that monitor key variables such as fill levels, pressure, and machine health. These sensors provide real-time feedback to the system, enabling it to make instantaneous adjustments to maintain optimal performance. Automation systems work in tandem with these sensors to regulate the speed and timing of each filling cycle, ensuring that containers are filled accurately and efficiently with minimal interruptions.
In summary, fully automatic filling machines are designed for high efficiency and precision, crucial for industries requiring fast and accurate packaging. Their advanced technology and reduced reliance on human operators distinguish them from semi-automatic machines, making them a preferred choice for businesses aiming to scale operations and enhance production reliability.
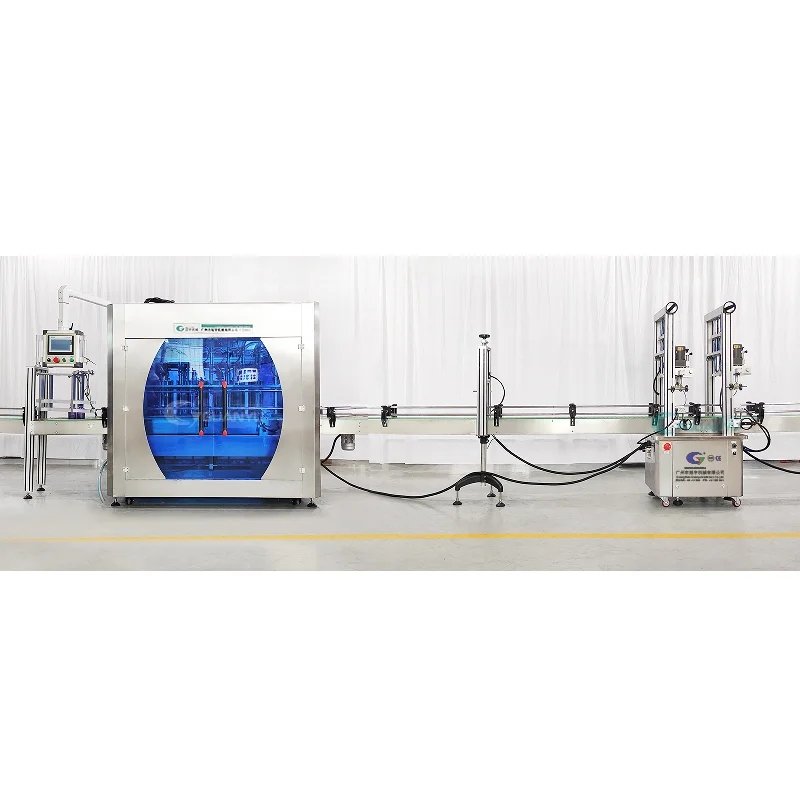
Key Features of 12 Nozzle Filling Machines
Fully automatic 12 nozzle filling machines are designed to enhance the efficiency and productivity of the bottling process for various liquids, including creams and honey. One of the most significant features of these machines is their high filling capacity. Equipped with twelve nozzles, they can fill multiple containers simultaneously, reducing the time required for bottling operations. This feature is particularly beneficial for businesses with large production demands, as it allows them to scale up their output without compromising quality.
Another essential aspect to consider is the speed of filling operations. A 12 nozzle filling machine can achieve impressive production speeds, often exceeding 100 containers per minute, depending on the viscosity of the product being filled. This rapid filling rate streamlines operations and enables businesses to meet tight deadlines while maintaining a steady workflow.
Precision is a crucial feature of 12 nozzle filling machines. These machines are designed to minimize spillage and ensure that each container is filled accurately. Modern servo-driven technology allows for precise control over fill levels, which is vital for products that require consistent packaging. This level of accuracy not only reduces waste but also supports brand consistency, as consumers expect uniform product quantities.
Versatility is another hallmark of 12 nozzle filling machines. They can handle a variety of liquid types, including creams, oils, honey, and more, making them suitable for diverse industries. The machines can be easily adjusted to accommodate different container sizes and shapes, allowing businesses to adapt to changing market needs without investing in additional equipment.
Overall, the key features of 12 nozzle filling machines significantly contribute to operational efficiency. By optimizing capacity, speed, Präzision, and versatility, these machines facilitate a more effective bottling process that can enhance productivity and profitability for manufacturers.
Anwendungen von 12 Nozzle Filling Machines
12 nozzle filling machines serve a wide range of applications across various industries, significantly enhancing productivity and efficiency in the packaging process. These machines are particularly well-suited for filling viscous products, such as creams, honey, tomato paste, and dishwashing liquids. The design facilitates precise and rapid filling, which is crucial for meeting production demands and maintaining product quality.
In the cosmetic industry, 12 nozzle filling machines are commonly employed for filling creams and lotions. These products often have varying viscosities, and the automatic nature of the machines allows for adjustments to accommodate different thickness levels. By utilizing a 12 nozzle system, manufacturers can achieve higher throughput while ensuring consistent filling, which minimizes waste and optimizes resources.
For the food industry, honey is another prominent application of 12 nozzle filling machines. The viscous nature of honey poses challenges during the packaging process, as it requires specialized handling to prevent dripping and product loss. The precision offered by these machines allows for accurate fills that enhance the aesthetics of the packaging while ensuring compliance with industry standards. This facilitates a smooth production line that is crucial for dealing with high volumes of output.
Moreover, the filling of tomato paste is enhanced through the use of 12 nozzle filling machines, as these products require a balance between speed and accuracy. The automatic features allow for maintaining consistent fill levels, which is essential for product uniformity and consumer satisfaction. Additionally, dishwashing liquids benefit from the versatility of these machines, which can handle varying viscosity levels while ensuring quick turnaround times.
Incorporating 12 nozzle filling machines into these industries not only maximizes efficiency but also supports manufacturers in scaling their operations seamlessly. The diverse applications across each sector highlight the machines’ integral role in modern production environments.
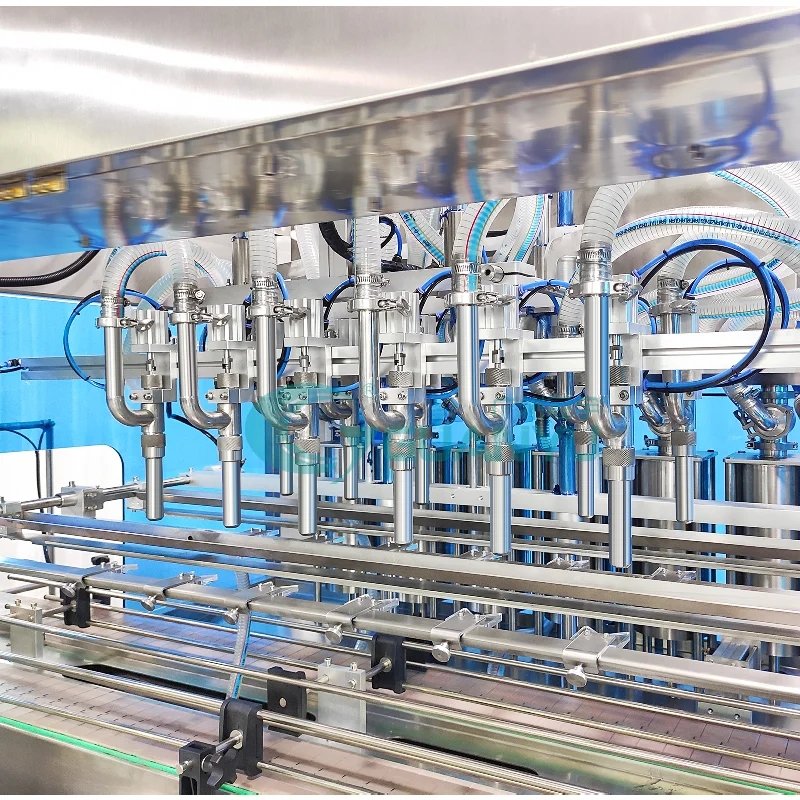
The Importance of Accurate Filling in the Packaging Industry
Accurate filling is a critical component of the packaging industry, especially for products such as creams, honey, and other viscous substances. The precision of the filling process directly influences not just the quality of the product but also the efficiency of the production line. Implementing fully automatic filling machines, particularly those equipped with a 12 nozzle system, significantly enhances the accuracy of the filling process. This technology minimizes human error, ensuring consistent volume and reducing product waste.
Inaccurate filling can lead to numerous issues, including product overfills or underfills, which ultimately result in financial losses. For instance, overfilling can increase material costs, while underfilling may lead to customer dissatisfaction and potentially harm the brand’s reputation. Furthermore, the inconsistency in filling can create discrepancies in regulatory compliance, especially for product labeling that often specifies net quantities. daher, achieving accuracy in the filling stage is not just a matter of operational efficiency but also of adhering to industry standards.
The capabilities of automatic filling machines, particularly those designed for high-volume production, ensure that product consistency is maintained throughout a production run. These machines utilize advanced technologies such as sensors and automated controls to monitor and adjust the filling process in real-time. The reliance on automation significantly reduces the likelihood of human error, which can frequently occur in manual filling processes. By employing precision engineering, full automatic machines can consistently achieve targeted fill volumes, ensuring that each container is correctly filled.
Ultimately, the importance of accurate filling cannot be overstated in the packaging industry. Investing in technology that guarantees precision not only optimizes production efficiency but also enhances the overall quality of the product. This commitment to excellence will lead to greater consumer trust and satisfaction, bolstering a brand’s market position.
Capping Systems: Types and Benefits
Capping systems play a critical role in the efficiency and effectiveness of filling machines, particularly in industries that package products like creams, honey, and other viscous materials. The choice of capping system can significantly impact the integrity and shelf life of the packaged goods. There are several types of capping systems available, each designed to serve particular applications and enhance product security.
One of the most commonly used capping systems is the screw cap. This type utilizes a rotating mechanism to firmly apply the cap, creating a tamper-evident seal that ensures product safety and longevity. Screw caps are particularly beneficial for products that require airtight conditions, making them ideal for creams and other cosmetics that could degrade with exposure to air. They are also available in various sizes and materials, providing flexibility according to the packaging needs.
Another popular option is the snap-on cap, which is designed for ease of application and removal. This type of capping system is typically made from flexible plastic and snaps securely onto the container, offering convenience for end-users. Snap-on caps are often favored for honey and other viscous liquids, as they allow for quick access while maintaining product freshness. Additionally, these caps can be designed to allow for one-handed operation, making them more user-friendly.
Other notable capping options include induction seals and roll-on/bottle caps. Induction seals provide an extra layer of security, as they bond with the container through a heat process, ensuring that the product has not been tampered with prior to opening. Roll-on caps, meanwhile, are applied using a roller mechanism, offering a reliable seal for bottles containing thicker liquids.
In selecting a capping system, manufacturers should consider the specific advantages of each type. By aligning the capping option with the needs of the product, companies can enhance packaging efficiency and maintain the quality of their offerings, ultimately improving consumer satisfaction.
Choosing the Right Filling and Capping Machine for Your Business
When selecting a filling and capping machine for your business, it is crucial to consider several key factors that can significantly impact your production efficiency and product quality. The first and foremost consideration is production volume. Businesses with high-demand products may require fully automatic machines that can handle larger batches with minimal downtime. In contrast, smaller operations might benefit from semi-automatic systems that still provide consistent results without the financial burden of high-capacity equipment. Understanding your production requirements will guide you in selecting a machine that aligns with your operational goals.
Another important factor to assess is the type of product being packaged. Different products, such as creams, liquids, or viscous substances like honey, often require specific filling techniques and capping solutions. Zum Beispiel, a cream might necessitate a machine with adjustable filling volumes and speeds to ensure accurate dosing and minimal waste. In contrast, a liquid product might benefit from a machine designed for rapid filling and leak-proof capping. daher, it’s essential to match the machine’s capabilities to the nature of the product to enhance efficiency and ensure the integrity of the packaged item.
Operational flexibility is also a vital component to consider when choosing the right filling and capping machine. Businesses should evaluate how easily a machine can adapt to changes in production volume or product variations. A machine that allows for quick format changes can provide significant advantages, especially in industries where consumer preferences may shift frequently. Ultimately, a thorough analysis of these factors—production volume, product type, and operational flexibility—will empower businesses to make informed decisions, leading to improved operational efficiency and better product quality in their packaging processes.
Maintenance and Troubleshooting of Filling and Capping Machines
Maintaining filling and capping machines is vital to ensuring their longevity and efficiency, especially for those that handle products like cream and honey, which can be viscous and require precision. Routine care is necessary to prevent breakdowns and to sustain optimal performance. Regular scheduled maintenance should include cleaning, lubrication, and inspection of parts. Machine operators should frequently check the filling nozzles for clogs, as these can directly impact the accurate dispensing of products. To facilitate proper cleaning, operators should follow the manufacturer’s recommendations regarding the use of specific cleaning solutions and inspect components such as pumps, hoses, and seals for wear.
Additionally, lubricating moving parts as per the outlined schedule can minimize friction and prevent premature wear. This can include bearings, drives, and pneumatic or electric motors. Inspecting electrical connections and ensuring that all components are securely fastened is also crucial. By keeping a log of maintenance activities, operators can track performance trends and proactively address potential issues before they escalate.
Troubleshooting common issues that arise during operation can further enhance the functionality of filling and capping machines. Operators may encounter problems such as inaccurate filling volumes or misaligned caps. For inaccurate filling, checking the calibration settings of the machine and ensuring that the filling nozzles are functioning correctly is essential. Capacitive sensors may need recalibration in certain machines. Misalignment of caps usually suggests that the capping head requires adjustment or that the machine is not level. Addressing these minor problems quickly can prevent larger complications and downtime.
In conclusion, routine maintenance and effective troubleshooting are integral to the optimal performance of fully automatic filling and capping machines. By adhering to a proactive maintenance schedule and promptly addressing any issues that arise, operators can maximize both the longevity and efficiency of their equipment.
Future Trends in the Filling and Capping Industry
The filling and capping industry is witnessing rapid changes driven by technological advances and evolving consumer preferences. One significant trend is the increasing shift towards advanced automation. Fully automatic filling and capping machines are becoming more prevalent, streamlining production processes and minimizing human error. Automation not only enhances the speed and efficiency of operations but also ensures consistent quality in the filling and capping of products such as creams, honey, and other viscous substances.
Moreover, eco-friendly packaging solutions have emerged as a pivotal focus for manufacturers. As sustainability becomes a critical concern, filling and capping operations are adapting to utilize recyclable and biodegradable materials. This shift aligns with consumer demand for greener products and enables companies to reduce their environmental footprint. The integration of eco-friendly packaging in fully automatic systems is thus considered a vital trend, leading to innovative designs and materials that meet both functional and ecological standards.
Another noteworthy trend is the incorporation of smart technology within filling and capping machines. These advancements include features such as Internet of Things (IoT) connectivity, enabling real-time monitoring and data collection. This capability allows manufacturers to optimize their production lines by gaining insights into operational processes and machine performance. Predictive maintenance, for instance, can be facilitated through smart technology, reducing downtime and increasing overall productivity.
As we look to the future, the filling and capping industry will likely continue to evolve with these transformative trends. The combination of automation, sustainable practices, and smart technology not only enhances operational efficiency but also caters to the growing demand for environmentally conscious and consumer-friendly products. Keeping abreast of these developments will be essential for businesses aiming to remain competitive in this dynamic landscape.