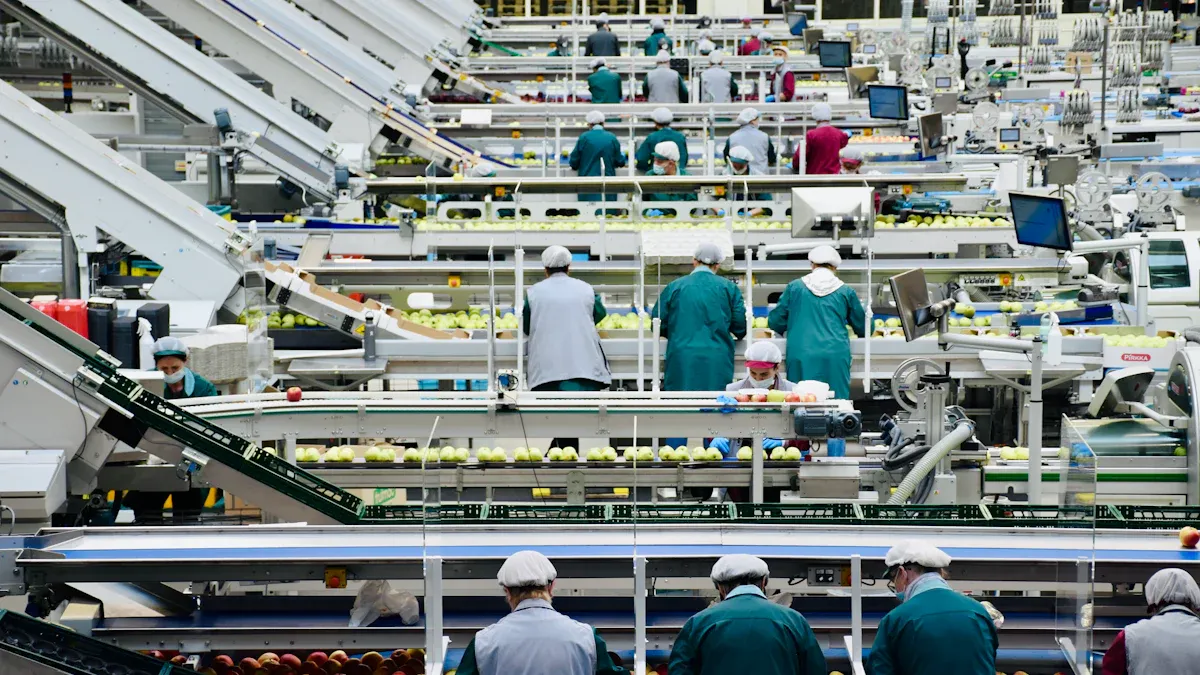
Efficiency in food production lines is key to meeting 2025 needs. Food and drink markets are growing by 6.2% each year. Factories must find ways to make more and work better. Improving food production lines helps cut costs and control quality. It also reduces waste, helping the planet. Using lean methods and new technology keeps things running smoothly and saves money. Companies like Guanyu offer custom solutions to help factories improve and stay ahead in a tough market.
Key Takeaways
1. Fast Production to Meet Market Demand
Implementation Steps and Tool Recommendations:
- Data Analysis and Forecasting:
- Use sales data and market trend analytics tools (such as Tableau or Power BI) to forecast product demands.
- Adjust production schedules in real time based on forecast results and historical demand patterns.
- Automation and Smart Production:
- Introduce automated production lines utilizing programmable logic controllers (PLCs) to monitor real-time production speeds.
- Integrate smart scheduling systems to align production output with market demand fluctuations.
Success Example:
A well-known fast-food chain implemented a big data analysis platform that synchronized production schedules with real-time sales data. As a result, the production efficiency increased by 20% while reducing material waste caused by inaccurate demand forecasting.
2. Preventative Equipment Maintenance to Reduce Downtime
Implementation Steps and Tool Recommendations:
- Routine Inspection Protocols:
- Develop and enforce weekly and monthly maintenance checklists for each piece of equipment.
- Document and track maintenance history using computer maintenance management systems (CMMS).
- Smart Monitoring Systems:
- Deploy IoT sensors (e.g., temperature, vibration, pressure sensors) to continuously monitor equipment health.
- Set up automated alerts so maintenance teams can address issues before they lead to breakdowns.
Success Example:
A food processing plant incorporated IoT sensors and a CMMS, which enabled early fault detection. This proactive approach led to a 30% reduction in downtime, cutting unexpected repairs and avoiding costly disruptions in the production line.
3. Optimized Process Design Boosts Efficiency
Implementation Steps and Tool Recommendations:
- Streamlined Workflow Design:
- Utilize process flow diagram tools such as Microsoft Visio or Lucidchart to map and optimize production line processes.
- Review and update the layout regularly to ensure smooth transitions between stages.
- Ergonomic Tools and Specialized Equipment:
- Invest in ergonomically designed tools and fixtures tailored to specific production tasks, reducing worker fatigue and error rates.
- Implement automated guided vehicles (AGVs) for efficient transportation of raw materials and finished products, minimizing manual handling.
Success Example:
A medium-sized food manufacturer restructured its production line by integrating AGVs and ergonomic tools. This redesign cut the production cycle by 25% while reducing labor intensity, leading to notable efficiency improvements.
4. Water Conservation and Waste Reduction for Environmental and Cost Benefits
Implementation Steps and Tool Recommendations:
- Water Recycling Systems:
- Install water treatment and recycling systems to ensure the purity and reuse of water within production processes.
- Monitor water usage with real-time management software to identify areas for further savings.
- Food Waste Management:
- Create a systematic approach to segregate and recycle production waste.
- Explore opportunities to repurpose food waste for energy generation (e.g., anaerobic digestion) or composting.
- Energy Efficiency Monitoring:
- Implement energy management systems (like Schneider Electric’s EcoStruxure) to monitor and optimize energy consumption throughout the facility.
Success Example:
A large-scale food factory adopted a comprehensive water conservation and waste recycling system. This initiative not only reduced operational water costs by 15% but also secured environmental certifications that enhanced the brand’s reputation.
5. Enhanced Employee Training Drives Safety and Quality
1. Fast Production to Meet Market Demand
Implementation Steps and Tool Recommendations:
- Data Analysis and Forecasting:
- Use sales data and market trend analytics tools (such as Tableau or Power BI) to forecast product demands.
- Adjust production schedules in real time based on forecast results and historical demand patterns.
- Automation and Smart Production:
- Introduce automated production lines utilizing programmable logic controllers (PLCs) to monitor real-time production speeds.
- Integrate smart scheduling systems to align production output with market demand fluctuations.
Success Example:
A well-known fast-food chain implemented a big data analysis platform that synchronized production schedules with real-time sales data. As a result, the production efficiency increased by 20% while reducing material waste caused by inaccurate demand forecasting.
2. Preventative Equipment Maintenance to Reduce Downtime
Implementation Steps and Tool Recommendations:
- Routine Inspection Protocols:
- Develop and enforce weekly and monthly maintenance checklists for each piece of equipment.
- Document and track maintenance history using computer maintenance management systems (CMMS).
- Smart Monitoring Systems:
- Deploy IoT sensors (e.g., temperature, vibration, pressure sensors) to continuously monitor equipment health.
- Set up automated alerts so maintenance teams can address issues before they lead to breakdowns.
Success Example:
A food processing plant incorporated IoT sensors and a CMMS, which enabled early fault detection. This proactive approach led to a 30% reduction in downtime, cutting unexpected repairs and avoiding costly disruptions in the production line.
3. Optimized Process Design Boosts Efficiency
Implementation Steps and Tool Recommendations:
- Streamlined Workflow Design:
- Utilize process flow diagram tools such as Microsoft Visio or Lucidchart to map and optimize production line processes.
- Review and update the layout regularly to ensure smooth transitions between stages.
- Ergonomic Tools and Specialized Equipment:
- Invest in ergonomically designed tools and fixtures tailored to specific production tasks, reducing worker fatigue and error rates.
- Implement automated guided vehicles (AGVs) for efficient transportation of raw materials and finished products, minimizing manual handling.
Success Example:
A medium-sized food manufacturer restructured its production line by integrating AGVs and ergonomic tools. This redesign cut the production cycle by 25% while reducing labor intensity, leading to notable efficiency improvements.
4. Water Conservation and Waste Reduction for Environmental and Cost Benefits
Implementation Steps and Tool Recommendations:
- Water Recycling Systems:
- Install water treatment and recycling systems to ensure the purity and reuse of water within production processes.
- Monitor water usage with real-time management software to identify areas for further savings.
- Food Waste Management:
- Create a systematic approach to segregate and recycle production waste.
- Explore opportunities to repurpose food waste for energy generation (e.g., anaerobic digestion) or composting.
- Energy Efficiency Monitoring:
- Implement energy management systems (like Schneider Electric’s EcoStruxure) to monitor and optimize energy consumption throughout the facility.
Success Example:
A large-scale food factory adopted a comprehensive water conservation and waste recycling system. This initiative not only reduced operational water costs by 15% but also secured environmental certifications that enhanced the brand’s reputation.
5. Enhanced Employee Training Drives Safety and Quality
Implementation Steps and Tool Recommendations:
Set up a real-time feedback mechanism for workers to report challenges and suggest improvements.
Regular Training and Assessments:
Develop detailed training programs covering new tools, technologies, and safety protocols.
Implement regular assessments to ensure employees are proficient in the use of updated equipment and methods.
Online Learning Platforms:
Establish an internal online training hub with video tutorials, simulation exercises, and up-to-date resources for continuous learning.
Use interactive e-learning modules to provide hands-on virtual experiences.
On-site Practical Training and Feedback Loops:
Combine classroom training with on-site practice to solidify new skills.
Components and processes of a food production line.
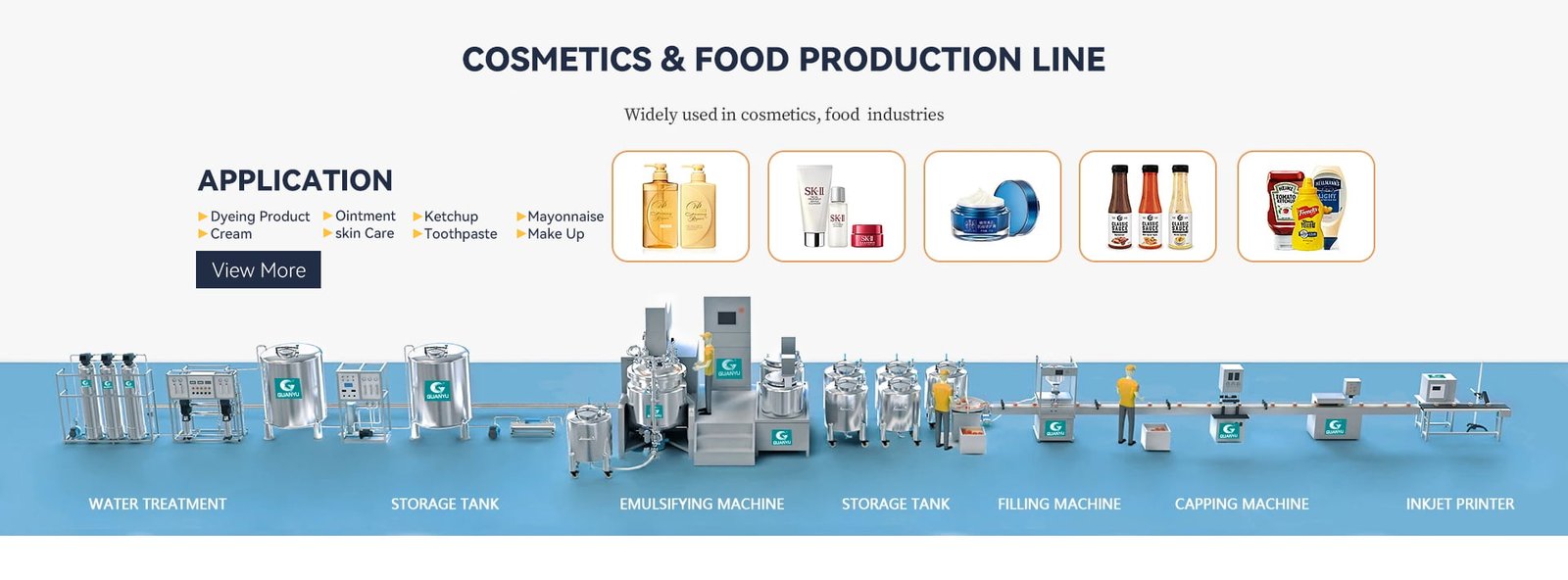
Wasserversorgung: Keeping Water Clean from the Start
Water is used in many food products. Clean water is important for safe and good-quality food. Treating water well stops problems like contamination or recalls. This can be done by setting water rules and using better cleaning tools. For example:
Dirty water can ruin food and slow production.
Checking water often keeps it safe and follows rules.
In industries like medicine, strict rules like USP ensure clean water. These rules help factories stay safe and avoid problems. By using good water systems, you can make your food production faster and safer.
Storage Tanks: Safe Places for Food and Ingredients
Storage tanks keep food and ingredients fresh and safe. Following clean rules makes storage tanks work better. Good habits include:
Best Practice | What It Means |
---|---|
Food Rotation | Use old items first to stop waste. |
Temperaturregelung | Keep tanks between 50°F and 70°F to avoid spoilage. |
Humidity Management | Keep air dry (below 15%) to stop mold. |
Sunlight Prevention | Keep food away from sunlight to save nutrients. |
Risk Reduction Storage | Store food off the floor and away from walls for easy cleaning. |
Pest Prevention | Close gaps and clean to keep pests away. |
Using these tips helps storage tanks stay clean and keep food production running smoothly.
Emulsifying Machine: Mixing Ingredients Perfectly
Emulsifying machines mix ingredients into smooth, even blends. These machines make sure food looks and tastes the same every time. Important things to check include:
Metric | What It Checks |
---|---|
Checks if the mixture stays smooth over time. | |
Breakdown Mechanisms | Finds problems like separating or clumping in the mixture. |
Special features, like vacuum systems, stop air bubbles and make better blends. These machines are used in food, medicine, and beauty products. Using good emulsifying machines helps you control mixtures and improve food production.
Abfüllmaschine: Accurate and Efficient Product Dispensing
Filling machines help make food production faster and more exact. They put the right amount of product into containers, cutting waste and keeping things consistent. With smart features, these machines improve how factories work.
Main features of modern filling machines are:
Piston Mechanism: Measures and fills liquids, pastes, or powders exactly.
Automatic Changeovers: Quickly switches between products and container sizes.
Level Control Systems: Stops overfilling or underfilling by keeping levels steady.
Data Integration: Tracks and manages the filling process in real-time.
Automated Cleaning Systems: Makes cleaning easier and lowers contamination risks.
Besonderheit | What It Does |
---|---|
Piston Mechanism | Fills containers with the exact amount of product. |
Automatic Changeovers | Changes between products and containers quickly, saving time. |
Level Control Systems | Keeps product levels steady to avoid filling mistakes. |
Data Integration | Watches and controls the process live for better results. |
Automated Cleaning Systems | Simplifies cleaning and keeps operations hygienic. |
These machines save resources and allow flexibility. They handle different products and containers, making production lines ready for new demands.
Verschließmaschine: Securing Product Integrity
Capping machines keep products sealed and safe during storage and shipping. They help maintain quality and build trust with customers. Regular care and proper setup are key for good results.
To improve capping, focus on these points:
Pick the right capping machine for your product and packaging.
Follow a maintenance plan to keep machines working well.
Use data to check performance and ensure quality.
Key Aspect | What It Means |
---|---|
Equipment Selection | Choosing the right machine ensures efficiency and product safety. |
Regular Maintenance | Keeping machines in good shape ensures they work reliably. |
Data Analytics for Quality Control | Using data helps track performance and maintain high standards. |
By following these tips, you can make capping more efficient and meet top quality standards.
Inkjet Printer: Batch Coding and Product Traceability
Inkjet printers are used for batch coding and tracking products. They print clear codes on items, helping meet rules and improve supply chain tracking. New printing tech makes them more accurate and efficient.
The inkjet printer market is growing fast. In 2023, it was worth $3.1 billion and could reach $5.2 billion by 2032, growing 5.6% yearly. This growth comes from the need for better tracking and stricter rules.
Market Size (2023) | Projected Size (2032) | Growth Rate (%) | Why It’s Growing |
---|---|---|---|
$3.1 billion | $5.2 billion | 5.6 | Demand for tracking, better tech, and strict rules |
By using advanced inkjet printers, you can improve product safety and meet customer needs. These printers also protect brands by printing clear, accurate codes on every item.
Emerging Technologies for Food Production Efficiency
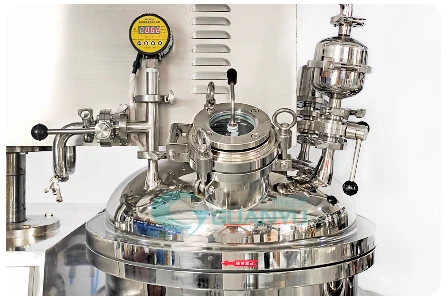
Industry 4.0 and Its Role in Food Production Line
Industry 4.0 is changing how food factories work. It uses smart tools to make production faster and cheaper. Robots, automation, and data systems help improve efficiency. Machines can do repetitive jobs, so workers can focus on quality and new ideas.
Industry 4.0 improves many areas of food production:
Performance Metric | What It Means |
---|---|
Better control of processes for smoother operations. | |
Throughput Time | Faster production cycles save time. |
Lead Time Reduction | Quicker delivery of products to customers. |
Operating Costs | Lower costs due to smart machines and systems. |
Quality and Safety Measures | Cleaner and safer food with automated checks. |
Productivity and Operational Efficiency | More output and better use of resources. |
Waste Reduction | Less waste and energy use, helping the environment. |
Demand Forecasting | Predicting customer needs to match production levels. |
Using Industry 4.0 tools helps factories work better, waste less, and make more while keeping food quality high.
IIoT: Real-Time Monitoring for Better Control
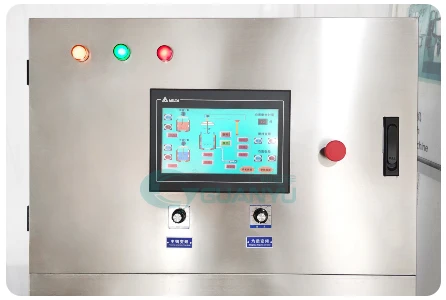
The Industrial Internet of Things (IIoT) connects machines and systems. It lets factories watch and control production in real-time. Sensors check things like temperature, humidity, and stock levels. These tools give useful information to improve production.
IIoT can warn about problems in the supply chain, keeping things running smoothly. It also predicts when machines need fixing, reducing downtime. Using IIoT makes food production faster and keeps quality consistent.
AI and Machine Learning: Smarter Food Production
Artificial intelligence (AI) and machine learning (Ml) help factories plan better. They study data to find patterns and predict future needs. This helps factories adjust production to match demand.
AI tools cut waste and save money by using resources wisely. For example, they can spot machine problems early, so repairs happen before breakdowns. This keeps production running smoothly.
Adding AI and ML to food production improves efficiency and quality. These tools help factories stay competitive and deliver great products.
Optimizing Equipment and Layout in Food Production Lines
Custom Equipment for Specific Needs
Special machines solve unique problems in food factories. Custom tools help machines work better for specific tasks. Adding AI and IoT to machines improves checking and quality. This makes work faster and meets customer needs.
Companies like DC Norris North America make tools based on batch size, cooking time, and packaging. This custom design makes work easier and faster. More factories now want special tools like twin screw extruders. Toolmakers are working hard to create better machines for changing needs.
Key Findings | Details |
---|---|
Increased Investment | |
New tools are made for specific factory needs. | |
Demand for Technical Products | Special tools like extruders are becoming more popular. |
Smart Layouts to Reduce Delays
Good factory layouts cut delays and keep work moving. Placing machines smartly helps teams work together better. This avoids problems and keeps things running smoothly.
Smart layouts also save money and improve safety. For example, better material flow stops slowdowns. A clear layout helps organize the workspace and reach goals faster with less waste.
Updating Old Systems for Better Results
Old machines can slow work and cost more to fix. Upgrading them makes work faster and meets new rules. New machines are safer, easier to upgrade, and work well with modern tools.
Studies show 74% of factories have problems with old systems. Upgrades can make work 33% faster and cut costs by 25% in a year. New tools also predict problems and fix them early. This saves money and keeps food production running smoothly.
Waste Reduction and Sustainability in Food Manufacturing
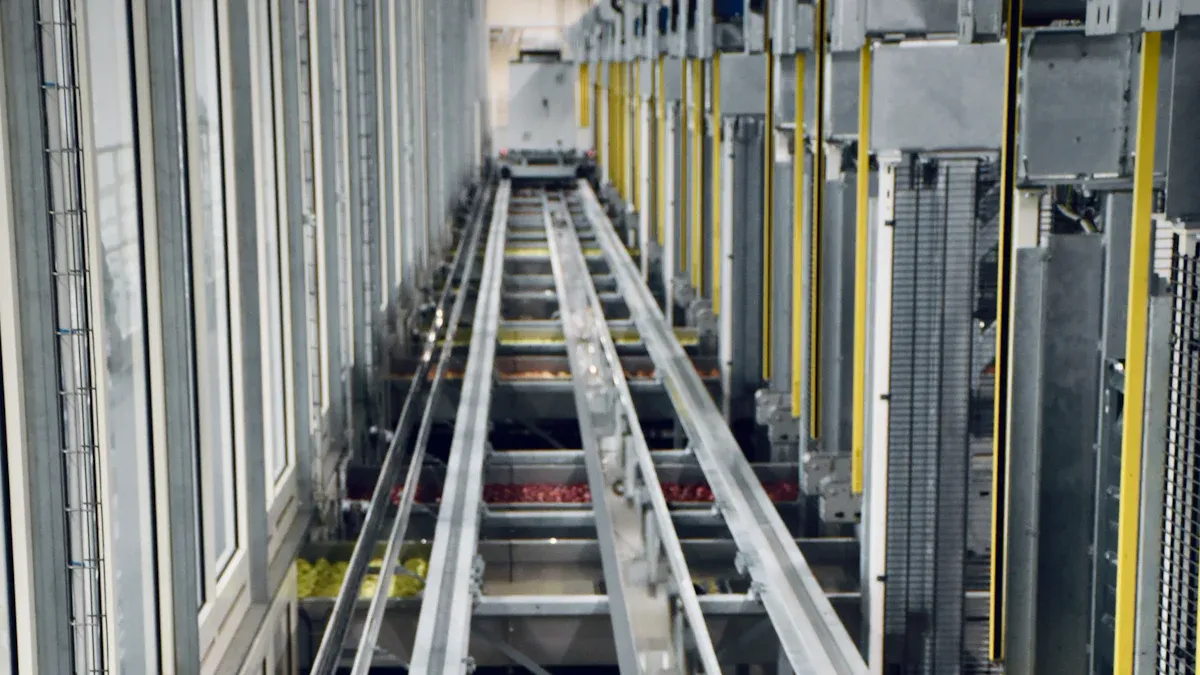
Saving Water to Help the Environment
Saving water is important for better production and sustainability. Using less water lowers energy use and cuts pollution. This helps nature and keeps water available for making food.
It supports areas with little water, keeping farms and jobs steady.
Using less water avoids slowdowns caused by shortages.
Using smart tools like better cleaning systems and water recycling can improve factory work. These methods save money and help the environment for the future.
Cutting Food Waste with Better Stock Management
Food waste is a big problem in factories. Managing stock wisely can fix this issue. Real-time tracking shows how much stock you have and stops overproduction. This saves resources and reduces waste.
Using first-in, first-out (FIFO) rules helps use older items first. This stops spoilage and keeps products fresh for customers. Predictive tools can guess demand, so you make just enough and avoid waste.
Cutting food waste makes factories more efficient and shows customers you care about the planet.
Turning Waste into Useful Resources
Recycling waste can turn it into something valuable. This supports a system where materials are reused instead of thrown away. For example, food waste can become compost or fuel, which helps the environment.
Source | What It Says |
---|---|
Talks about reusing and recycling to cut waste in food factories. | |
Closing the Loop: How Circular Economy Approaches Can Tackle Food Waste and Promote Sustainability | Explains composting and making fuel from food waste to help the planet. |
Circular Economy in the Food Chain: Production, Processing and Waste Management | Focuses on recycling nutrients and byproducts to reduce waste. |
By recycling and reusing, factories can avoid problems from resource shortages. This also helps the planet and makes production better.
Maintenance and Monitoring for Production Efficiency
Predictive Maintenance to Prevent Downtime
Predictive maintenance stops machines from breaking unexpectedly. It uses data and smart tools to check machine health. Sensors and programs predict when a machine might stop working. Fixing problems early avoids stopping production.
Predictive maintenance can cut breakdowns by 70% and save 25% on repairs, says Deloitte.
Sensors send live updates about machines, helping workers act fast.
Data tools find issues early, keeping production smooth and efficient.
Using predictive maintenance saves time, lowers costs, and keeps machines running well.
Real-Time Data Tracking for Proactive Decision-Making
Real-time tracking shows live updates about your production process. This helps you make quick choices in a busy food factory.
Benefits of real-time tracking include:
Spotting problems fast to avoid bigger delays.
Making smart decisions to adjust plans and resources quickly.
Boosting equipment performance by fixing slowdowns.
Adapting to market needs to meet customer demands.
For example, checking key performance numbers helps find and fix problems. Real-time tracking helps you stay ready and keep high standards.
Using Digital Twins to Simulate and Optimize Processes
Digital twins are computer models of your production systems. They let you test ideas without stopping real work. By trying different setups, you can find ways to save time and money.
These models help you:
See how changes will affect production before trying them.
Test new layouts or tools to avoid costly mistakes.
Watch and improve processes live for better results.
Digital twins are great for improving production and staying ahead in food manufacturing.
Workforce Training and Safety in Food Production Lines
Teaching Workers About New Technologies
Training workers on new tools is very important. Modern tools like AI and IoT make food production faster and safer. But, workers need to know how to use them well.
When workers learn these tools, they can spot problems early. This keeps products safe and improves work speed. Studies show AI helps make better products and find risks early. Training workers is a smart way to improve your factory.
To make training better:
Use practice sessions to teach new systems.
Offer help when workers face problems.
Let workers share ideas and tips with each other.
Making Safety Rules for Workers and Products
Safety rules keep workers safe and products high-quality. The food industry uses strict rules like HACCP to stop dangers. These rules make sure every step is safe.
Proof Type | What It Means |
---|---|
Safety Rules | Keep workers safe and products good. |
HACCP Rules | Find dangers and set safety steps for food. |
Worker Training | Teach workers their role in keeping things safe and high-quality. |
People want safe, good food. They trust factories to follow safety rules. Training workers on safety builds trust and lowers risks in production.
Supporting Learning and New Ideas
Encouraging learning and new ideas keeps workers happy and skilled. When workers learn new things, they stay excited and ready for changes. This also helps keep workers longer and makes work more fun.
Learning helps workers grow and improve.
Workers who share ideas feel proud and involved.
Fun training methods, like Airbnb’s, improved worker stay by 35%.
By focusing on learning, you help your team work smarter and bring new ideas to food production.
Continuous Improvement in Food Production Efficiency
Using Data Analysis to Find Better Ways
Data analysis helps improve how food factories work. By studying production data, you can find problems and fix them. Some helpful methods include:
Method | What It Does |
---|---|
Statistical Process Control | Tracks process changes with charts. It spots issues early and helps fix them fast. |
Six Sigma | Uses teams and stats to cut problems and boost performance. |
Lean Manufacturing | Cuts waste by removing steps that don’t add value. |
New tools also help analyze data. These tools watch production lines, study data, and adjust things quickly. They find slow spots, save food, and make work faster. Using these tools helps factories work better all the time.
Improving Step by Step with Feedback
Feedback is key to making food production better. It helps test ideas, check results, and improve processes. Start by collecting data from your factory. Use it to find what needs fixing. Make changes and see how they work.
For example, if one machine slows things down, change its settings or move workers around. After trying this, check if it helped. Keep repeating this process to stay ready for new challenges.
Using feedback loops helps factories stay efficient and meet high standards.
Working with Experts Like Guanyu for Custom Solutions
Teaming up with experts can speed up improvements. Guanyu makes special machines to solve factory problems. Their tools are designed to fit your needs and improve efficiency.
Guanyu’s machines, like mixers and fillers, make production faster and keep quality high. With over 35 jahrelange Erfahrung, they offer trusted solutions for tough markets.
Working with experts like Guanyu helps your factory run smoothly and stay ahead in the industry.
Making food production better needs smart tools, less waste, and trained workers. Cool tools like prediction models and quality charts help plan better and stop mistakes. These ideas make work faster and save money, as shown below:
Plan | What It Helps With |
---|---|
Smart Data Checks | Cuts down on checking costs |
Learning from Data | Makes factories adjust faster |
Prediction Models | Helps plan and organize work |
Quality Charts | Stops mistakes and fixes problems early |
Multi-Data Study | Finds hidden chances to improve |
Improvement | How Much Better It Gets |
---|---|
Fewer mistakes in products | |
Less time fixing broken machines | 20-35% |
Faster production | 5-15% |
Lower checking costs | 10-25% |
Quicker new product launches | Better understanding of processes |
Always finding ways to improve keeps your factory strong. Working with experts like Guanyu gives you special tools for your needs. Start now to make your factory the best by 2025!
FAQ
How can food factories work faster and better?
Using smart tools like AI, IoT, and predictive maintenance helps. These tools make processes smoother, cut downtime, and improve product quality. Custom machines and smart layouts also make factories more efficient.
What does predictive maintenance do for food factories?
Predictive maintenance finds machine problems before they happen. It stops sudden breakdowns, lowers repair costs, and keeps production running smoothly. This helps factories avoid delays and save money.
Why is being eco-friendly important in food factories?
Eco-friendly practices protect nature and save resources for the future. Saving water, cutting waste, and recycling help the planet. These actions also meet customer and rule expectations, making your brand stronger.
How do special machines help food factories?
Special machines are made for specific factory needs. They work better, waste less, and make more products. These machines also work well with new technology, improving how factories run.
Why is worker training important for food factories?
Training teaches workers to use new tools safely and correctly. It reduces mistakes, improves safety, and increases productivity. Trained workers handle changes better, keeping production steady and efficient.