The beauty industry is a multifaceted and dynamic sector that constantly evolves to meet consumer demands and trends. Among the myriad of tools and equipment essential to this industry, the blending machine stands out as a critical component in the production process. Blending machines, also known as mixers or blending kettles, play a pivotal role in ensuring the quality, Konsistenz, and effectiveness of a wide range of beauty products. This article explores the various applications of blending machines in the beauty industry, highlighting their importance in the manufacturing of cosmetics, skincare products, perfumes, and more.
Introduction to Blending Machines
Blending machines are industrial devices designed to mix, blend, or homogenize various ingredients to create a uniform product. These machines come in different sizes and configurations, each suited to specific types of products and production scales. In the beauty industry, blending machines are used to combine raw materials, active ingredients, and other additives to produce a wide array of beauty and personal care products.

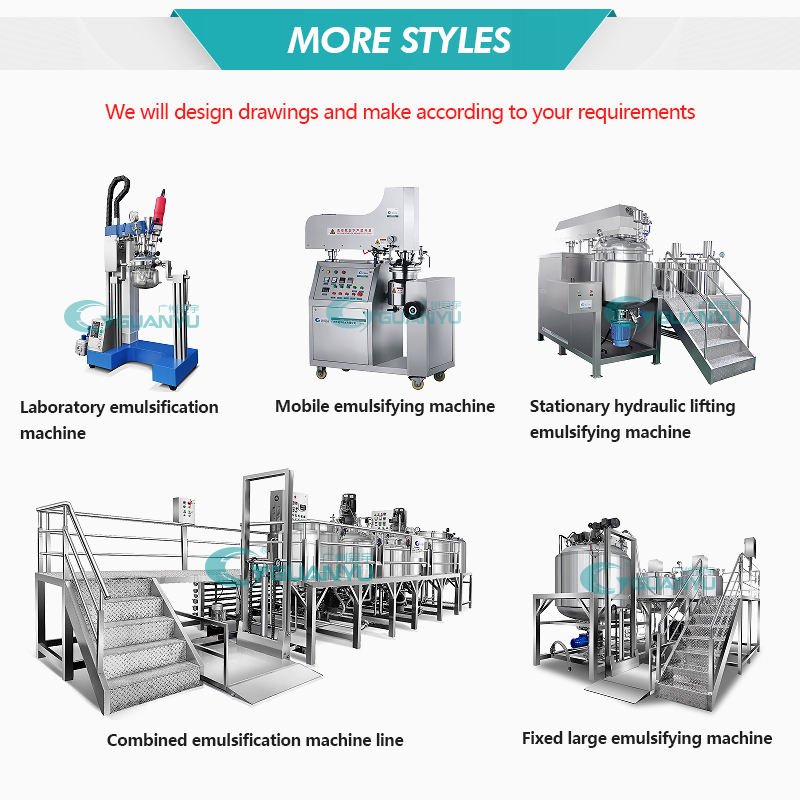
Types of Blending Machines
There are several types of blending machines used in the beauty industry, each serving a specific purpose:
- Ribbon Blenders: These machines use helical ribbons to mix ingredients thoroughly. They are ideal for powder blending and are commonly used in the production of dry cosmetics such as face powders and eyeshadows.
- Planetary Mixers: These mixers have an agitator that moves around the bowl in a planetary motion, ensuring even mixing. They are often used for thick, viscous products like creams, Lotionen, und Salben.
- High-Shear Mixers: High-shear mixers are used to emulsify, homogenize, and disperse ingredients. They are essential for producing emulsions, such as moisturizers and sunscreens, where oil and water phases need to be uniformly mixed.
- Vacuum Emulsifying Mixers: These mixers operate under vacuum conditions to remove air bubbles and ensure a smooth, high-quality product. They are commonly used in the production of high-end skincare products and pharmaceuticals.
Key Applications in the Beauty Industry
Blending machines are integral to various stages of product development and manufacturing in the beauty industry. Here are some key applications:
1. Cosmetics Manufacturing
The production of cosmetics such as foundations, eyeshadows, blushes, and lipsticks relies heavily on blending machines. These products require precise mixing of pigments, binders, fillers, and other additives to achieve the desired texture, color, and performance. Blending machines ensure that the ingredients are evenly distributed, resulting in a consistent and high-quality product.
For instance, in the production of foundation, a blending machine mixes pigments with emollients, stabilizers, and preservatives to create a smooth, homogeneous product that can be easily applied to the skin. Similarly, in eyeshadow production, ribbon blenders are used to mix fine powders and pigments to achieve a uniform color and texture.
2. Skincare Product Production
Skincare products, including moisturizers, serums, cleansers, and masks, require meticulous blending of active ingredients, emulsifiers, and bases. Blending machines play a crucial role in ensuring that these products are stable, effective, and pleasant to use.
In the creation of moisturizers, for example, high-shear mixers are used to emulsify oil and water phases, creating a stable emulsion that hydrates and nourishes the skin. For serums, which often contain high concentrations of active ingredients, planetary mixers ensure that the ingredients are evenly distributed without compromising their potency.
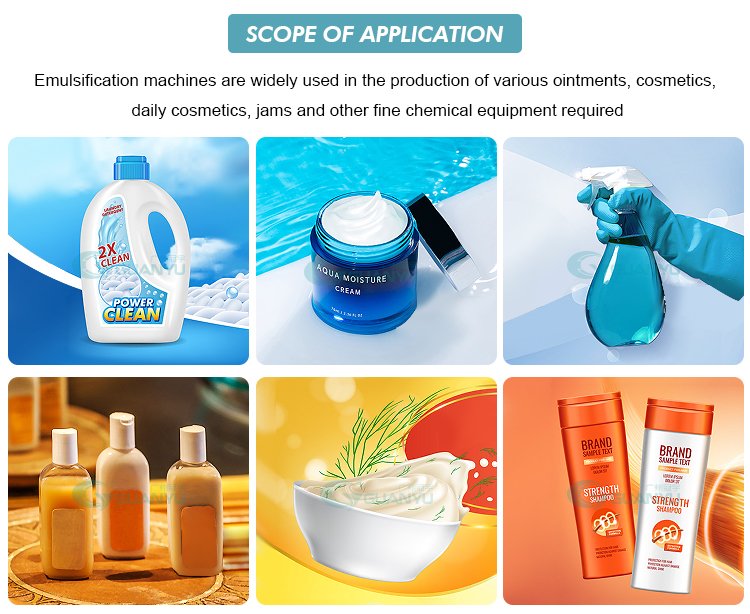
3. Perfume and Fragrance Blending
The art of perfume making involves the precise blending of various aromatic compounds to create unique and appealing scents. Blending machines are used to mix essential oils, Alkohol, and other solvents to achieve a consistent fragrance.
Perfume blending requires careful control of the mixing process to ensure that the final product has a balanced and lasting scent. Blending machines help achieve this by ensuring that the different fragrance notes are evenly distributed and well-integrated.
4. Pharmaceutical and Cosmeceutical Production
In the production of cosmeceuticals and pharmaceutical products, blending machines are essential for mixing active pharmaceutical ingredients (APIs) with excipients to create stable and effective formulations. These products often require precise dosing and thorough mixing to ensure their therapeutic efficacy.
Vacuum emulsifying mixers are particularly valuable in this context, as they can produce high-quality emulsions and gels that are free from air bubbles, ensuring a smooth and uniform product.
5. Batch and Continuous Production
Blending machines are used in both batch and continuous production processes in the beauty industry. Batch production involves mixing ingredients in discrete batches, while continuous production involves a continuous flow of materials through the mixing process.
Batch production is commonly used for small-scale or specialized products, allowing for flexibility in formulation and production. Continuous production, on the other hand, is suited for large-scale manufacturing, providing efficiency and consistency for high-demand products.
The Importance of Blending Machines in Quality Control
Quality control is paramount in the beauty industry, as consumers expect safe, effective, and high-quality products. Blending machines play a vital role in ensuring product quality by:
- Ensuring Uniformity: Blending machines ensure that all ingredients are evenly distributed, resulting in a uniform product. This uniformity is crucial for product performance and consumer satisfaction.
- Enhancing Stability: Proper mixing helps stabilize emulsions, suspensions, and other formulations, preventing separation and ensuring the product remains effective throughout its shelf life.
- Improving Texture and Consistency: The texture and consistency of beauty products are critical to their usability and appeal. Blending machines help achieve the desired texture, whether it’s a smooth cream, a silky serum, or a fine powder.
- Controlling Air Incorporation: Vacuum emulsifying mixers remove air bubbles during the mixing process, ensuring a smooth and high-quality product. This is particularly important for products like creams and gels, where air bubbles can affect texture and appearance.
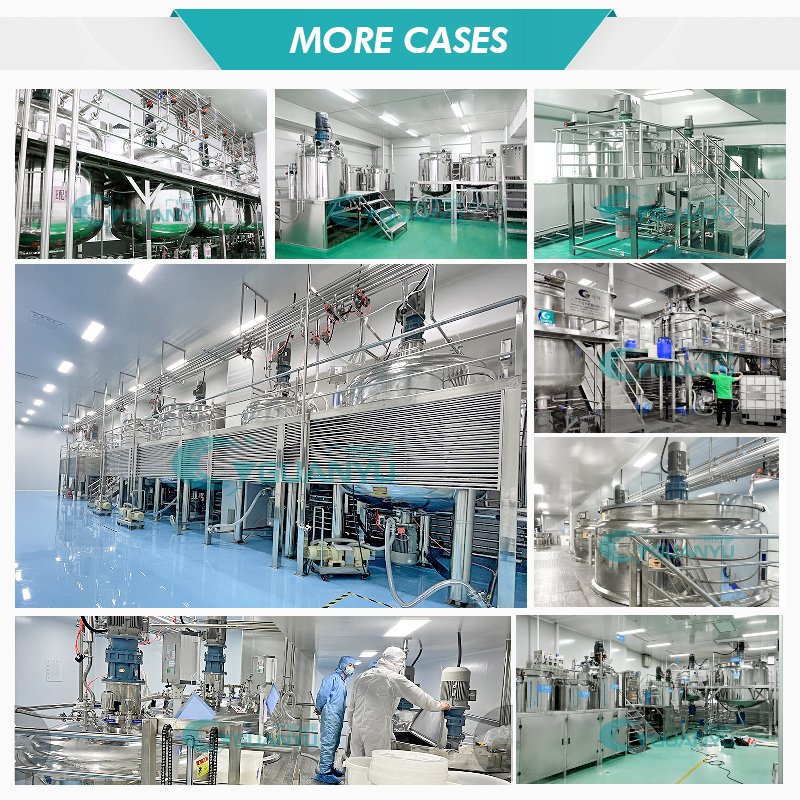
Advances in Blending Technology
The beauty industry continuously seeks to innovate and improve production processes. Advances in blending technology have led to more efficient and versatile blending machines, offering numerous benefits:
- Automatisierung und Steuerung: Modern blending machines often feature automated controls and programmable settings, allowing for precise control over mixing parameters such as speed, Zeit, and temperature. This automation enhances consistency and reduces the risk of human error.
- Scalability: Blending machines are available in various sizes, from small laboratory-scale units to large industrial-scale equipment. This scalability allows manufacturers to efficiently scale up production to meet market demand.
- Hygienic Design: Advances in hygienic design ensure that blending machines are easy to clean and sanitize, reducing the risk of contamination. This is particularly important in the beauty industry, where product safety and hygiene are paramount.
- Energieeffizienz: Modern blending machines are designed to be energy-efficient, reducing operational costs and minimizing environmental impact. Energy-efficient designs also contribute to sustainable manufacturing practices.
Challenges and Considerations
While blending machines offer numerous benefits, there are also challenges and considerations to keep in mind:
- Ingredient Compatibility: Different ingredients may have varying properties and compatibilities, requiring careful selection of blending equipment and parameters to ensure effective mixing.
- Heat Sensitivity: Some active ingredients and formulations may be sensitive to heat generated during the mixing process. Blending machines with temperature control features can help mitigate this issue.
- Reinigung und Wartung: Regular cleaning and maintenance of blending machines are essential to prevent contamination and ensure consistent performance. This requires proper training and adherence to hygiene protocols.
- Regulatory Compliance: The beauty industry is subject to stringent regulatory requirements. Manufacturers must ensure that their blending processes and equipment comply with relevant regulations and standards to ensure product safety and quality.
Abschluss
Blending machines are indispensable tools in the beauty industry, enabling the production of a wide range of high-quality, consistent, and effective products. From cosmetics and skincare to perfumes and pharmaceuticals, these machines play a critical role in mixing and homogenizing ingredients, ensuring that the final products meet the expectations of consumers and regulatory standards.
As the beauty industry continues to evolve, advances in blending technology will further enhance the efficiency, versatility, and sustainability of production processes. Manufacturers who invest in modern, high-quality blending machines will be well-positioned to meet the demands of an increasingly discerning and dynamic market.