The cosmetics industry is a rapidly growing sector, continually evolving to meet consumer demands for innovative and high-quality products. One of the critical elements in the production of these products is the mixing blending tank. These tanks play a pivotal role in ensuring the consistency, stability, and quality of cosmetic products. This article explores the application of mixing blending tanks in the cosmetics industry, highlighting their importance, functionality, and impact on product development.
Introduction to Mixing Blending Tanks in Cosmetics
Mixing and blending tanks have become indispensable tools in the cosmetics industry, reflecting a long history of technological evolution designed to meet the sector’s unique demands. Initially, the use of rudimentary containers for manual mixing sufficed, but as the industry grew, so did the need for more sophisticated equipment. Modern mixing and blending tanks are the result of this continuous advancement, tailored to enhance the efficiency and quality of cosmetic manufacturing processes.
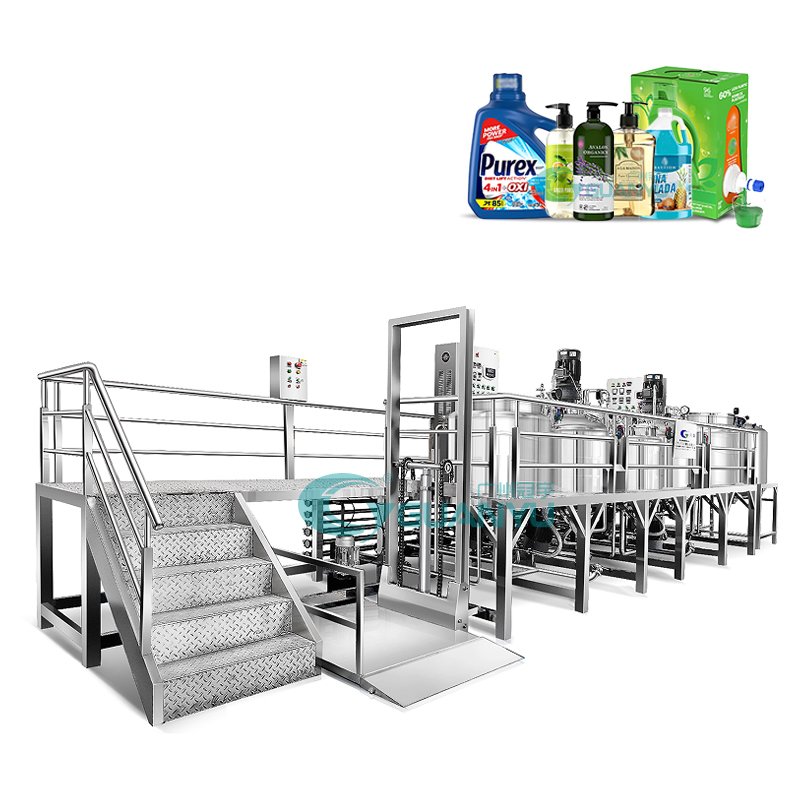
These tanks are primarily constructed from durable materials such as stainless steel, which offers excellent resistance to corrosion and contamination, ensuring the purity of the cosmetic products. Available in various sizes and capacities, these tanks can cater to both small-scale and large-scale production needs, making them versatile assets in any manufacturing setup.
The primary function of mixing and blending tanks is to homogenize ingredients, ensuring a consistent texture and composition throughout the product. This is crucial in the cosmetics industry, where uniformity in texture and appearance is vital for consumer satisfaction. The tanks facilitate the preparation of large batches of products, significantly improving production efficiency and scalability.
Beyond homogenization, these tanks play a crucial role in maintaining the quality and safety standards of cosmetic products. By providing a controlled environment for mixing, they help minimize contamination risks and ensure that the final product meets stringent regulatory requirements. This aspect is particularly important given the sensitive nature of cosmetic formulations, which often include active ingredients that must be precisely blended to achieve the desired effect.
In conclusion, the integration of mixing and blending tanks into the cosmetics manufacturing process represents a significant advancement in the industry. These tanks not only streamline production but also uphold the high-quality standards expected by consumers, making them essential tools in the creation of safe and effective cosmetic products.
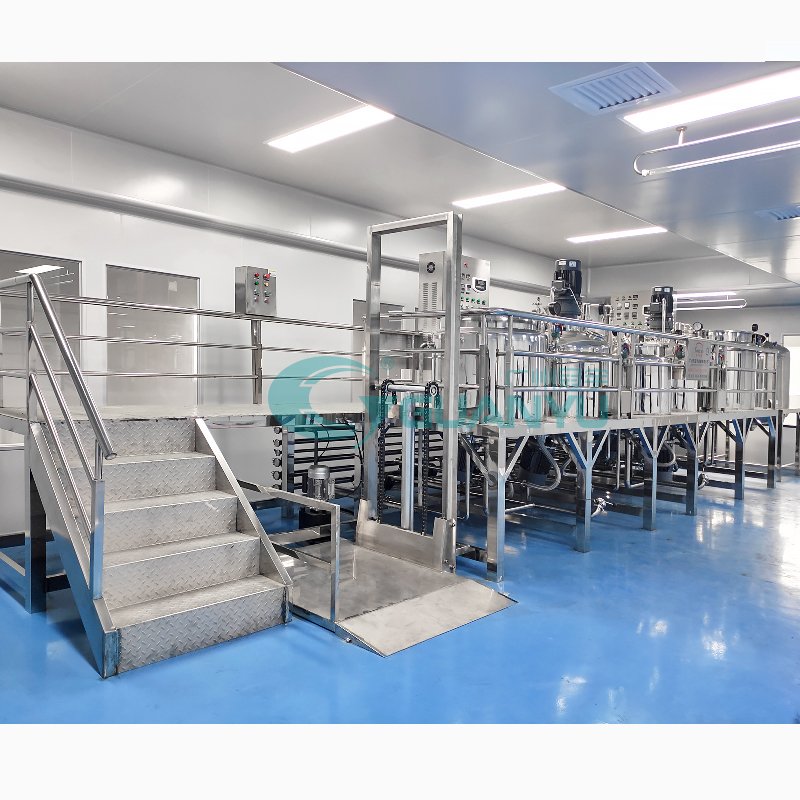
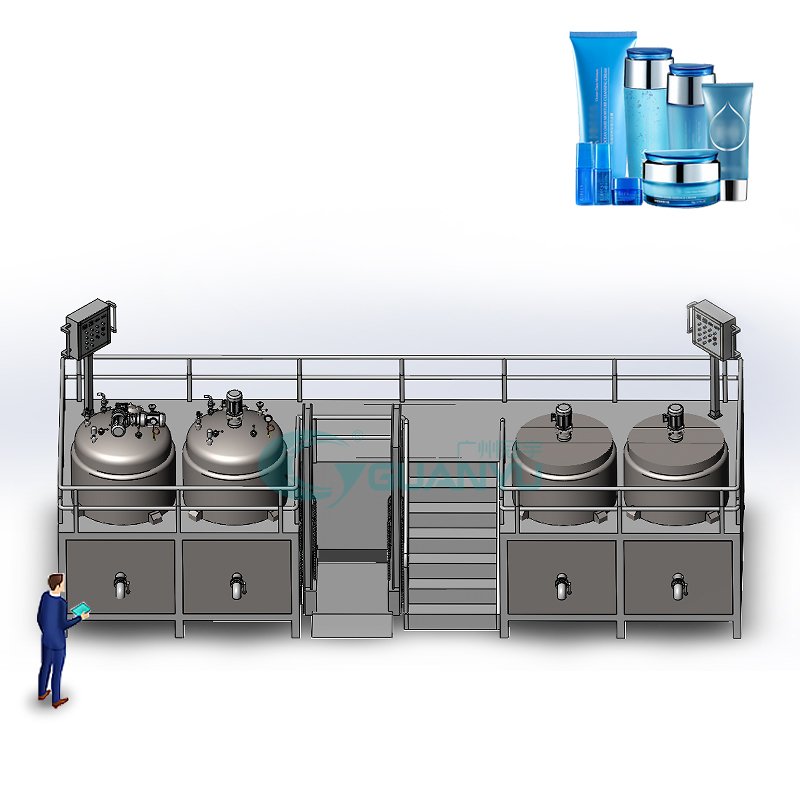
Key Applications and Benefits in Cosmetic Manufacturing
Mixing and blending tanks serve as essential equipment in the cosmetics industry, playing a critical role in the production of a wide array of products, including lotions, creams, shampoos, and makeup. These tanks are designed to handle the precise mixing of active ingredients, fragrances, and colorants, ensuring that each product meets the desired consistency and efficacy. The ability to uniformly blend components is vital for maintaining the quality and performance of cosmetic products, which directly impacts consumer satisfaction.
One of the primary applications of mixing and blending tanks in cosmetics is in the formulation stage. These tanks enable manufacturers to combine various ingredients under controlled conditions, ensuring that the final product is homogeneous and stable. For instance, in the production of lotions and creams, the tanks facilitate the emulsification process, allowing water and oil-based components to blend seamlessly. Similarly, in shampoo manufacturing, these tanks ensure that surfactants, conditioners, and fragrances are evenly distributed, providing a consistent product with every batch.

Scaling up production from small lab batches to full-scale manufacturing is another significant benefit of using mixing and blending tanks. These tanks are designed to replicate lab-scale formulations accurately, allowing for a smooth transition to mass production. This scalability ensures that the final products maintain their intended properties, such as texture, viscosity, and fragrance, regardless of the production volume.
Moreover, the use of mixing and blending tanks offers several advantages, including improved product quality, enhanced efficiency, and reduced production costs. The ability to automate mixing processes minimizes human error and ensures consistency across batches. Additionally, these tanks are often equipped with advanced features such as temperature control, which is crucial for maintaining the stability of heat-sensitive ingredients.
Sanitation and easy cleaning are also critical considerations in cosmetic manufacturing. Mixing and blending tanks are designed with features that facilitate thorough cleaning and sterilization, helping manufacturers comply with industry regulations and maintain high standards of product safety. These features include smooth interior surfaces, easy access points, and automated cleaning systems, reducing the risk of contamination.