جدول المحتويات
Vacuum Emulsifying Mixer Buying Guide
أنا. Precisely Selecting the Most Suitable Vacuum Emulsifying Mixer
Procuring a vacuum emulsifying mixer is a meticulous process of matching the equipment with your specific requirements, necessitating a comprehensive consideration of multiple factors. As a processing manufacturer or end-user, the appropriate equipment selection directly impacts production efficiency and product quality. This comprehensive guide will methodically analyze the key considerations, facilitating a seamless procurement process tailored to your needs.
الثاني. Unveiling the Working Principle of Vacuum Emulsifying Mixers
2.1 Definition of Vacuum Emulsifying Mixer
A vacuum emulsifying mixer is a highly efficient device that harnesses the powerful stirring force generated by vacuum negative pressure to thoroughly blend and emulsify a diverse array of liquid and solid raw materials.
2.2 Principle Analysis
The device creates a vacuum environment within a sealed container, and the high-speed rotation of the stirring assembly generates a potent centrifugal force. This force causes the raw materials to be comprehensively dispersed and mixed, with particulate matter thoroughly emulsified, achieving a uniform and stable homogeneous mixture.
2.3 Application Areas
Vacuum emulsifying mixers find widespread applications across diverse industries, catering to a broad range of mixing and emulsifying requirements. These versatile machines are extensively utilized in the food and beverage sector for mixing and homogenizing ingredients like sauces, الضمادات, and dairy products. The pharmaceutical industry relies on vacuum emulsifying mixers to produce ointments, كريمات, and other topical formulations, ensuring precise emulsification and uniformity. في صناعة مستحضرات التجميل, these mixers are indispensable for creating emulsified lotions, كريمات, and other personal care products. بالإضافة إلى ذلك, vacuum emulsifying mixers play a crucial role in the chemical and paint industries, facilitating the mixing and dispersion of pigments, راتنجات, and other components.
ثالثا. Analysis of Various Types of Vacuum Emulsifying Mixers
Employing hydraulic power to drive the agitator’s vertical lifting and lowering motion, this type can facilitate intermittent feeding and discharging operations, offering convenient maintenance and suitability for high-viscosity materials.
3.2 Bottom Agitation Type
With the stirring assembly installed at the bottom of the conical vessel, this type features a feeding inlet and discharging door at the top, lending a compact structure and simple operation.
3.3 Inertia Rotor Type
Equipped with a high-speed rotating rotor, this type generates immense centrifugal force and stirring power, making it well-suited for viscous materials and shear-sensitive substances.
رابعا. Factors to Consider When Purchasing Vacuum Emulsifying Mixers
4.1 Type of Mixing Materials
Evaluating the physical and chemical properties of the mixing materials, such as viscosity, density, درجة حرارة, and other characteristics, is a prerequisite for matching the appropriate vacuum emulsifying mixer model. This initial assessment ensures compatibility and optimized performance.
4.2 Production Capacity Requirements
Based on the company’s production scale, batch sizes, and expected throughput, it is crucial to select vacuum emulsifying mixers with the appropriate vessel capacities and processing capabilities. Accurately determining production needs is paramount for efficient operations.
4.3 Automation and Human-Machine Interaction
Advanced vacuum emulsifying mixers incorporate automated control systems and user-friendly human-machine interfaces. During the selection process, it is essential to assess the desired level of automation and operational convenience to meet your specific workflow and staffing requirements.
4.4 Installation and Maintenance Considerations
Different vacuum emulsifying mixer models may vary in their installation space requirements, maintenance accessibility, and long-term operating costs. It is imperative to comprehensively evaluate these factors to ensure seamless integration, efficient servicing, and cost-effective operations.
4.5 Supplier Recommendation: آلات Guanyu
With decades of industry experience, Guanyu Machinery Company has amassed extensive expertise in the vacuum emulsifying mixer domain. They not only offer industry-leading products but can also tailor customized solutions to meet the unique needs of individual companies. Guanyu Machinery provides comprehensive lifecycle services and support, making them a trusted partner for both large enterprises and small-scale factories.
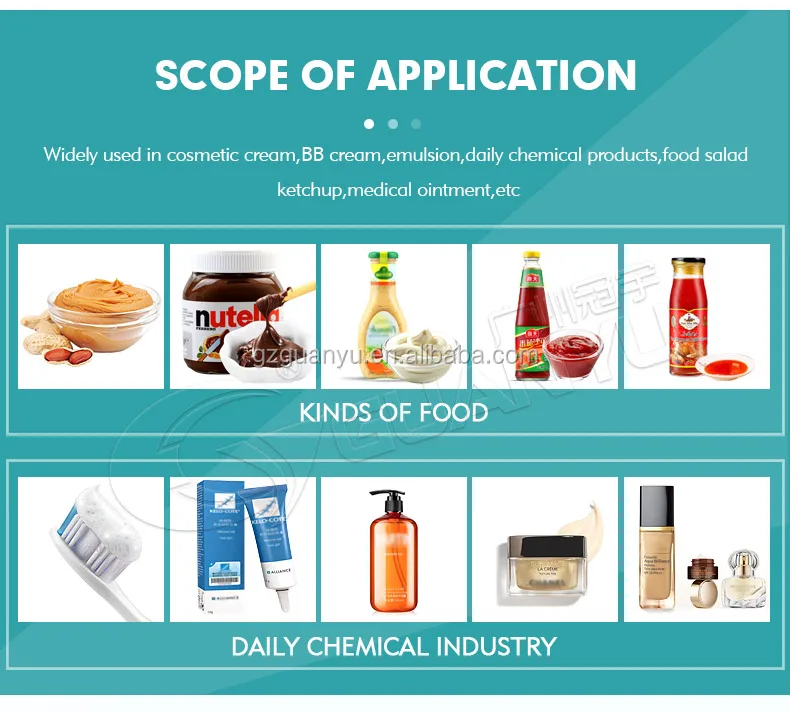
V. Key to Efficient Equipment Utilization
5.1 Standardized Installation Process
Following the equipment manual’s instructions, selecting a suitable location, and installing the mixer according to established norms will help avoid potential issues during subsequent use and operation.
5.2 Regular Maintenance and Servicing
Establishing a periodic maintenance plan is crucial. This includes regularly inspecting and replacing wear parts, calibrating and adjusting the equipment, and performing diagnostic checks to ensure optimal operating conditions at all times.
5.3 Operator Training and Skill Development
Providing comprehensive theoretical and hands-on training for operators is essential. By standardizing operating procedures and fostering a skilled workforce, human operational errors can be minimized to the greatest extent possible, further enhancing productivity and product quality.
VI. Take Action Now, Procure the Ideal Equipment
Now that you have a thorough understanding of the working principles, classifications, and selection criteria for vacuum emulsifying mixers, it’s time to take decisive action and embark on your procurement journey. شركة قوانيو للآلات will collaborate closely with you to tailor the optimal solution that aligns with your unique needs. Their team of experts will provide professional guidance throughout the selection process, ensuring a well-informed decision. Furthermore, Guanyu Machinery will offer comprehensive support services during installation, commissioning, and ongoing maintenance, ensuring a seamless transition and maximizing the performance and longevity of your investment.